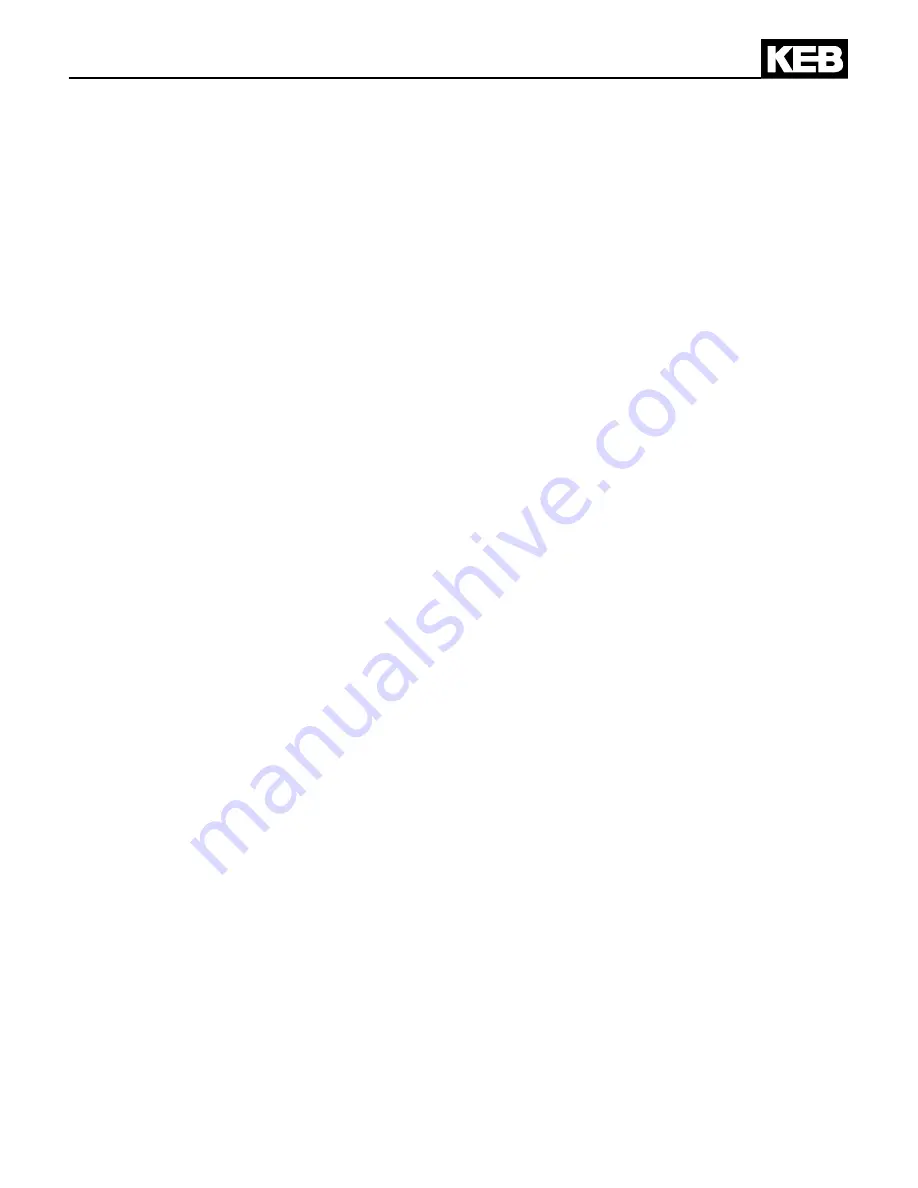
GB - 7
COMBICONTROL
2.
Basic module with drive interfaces
The basic module is mounted on a 35 mm mounting rail. The grounding occurs by the mounting
rail via spring contacts on the back of the basic module. The basic module serves as carrier
for the operation unit and the field bus interface as well as the input/output terminal blocks.
Furthermore it contains the
• CPU
• Switching power supply
• Flash file system
• Real-time clock
• HSP5/485-interfaces to the inverter/servo axes
2.1 Real-time clock
The integrated real-time clock is maintenance-free (no battery) and operates without power
supply for approx.30 days. After this time it must be adjusted again. A read out parameter
indicates the validity of the date and time. The control shall remain switched on min. 30 minutes
for complete loading. Leap years are recognized automatically up to the year 2099. Date and
time can be read and set via COMBIVIS or the control program.
2.2 HSP5/485 interfaces to the inverter/servo axes
Up to eight KEB COMBIVERT F5 can be connected via the terminals X1A to X1H. The
connection occurs via reliability RS485 cables, which can be up to 100 m long. A shielded
standard cable with RJ-45 connector is used on the control side and appropriate operator
on the frequency inverter/servo. The process data of the required axes are exchanged by
the control in the cyclic or synchronous mode. Service 50 (1*32 + 2*16 Bit process data) is
used thereby. The parameter channel is free for the PLC program and COMBIVIS access
to the axes. Depending on the used axes the cycle time can be between 1 and 65 ms. The
process data assignment in the axes must be adjusted before starting the cyclic/synchronous
operation in parameters SY.16…31 (if not stored in the axes).
The process data are mapped-in as follows in the image of the control:
%IW8+9
%ID4
1. Word (32 Bit) of axis 1
%QD4
1. Word (32 Bit) to axis 1
%IW10
2. Word (16 Bit) of axis 1
%QW10 2. Word (16 Bit) to axis 1
%IW11
3. Word (16 Bit) of axis 1
%QW11 3. Word (16 Bit) to axis 1
%IW16+17 %ID8
1. Word (32 Bit) of axis 2
%QD8
1. Word (32 Bit) to axis 2
%IW18
2. Word (16 Bit) of axis 2
%QW18 2. Word (16 Bit) to axis 2
%IW19
3. Word (16 Bit) of axis 2
%QW19 3. Word (16 Bit) to axis 2
%IW24+25 %ID12 1. Word (32 Bit) of axis 3
%QD12 1. Word (32 Bit) to axis3
%IW26
2. Word (16 Bit) of axis 3
%QW26 2. Word (16 Bit) to axis3
%IW27
3. Word (16 Bit) of axis 3
%QW27 3. Word (16 Bit) to axis3
%IW32+33 %ID16 1. Word (32 Bit) of axis 4
%QD16 1. Word (32 Bit) to axis 4
%IW34
2. Word (16 Bit) of axis 4
%QW34 2. Word (16 Bit) to axis 4
%IW35
3. Word (16 Bit) of axis 4
%QW35 3. Word (16 Bit) to axis 4
further on next side
Содержание combicontrol PCC C5
Страница 1: ...07 2007 COMBICONTROL 00 C5 0DB K213 Instruction Manual PCC C5...
Страница 31: ...GB 31 COMBICONTROL...