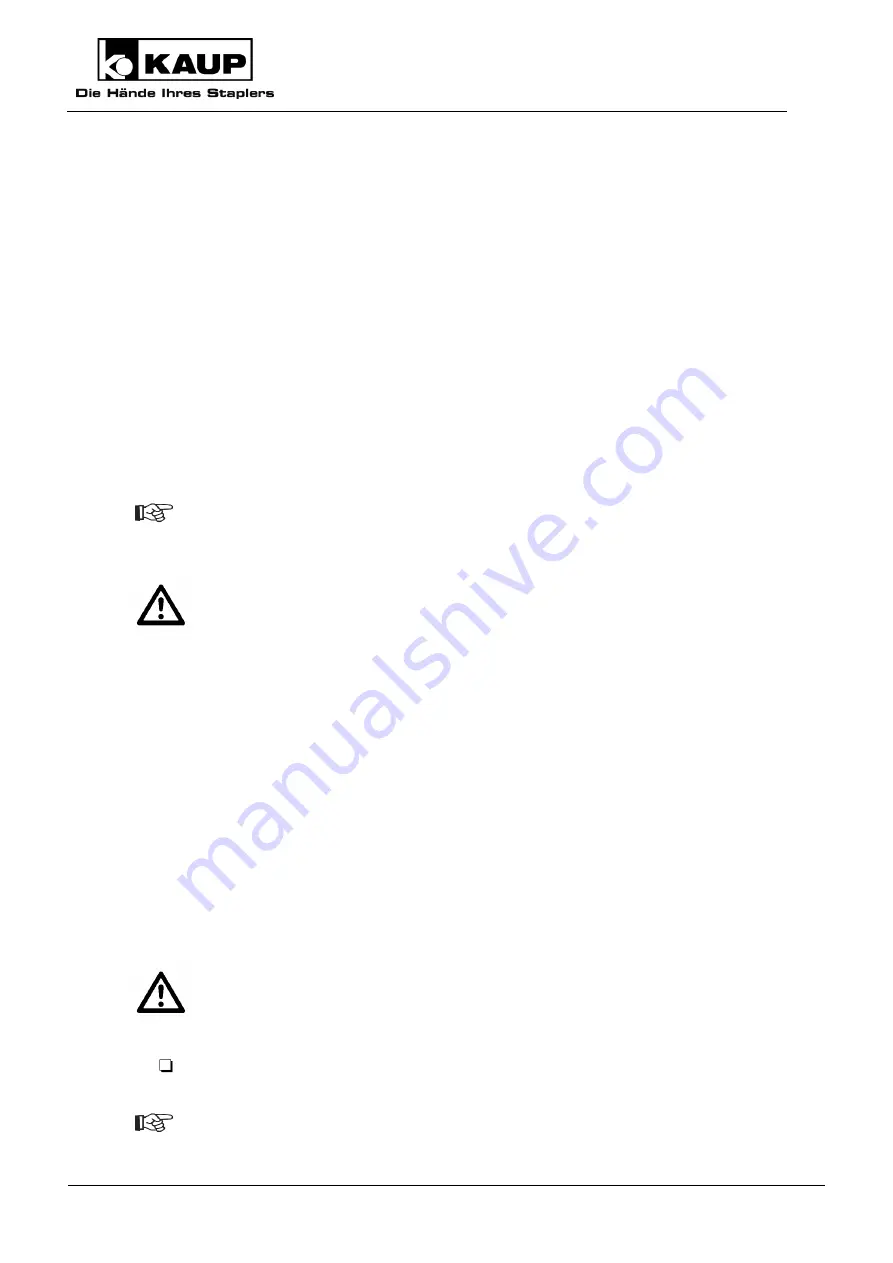
Operating Manual
10
Original Operating Manual
Mount the lower hooks (2), tightening the screws (5) with a torque of 190 Nm.
Connect the hose lines (6) to the hydraulic connectors on the lift truck.
Remove the fork stops (7) and slide the fork arms onto the fork carrier from the side.
Make sure that all fork stops (7) have been correctly reinstalled.
Before initial operation, check the functions and the identification of the attachment with the
movement directions of the operating elements (operating lever, joystick, etc.).
Mount the residual carrying capacity notice and identification of the operating elements (if
not already present) of the combination of lift truck/attached equipment on the lift truck.
4.2
Checking out
KAUP-attachments are delivered pre-lubricated. If the attachment has been in storage
for a longer period, we recommend that it be lubricated again before being placed in
service. See 6. Maintenance and onwards.
Failure of the safety devices (e.g. the pressure relief valve and the non-return
valve) and incorrect connection of the controls to the actuators can cause
malfunctioning of the attachment and damage to it.
After mounting and before initial operation, check the functions and the
identification of the attached equipment with the movement directions of the
operating elements (operating lever, joystick, etc.).
4.2.1 Bleeding the hydraulic system
Start the lift truck.
Move the sideshifter repeatedly in both directions to maximum extent.
Repeatedly cycle the fork positioner from the fully open to the fully closed position.
Inspect the hydraulic connections for leakage.
4.2.2 Adjustment after putting into service
The hydraulic system is under pressure. During work on hydraulic components
oil spurting out can cause injuries. Unload the system in accordance with the
operating instructions of the lift truck manufacturer. In the case of injuries
caused by high pressure oil, inform the works physician and seek out a
specialist immediately.specialist immediately.
Synchronising the carriages
The synchronization of slides is adjusted ex-factory. This can alter for different friction
conditions (wear), temperatures and volumes conveyed. Perform a readjustment. The
recommended working temperature of the hydraulic fluid is approx. 35 °C.