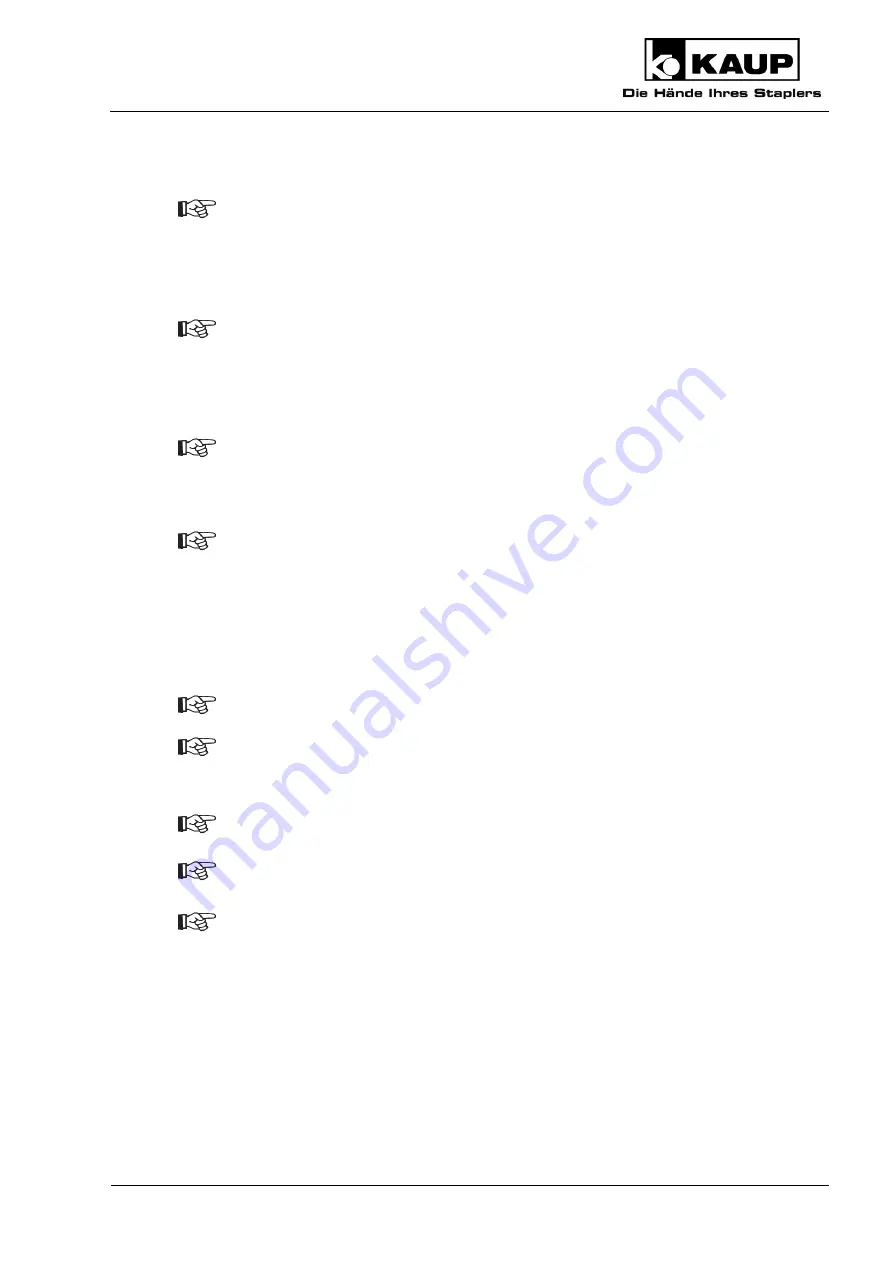
Operating Manual
Original Operating Manual
17
Replace worn sliders (11) by removing nut (25) from each cylinder (26). Pull the
carriage (27) to the side to remove. Remove the greasing nipples (12) and the screw
(28). Replace the sliders (11). When installing the new sliders, make sure that the
axial stops (29) are correctly seated. Refit the screw (28) and the greasing nipple
(12). Push the carriage (27) into clamp body (30) and reinstall nuts (25) of cylinders
(26).
Replace defective supporting rollers (22) in the hooks (10) by removing the screws
(9). Using suitable hoisting gear tilt the clamp body (30) forwards away from the fork
carriage on the lift truck. Remove the bolts (31) in the hooks (10), remove the
defective supporting rollers (22) and replace them with new ones. Remount the clamp
body (30) in the reverse order.
Replace the faulty cylinder (23) by removing the hydraulic lines from the cylinder (23)
with the hydraulic system depressurised. Remove the nut (31), loosen the lock nut
(32), and remove the nut (24). Replace the faulty cylinder (23) and install the lock nut
(32), nut (24), and nut (31). Tighten the lock nut (32) and re-install the hydraulic lines.
After installing or removing a cylinder (26), always check the clearance between the
cylinder mount and nut of the cylinder (26). Cylinders are installed with axial
clearance of 1.5 to 2 mm.
6.3.3 Forks
Annually
Inspect the heel of the fork for wear and cracks.
Remove forks from service when wear exceeds 10 % of the thickness of the fork.
As necessary
Bent forks are not safe to operate and their continued use should be prevented.
Straightening of forks may only be performed by the manufacturer of the fork or by
one of his authorised workshops.
You can increase the service life of forks by using forks especially protected
against wear.