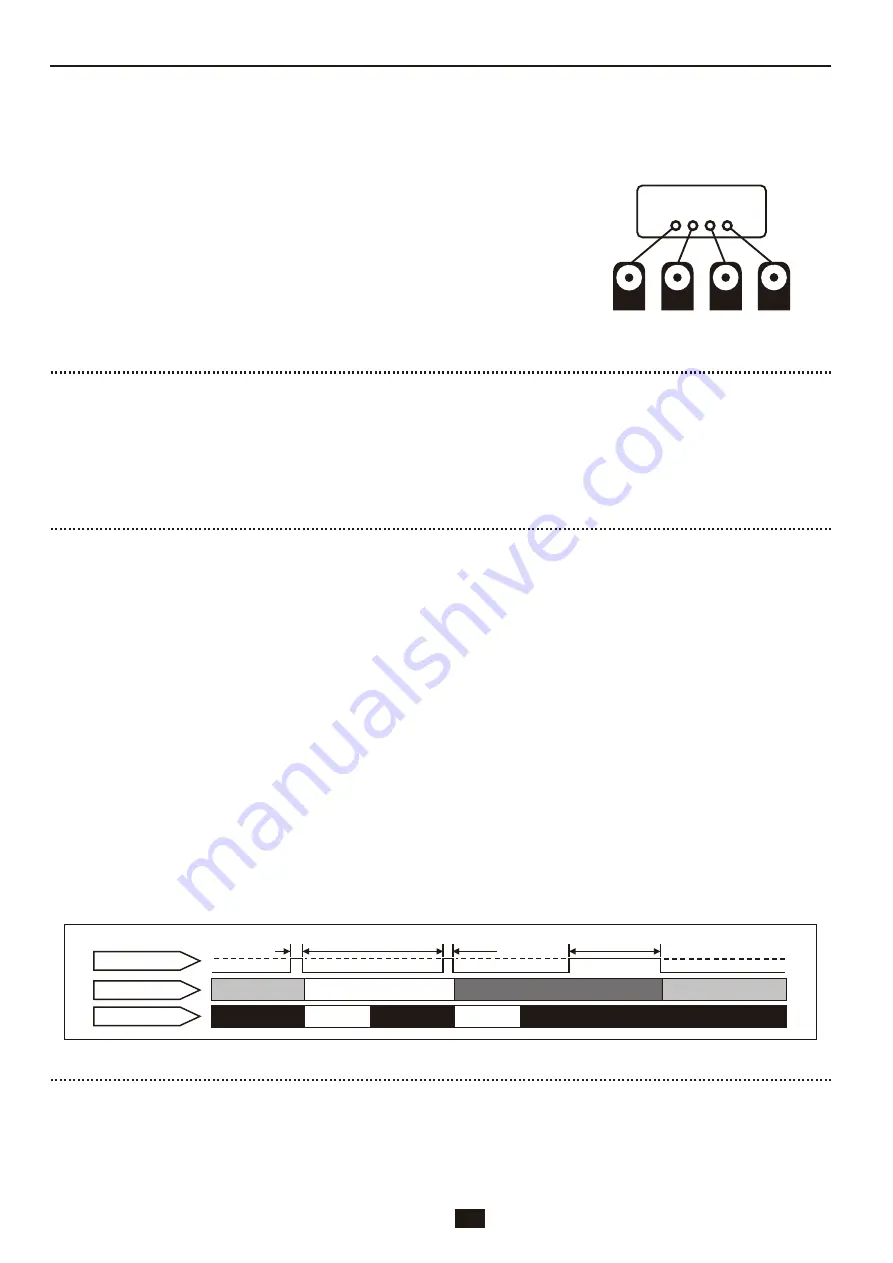
12
■Controlling Servos with a Control Board
Only one servo per output port may be connected when using a PWM
signal. Uncheck the Serial Signal check box.
■Control Using Programming
Please refer to When using a PWM signal in the ICS 3.5 Command
Reference to control the servos in PWM mode.
Example of how servos are
connected in PWM control
mode.
Control Board
Servos
1 2 3‥n
1 2 3 n
・
(Ch)
※Voltage drops and/or noise in the signal may cause unintentional movement during operation. Use this
product with caution.
※Using the position capture (teaching) function in conjunction with a home-made control board requires
pull-up resistor in the signal wire from the control board CPU. Furthermore, the CPU servo control board
needs to be able to change between signal input and output. Kondo control boards are compatible with the
position capture function.
Points of Caution When Using a PWM Signal
Using a PWM Signal
100〜200μsec
50μsec
700〜2300μsec
■ Diagram showing the timing of the signal and servo movement ■
■Position Command (MOVE)
The output shaft of the servo rotates in accor-
dance with the PWM input signal.
700μs (-135 ° ) to 1500μs (0 ° ) to 2300μs
(+135°)
■Power Limitation
Inputting a pulse width of 50μs will reduce the
power output of the servos. This state of limited
power output will be maintained until the servos
receive the next position command with a pulse
width between 700μs and 2300μs.
■Characteristic Change (Stretch preset change)
Inputting a pulse width of 100μs, 150μs or 200μ
s will instruct the servos to change between three
preset characteristics (SET1 ˜ SET3 stretch set-
tings) saved within the servo.
The servos will maintain the state the output shaft
was in directly before they were instructed to
change position.
Preset parameters (SET1, SET2 and SET3) can be
changed using the ICS menu. Setting 1 (SET1) will
automatically be selected when turning the servo
power on. 。
Stretch 1 (SET1) 100μs +/-10μs
Stretch 2 (SET2) 150μs +/-10μs
Stretch 3 (SET3) 200μs +/-10μs
■Position Capture (Teaching)
Inputting a pulse width of between 50μs and 200
μs will instruct the servos to output a pulse width
that indicates the current position of the servo
output shaft. This pulse output from the servos is
then read by the control board and the current posi-
tion of the servos can be ascertained.
Movement of Servos Using a PWM Signal
RCB-3HV
RCB-3J
PWM Compatible Control Boards
When operating this product using a PWM signal, position commands
can be made using general radio control signals.
Functionality can also be expanded by using other specific signals.
PWM cycle compatibility:3ms 〜 30ms
Pulse width: Normal operation 700μs to 2300μs.
Expanded function 50μs to 200μs.
※The KRS 3000 series is designed to be operated between 6.0 and 7.4 volts. Ensure the input current is within that range.
KCB-5 : 6 x PWM outputs. Teaching and characteristic change are possible depending on the programming.
(Cannot be used in conjunction with serial terminal, so separate wiring is required.)
: RCB-3HV/RCB-3J: 24 x PWM outputs. Up to 24 servos can be connected. Suitable for teaching
and changing characteristics.
Normal movement
Normal movement
Servo movement
input
signal
Hold
Input
Input
Input
Servo signal line
Output
Output
Input signal present
No input signal present
Power limitation