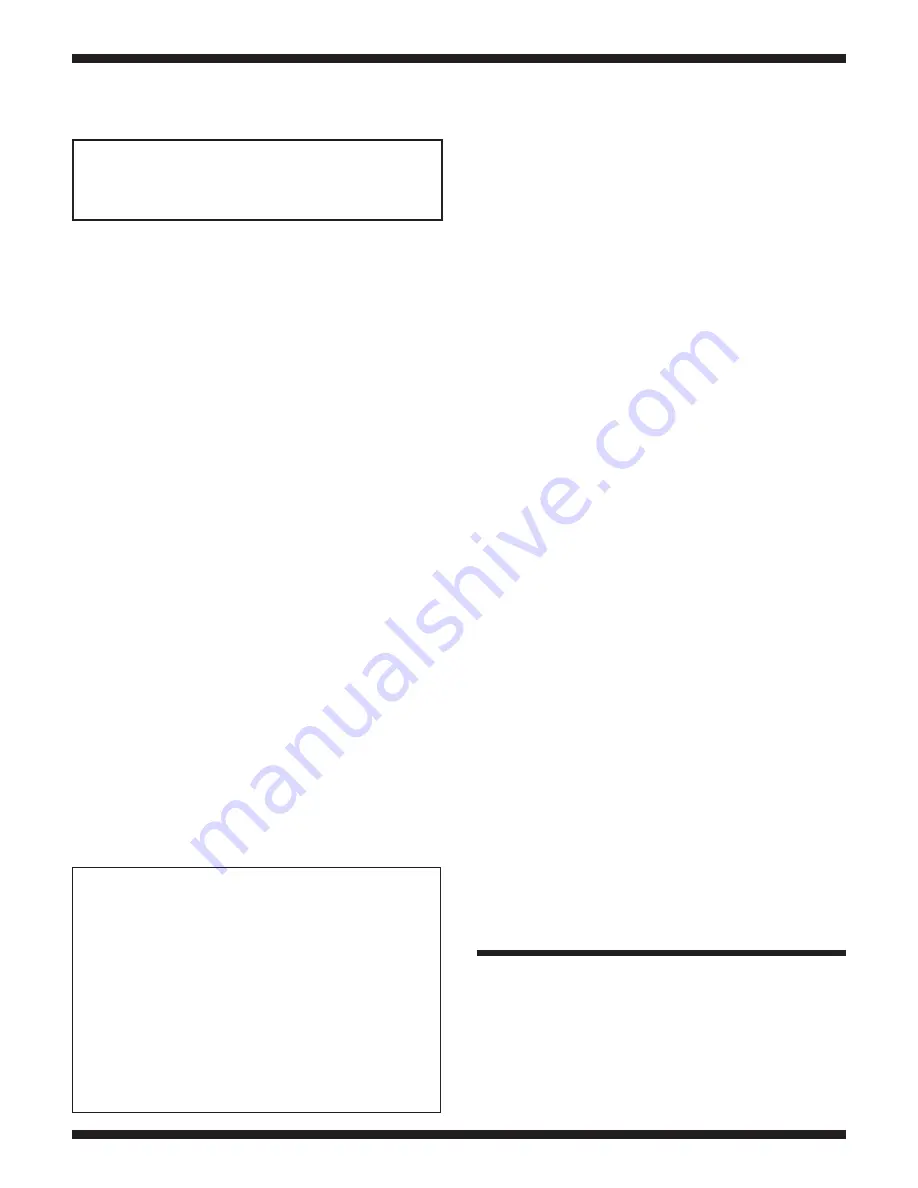
PAGE 12
TECH SHEET - DO NOT DISCARD
PART NO. 3954702 REV. A
FOR SERVICE TECHNICIAN'S USE ONLY
IMPORTANT: Electrostatic (static electricity)
discharge may cause damage to electronic
control assemblies. See page 1 for details.
CONTROL BOARD REMOVAL
OR REPLACEMENT
PART NO. 3954702 REV. A
NOTE: This sheet contains important
Technical Service Data
FOR SERVICE TECHNICIAN ONLY
DO NOT REMOVE OR DESTROY
4,254,640
4,254,641
4,262,870
4,268,098
4,288,671
4,291,556
4,306,841
4,324,035
4,357,813
4,366,902
4,387,580
4,430,871
4,432,528
4,491,210
4,495,960
4,533,126
4,545,947
4,555,919
4,566,295
4,572,596
4,618,193
4,624,117
4,643,350
4,646,545
4,656,844
4,656,847
4,692,987
4,700,554
4,715,401
4,715,402
4,719,769
4,754,622
4,809,524
4,493,745
SOFTWARE COPYRIGHTED
MANUFACTURED UNDER ONE OR MORE OF
THE FOLLOWING UNITED STATES PATENTS:
NOTE:
Be sure to perform the Diagnostic Tests before
replacing the control board. Disconnect power before
replacing control board.
To remove machine control board:
■
Remove all connectors from the control board. Remove
both mounting screws from control board.
■
Push the mounting legs on both sides of control board
toward each other. Lift control board away from bracket.
■
Pinch and remove cable tie snap from bottom of board.
To replace machine control board:
■
Attach control board mounting legs to bracket. Replace
both mounting screws into control board and secure to
control bracket.
■
Plug all connectors into the control board. Reconnect
ribbon connectors so that the ribbon is wrapped around
the two-wire (GY/WH and BK/WH) leads.
■
Plug wire harness snap tie into top of board.
To remove motor control board:
■
Remove all connectors from the control board.
■
Remove lock down screw from plastic bracket
(mounting screw #1, see Figure 6). This is the screw on
the motor control that is closest to the machine control.
Also remove screw near heat sink (mounting screw #2,
see Figure 6) from motor control board.
■
Rotate entire assembly away from control mounting
bracket, lift and remove motor control board.
To replace motor control board:
■
Insert plastic tabs into slots on metal control bracket.
Rotate entire assembly toward the control mounting
bracket so that the screw hole in the plastic mount lines
up with the hole in the metal control bracket.
■
Insert both mounting screws and secure into metal
control bracket.
■
Plug all connectors into the control board.
To remove line filter:
■
Disconnect the two filter connectors from the wiring
harness and power cord.
■
Remove the grounding screw which secures the
grounding ring to the top.
■
Remove the line filter mounting screw. Tilt away from
screw mounting end and remove line filter component.
To replace line filter:
■
Insert line filter tab into slot on top, secure line filter with
mounting screw.
■
Secure grounding ring with grounding screw to the top.
■
Reconnect the two filter connectors to the wire harness
and power cord.