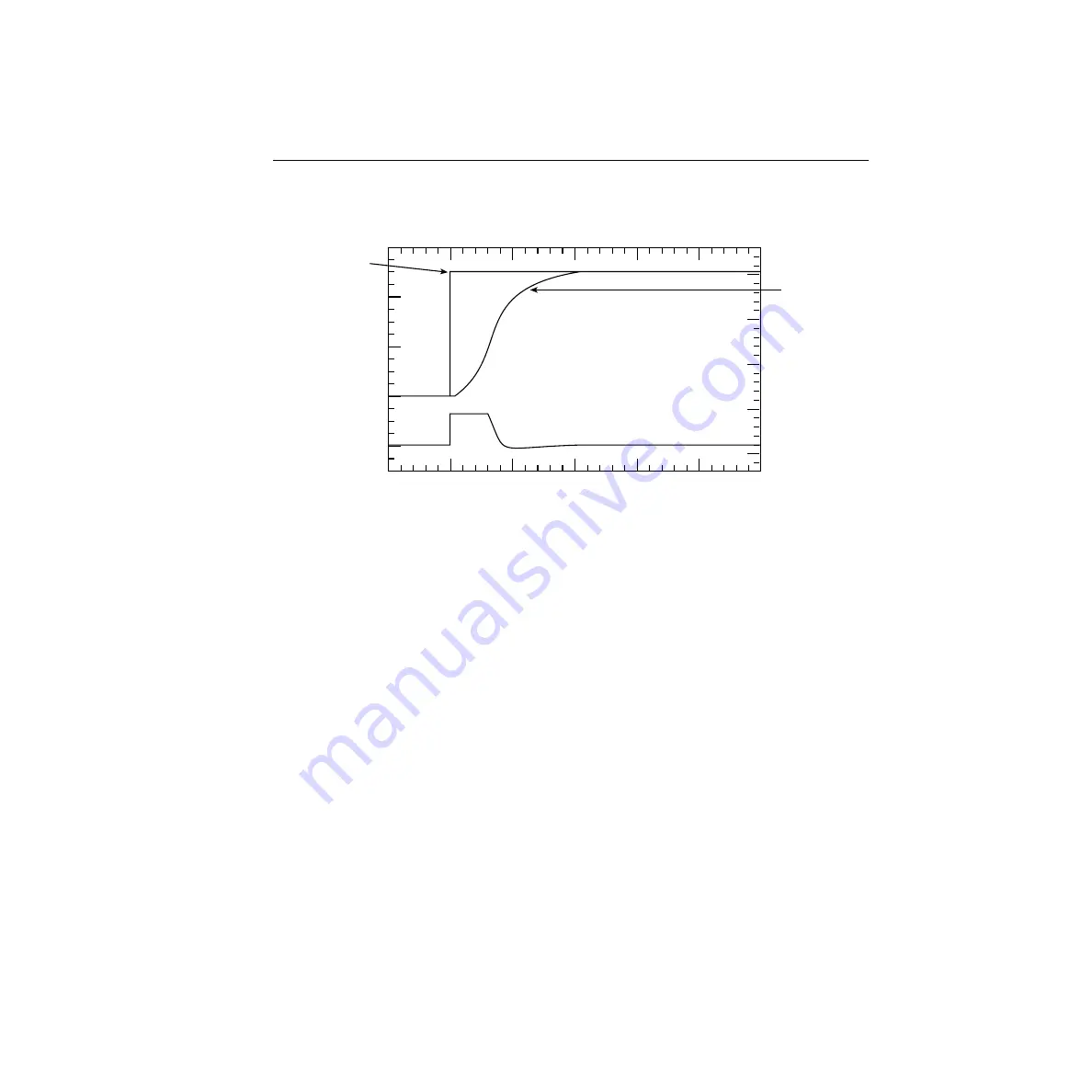
Models 2510 and 2510-AT User’s Manual
PID Control Concepts
4-5
Figure 4-3
PID control characteristics
PID tuning
It will be necessary for you to tune the Model 2510 PID loop controller by trial and error.
The method for tuning the PID loop outlined below is intended only as a starting point,
and some experimentation may be required for optimum performance. This procedure is
based on the assumption that a critically damped system is optimal, and that stability and
noise performance must be traded for response time. See
, for information on setting up functions including programming the proportional,
integral, and derivative constants covered in these procedures.
CAUTION
This procedure may result in large temperature oscillations during the
tuning process that could cause damage to the thermoelectric cooler.
1.
Adjust the temperature setpoint value (T
S
) to a typical value for thermoelectric
cooler, and set the Derivative (D) and Integral (I) constants to 0.
2.
Select a safe value for the maximum TEC power, and increase the proportional
gain (P) until the system is just oscillating. Note the period of oscillation, then
reduce the gain by 30%. Note, however, that if you adjust for maximum power
(control effort limit) and tune for that setting, specific PID parameters will result. If
you use those same PID values for a different limit, the system may respond
differently.
3.
Suddenly decreasing or increasing T
S
by about 5% should induce underdamped
oscillations. Try several Derivative values, and choose a value that gives a critically
damped response. Typically, D will be about one third of the oscillation period
obtained in step 2 above.
80
70
60
50
40
50
100
150
Time (s)
Temperature (
°
C)
Cooler
Temperature
Setpoint
200
300
0
250
50
0
Power (W)
Содержание TEC SourceMeter 2510
Страница 194: ...A Specifications...
Страница 197: ...B StatusandErrorMessages...
Страница 206: ...C IEEE 488BusOverview...
Страница 221: ...D IEEE 488andSCPI ConformanceInformation...
Страница 225: ...E ExamplePrograms...
Страница 233: ...F GPIB488 1Protocol...