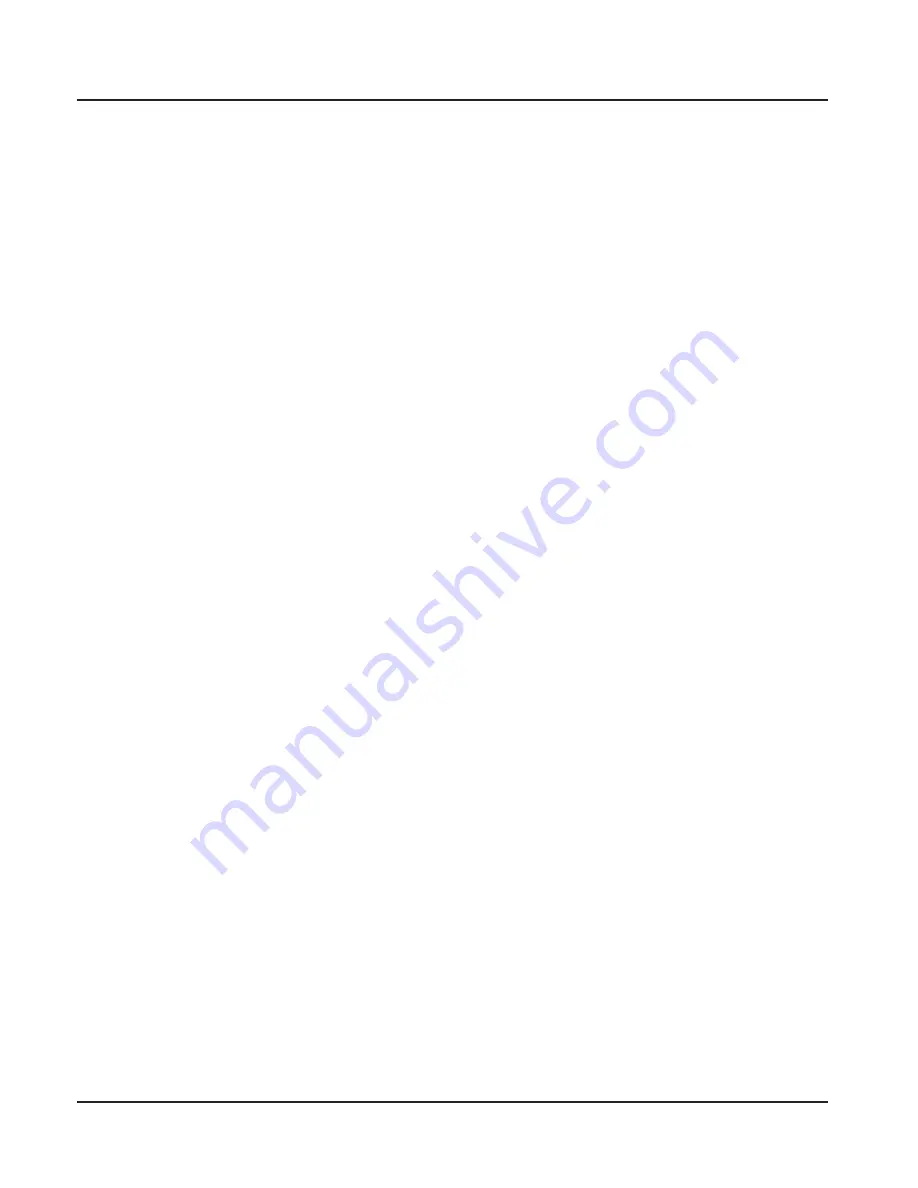
5.14
Section 5
Fuel System and Governor
2. The stepper motor, electronic control unit
(ECU) and oxygen sensor can all be checked
with the Kohler Emission Sentry
™
Tester (Kohler
Part No. 12 761 07-S).
a. Separate the plug connector between the
electronic control unit (ECU) and the stepper
motor. Plug the separated connectors into
the mating connectors on the Emission
Sentry
™
Tester. Connect the single black
lead to battery negative or a good ground
on the engine/unit. Turn the key switch on
the dash to the ‘‘run’’ position, and push
the small toggle switch on the tester to the
‘‘open’’ position. Observe the red LED’s
for the ECU and the bicolor LED’s for the
stepper motor. The red LED’s should fl ash in
sequence, the bicolor LED’s should alternate
colors, and you should hear the stepper
motor turning. Now push the toggle switch
to the ‘‘close’’ position and repeat your
observations. The red LED’s should fl ash
in the reverse sequence, the bicolor LED’s
should again alternate, and you should again
hear the stepper motor turning. If any or all
of the red LED’s are not fl ashing, the ECU is
faulty. If the bicolor LED’s are not alternating
and/or the stepper motor is not running, the
stepper motor is faulty.
b. Allow the toggle switch on the tester to return
to the ‘‘monitor’’ position, start the engine,
and place the throttle between midrange
and fast. Observe the LED’s on the tester.
The red and bicolor LED’s should fl ash as in
the previous test. The green LED (oxygen
sensor) will be off initially, unless the muffl er
is still hot from prior running. As the oxygen
sensor reaches operating temperature, the
green LED should begin to fl ash on and off.
If it stays on or off, or the interval between
fl ashes is more than 25-30 seconds, the
oxygen sensor could be faulty or the load
adjusting screw in the fuel metering valve
may be stuck or binding. Proceed to step 3.
3. Remove the stepper motor/fuel metering valve
assembly from the engine. Remove the four
small socket head screws and separate the fuel
metering valve from the stepper motor. Try to
turn the load adjusting screw with the blade of a
small screwdriver (see inset in Figure 5-17). If the
screw turns freely and easily, the oxygen sensor
was faulty (step 2b).
If the screw is stuck or binding, remove it from the
valve body, clean the threads with solvent, and
reinstall. Check it again for binding. Do not use
any type of lubricant on the threads of the load
adjusting screw.
NOTE: If the oxygen sensor is removed from
the exhaust manifold for any reason, a
high temperature anti-seize compound
(Loctite
®
No. 767) should be applied to
the threads. A new replacement sensor
already has a dry anti-seize compound
on the threads; additional compound is
not required.
4. If the fault circuit triggers while the engine is
idling, but not during normal operation, the
idle mixture screw on the regulator is probably
out of adjustment. Turn the screw 1/2 turn
clockwise, start the engine, and run it at idle for
approximately two minutes. If the fault circuit
does not trigger, the problem has been corrected.
If the fault circuit is triggered and the engine
shuts off before two minutes, turn the screw an
additional 1/4 turn clockwise and test again for
two minutes.
Governor
These engines are equipped with a centrifugal
fl yweight mechanical governor. It is designed to hold
the engine speed nearly constant under changing load
conditions. The governor gear/fl yweight mechanism
is mounted inside the crankcase and is driven off the
gear on the balance shaft.
Operation
As the governor gear rotates, centrifugal force causes
the fl yweights to move outward as speed increases.
As the fl yweights move outward, they cause the
regulating pin to move outward.
The regulating pin contacts the tab on the cross
shaft, causing the shaft to rotate when the engine
speed changes. One end of the cross shaft protrudes
through the side of the crankcase. Through external
linkage attached to the cross shaft, the rotating action
is transmitted to the throttle lever of the carburetor.
Содержание CV11-16
Страница 1: ...1 SERVICE MANUAL VERTICAL CRANKSHAFT CV11 16 CV460 465 CV490 495...
Страница 2: ......
Страница 4: ......
Страница 22: ...2 4 Section 2 Special Tools...
Страница 30: ...4 4 Section 4 Air Cleaner and Air Intake System...
Страница 56: ...6 6 Section 6 Lubrication System...
Страница 112: ...9 16 Section 9 Disassembly...
Страница 148: ...11 24 Section 11 Reassembly...
Страница 149: ......