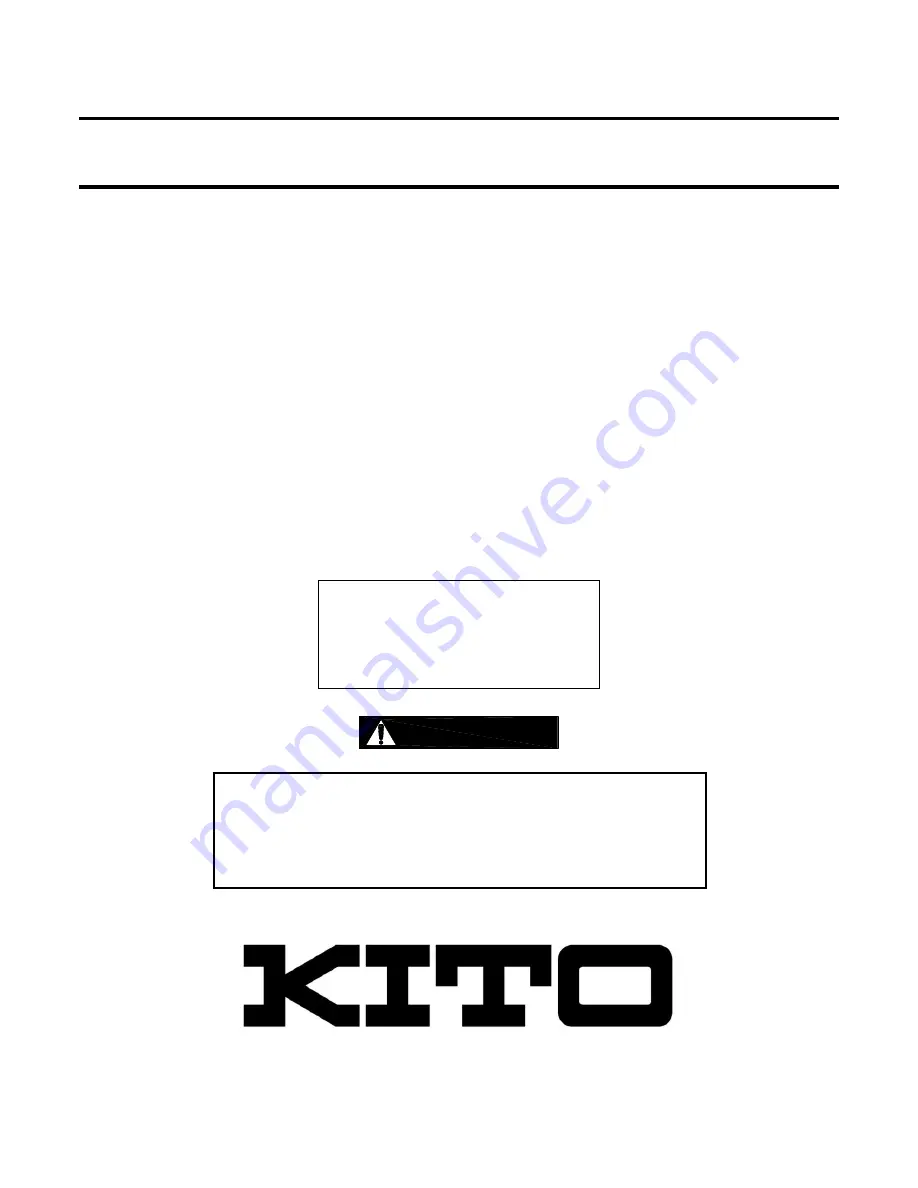
Owner’s Manual
LUBRICANT FREE
AIR POWERED
CHAIN HOIST
TCL SERIES
¼, tonne through 1 tonne Capacity
WARNING
Code, Lot and Serial Number
This equipment should not be installed, operated or
maintained by any person who has not read and understood
all the contents of this manual. Failure to read and comply
with the contents of this manual can result in serious bodily
injury or death, and/or property damage.
EFFECTIVE: April 1, 2020
Содержание TCL Series
Страница 43: ...43 Figure 7 4 Single Fall Chain Connections Figure 7 5 Double Fall Chain Connections ...
Страница 52: ...10 1 Motor Valve Body and Controls 52 Figure 10 1 Motor Valve Body and Controls ...
Страница 55: ...55 This Page Intentionally Left Blank ...
Страница 56: ...10 2 Brake Gears and Load Suspension Components 56 Figure 10 2 Brake Gears and Load Suspension Components ...
Страница 61: ...61 NOTES ...
Страница 62: ...62 NOTES ...
Страница 63: ...63 NOTES ...