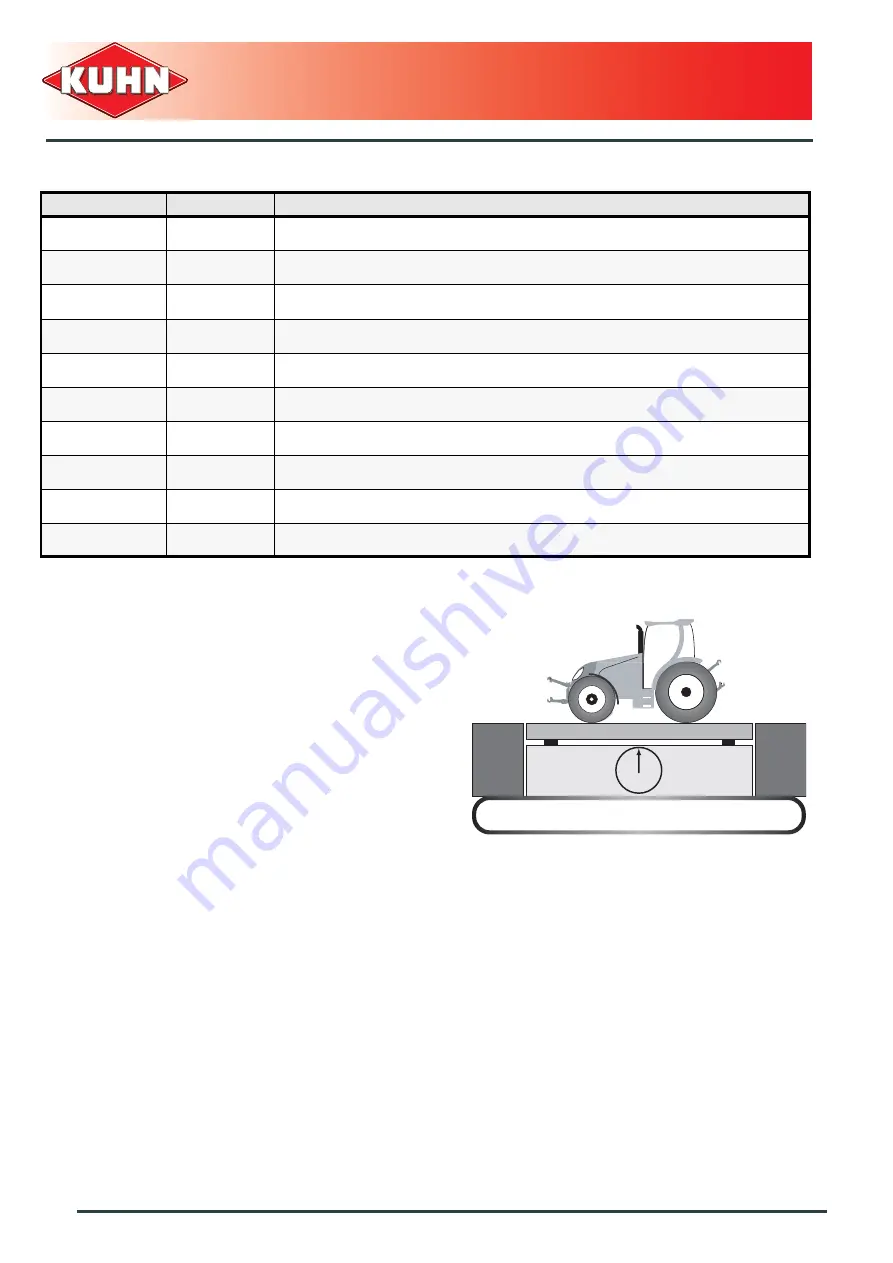
Disc mower
10
GMD33N
Safety
Description of symbols
Stage 1:
To measure:
- Tractor tare (T).
Description
Units
Description
T
kg
Tractor unladen weight
PTAC
kg
Gross Combined Weight Rating
T1
kg
Unladen load on tractor front axle
T2
kg
Empty load on tractor rear axle
t
kg
Axle loads (T machine)
t1
kg
Load on front axle (T machine)
t2
kg
Load on rear axle (T machine)
t1 max
kg
Maximum load authorized on the tractor front axle according to the tires
t2 max
kg
Maximum load authorized on the tractor rear axle according to the tires
M1
kg
Total weight of front tool or front ballast
T = _____kg
Содержание GMD33 N
Страница 2: ......
Страница 64: ...Disc mower 62 GMD33N Appendix T Axle loads Tractor only T _____kg ...
Страница 69: ......
Страница 70: ......
Страница 71: ......