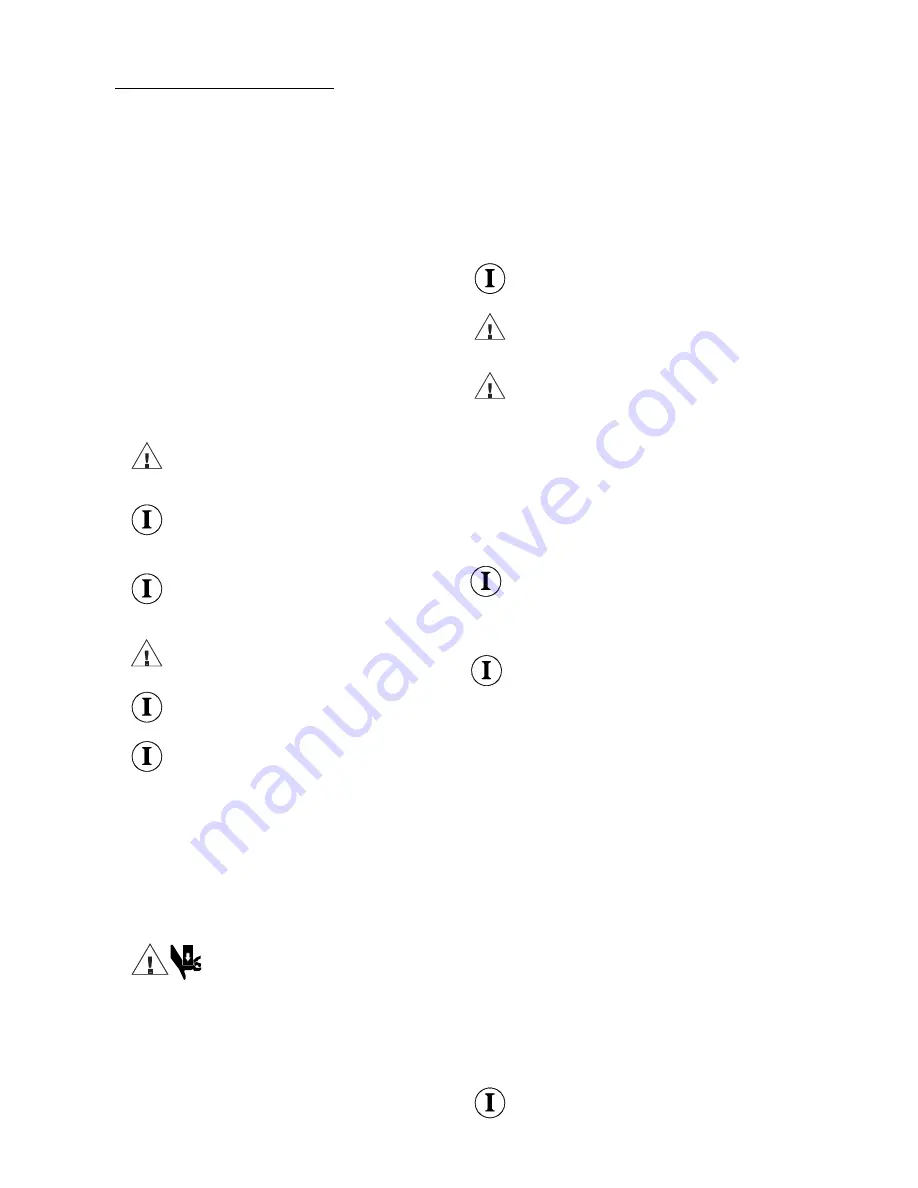
Instruction
Manual
UAP
2
page
9
______________________________________________________________________________________________________________________
5. Remarks in respect of the determined use
Before starting the pressing process the charging levels of the
battery cartridge (Pos.-#. 7) should be tested. A low charging level
can for example be detected by a continued signal of the light
diode display (Pos.-#. 6) for 20 sec. at the end of a test pressing
cycle. (see chapter 4.3)
5.1. Operation of the units
After having selected the right pressing jaw for the intended
application the jaw must be examined in terms of possible damage,
dirt in the compression area and ware. When using competitor
products the user has to make sure that the jaw complies with our
tool. To insert or change the pressing jaw please follow picture 6-
11.
After mounting the fitting on the tube the pressing jaws will be
opened by pushing the rear end of the pressing jaw together while
the jaw has to be positioned on the fitting. (Pls. see also picture 5
Pos. E)
A pressing procedure will be initiated by actuating the trigger
(Pos.-#. 1, Picture 2 Pos. C). The pressing process is defined by the
closing motion of the pressing jaws. The drive rolls on top of the
ram close the pressing jaws scissors like.
Attention
The user has to make sure that the lock pin (Pos. 3) is
properly engaged
Attention
A necessary condition for a permanently leaking free
connection is that the pressing cycle has to be completed
which means that the pressing jaws completely closed at
the tip as well as the T-link.
Attention
The assembly of gas pipes in gas distribution lines is
prohibited unless the system provider gives an explicit
permission to use this tool on special gas fittings.
Attention
The pressing procedure can be interrupted at any
moment by releasing the trigger.
Attention
The user has to check by optical means whether the
pressing jaws are completely closed.
Attention
If a pressing cycle has been interrupted the fitting has to
be either dismantled or pressed a second time.
The user needs to make sure that the pressing jaws are completely
closed and that there are no foreign objects (e.g. plaster or stone
fractions) between the pressing jaws.
In case of error or emergency push retract button (Pos. 2, Picture 2
Pos. B) to return the drive rolls into starting position.
The drive rolls retract automatically and return into the starting
position after the maximum operating pressure has been reached
enabling the user open the pressing jaw.
Attention
Before changing the pressing jaws remove
battery to avoid unintentional operation.
5.2. Explanation of the application range
The UAP 2 is a hand guided pressing tool to mount fittings on multi
Layer, copper and stainless steel type plumbing tubes with
∅
12 to 54
mm, with pressing chain (picture 12c+d) up to 75 mm. The unit is not
supposed to be restrained in a vise. It is not allowed to use the tool in a
stationary application. Complying certain conditions the unit can be
operated stationary with our presentation support EKST. The conditions
can be taken from the instruction manual of the EKST.
The tool is not designed for continued pressing operations. After a
sequence of approximately 50 completed cycles you have to make a
break of 15 minutes to give the unit time to cool down.
Attention
Too intensive use can cause heat damages for the tool
Attention
During the operation of electric motors sparks can occur
which might ignite highly inflammable or explosive liquids
and materials
Attention
Electric-hydraulic pressing tools must not be operated in
pouring rain or under water.
5.3. Mounting instructions
Please reference the assembly manual of the systems supplier before
mounting the fittings on the tubes. In order to safeguard a proper
pressing and to guaranty a safe and reliable handling the machine must
only be operated with pressing jaws/~ chains recommended by the
provider of the tube system and/or the tool manufacturer. If the markings
on the tool and pressing jaw do not match respectively if there are no
assembly instructions the user has to contact the provider of the system
to request a compatibility statement.
Attention
Do not use bent or damaged pressing jaws.
For your job on the location we recommend the accessories shown in
picture 12.
Remark
As the tool manufacturer we offer perfectly designed pressing
jaws for all known systems and tube dimensions. Special
designs and customer solutions upon request.
5.4. Service and maintenance instruction
The reliable performance of the tool is dependent on careful treatment
and service. This represents an important condition to safeguard a lasting
connection. To safeguard this the tool have to be maintained and
serviced regularly (see chapter 4.3 for more information).
We would like to draw your attention to the following points:
1.
The electric-hydraulic pressing unit have to be cleaned and dried
after each use before being put into the transportation case.
2. In order to guaranty a proper function of the machine the pressing
tool should be returned to the manufacturer after the light diode
display (Pos.-#. 6) indicates Service.
3. The battery as well as the charging unit must be protected against
humidity and foreign objects.
4. The bolt joins, the drive rolls and their guides must be oiled
regularly in small amounts.
5. Check through test crimps or have the tool manufacturer check the
tool and pressing jaws regularly for proper function.
6. Keep pressing jaws clean. Remove dirt with a brush.
In order to avoid possible malfunctions we offer you a manufacturer
service consisting of disassembly, cleaning, exchange of possibly worn
out parts assembly and final control. Only a clean and properly
functioning press system can over the time safeguard a leaking free
connection.
Within the determined use of the tool only the pressing jaws (Pos.-#. 10)
are permitted to be changed by the customers.
Attention
Do not damage the seals of the tool.
If the seals are damaged the warranty is invalidated.