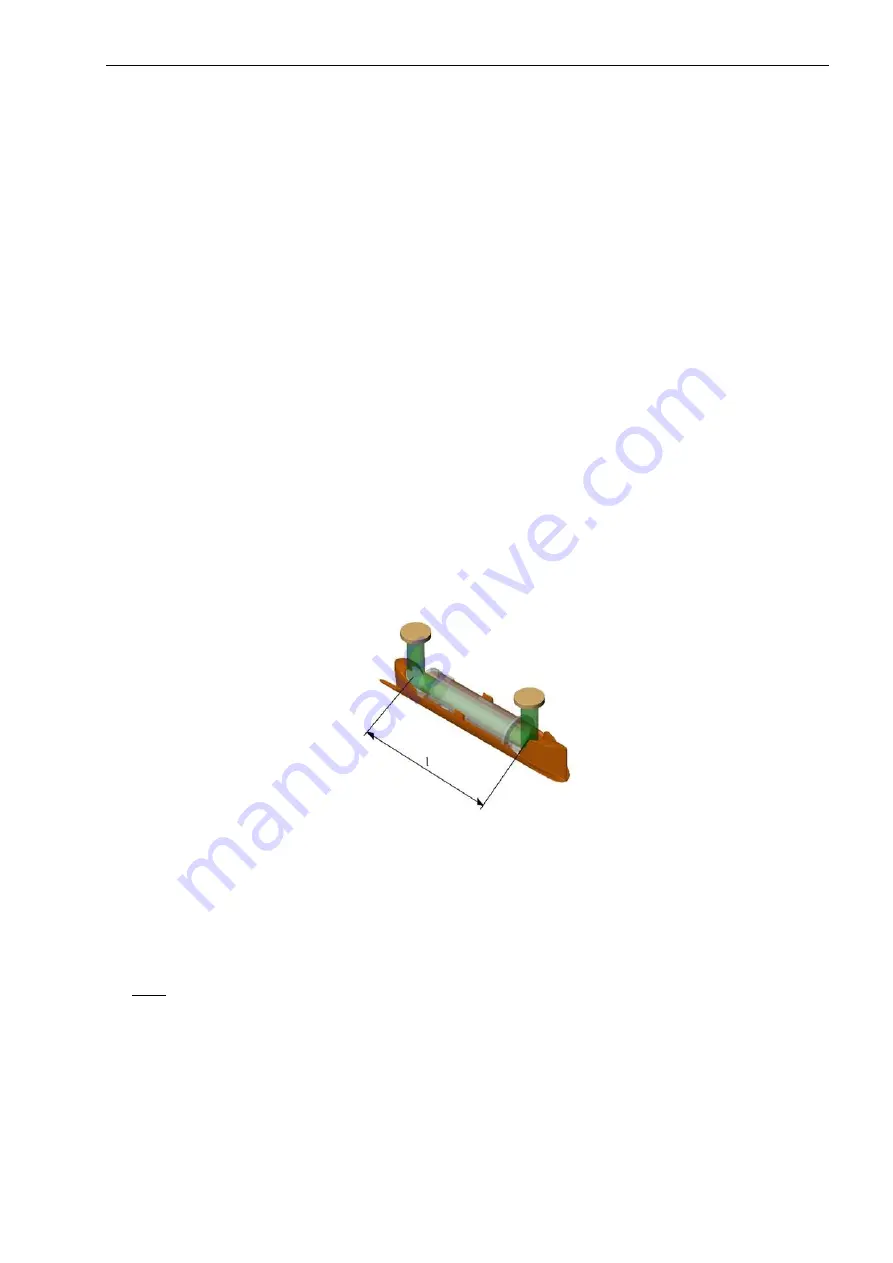
TECHNICAL DESCRIPTION
ULTRAFLOW® 54 DN150-300
Kamstrup A/S
·
Technical description
·
5512-876_M1_GB_12.2020
33
8
Functional description
Within the heat, cooling and water meter industry, producers have been working on alternative techniques for the
replacement of flow sensors based on the mechanical principle. Research and development at Kamstrup have proven
that ultrasonic measuring is the most viable solution. Combined with microprocessor technology and piezo ceramics,
ultrasonic measuring is not only accurate but also reliable.
8.1
Flow measurement with ultrasound
Within ultrasonic flow measuring, there are two main principles: the transit time method and the Doppler method. The
Doppler method is based on the frequency change which occurs when sound is reflected by a moving particle. This is the
effect you experience when a car drives by. The sound (the frequency) decreases when the car passes by. The transit time
method used in ULTRAFLOW® utilizes the fact that it takes an ultrasonic signal, sent in the opposite direction of the flow,
longer to travel from transmitter to receiver than a signal sent in the same direction as the flow.
A piezo-ceramic element is used for transmitting and receiving ultrasound. The thickness of the element changes when
exposed to an electric field (voltage) and thereby it functions as a transmitter of ultrasound. When the element is
mechanically influenced, it generates a corresponding electric voltage and thus functions as a receiver of ultrasound.
8.2
Signal path, flow calculation and flow profiles
As proven by the calculations below, the average flow velocity is directly proportional to the transit time difference of
ultrasound signals which are sent with or against the flow.
shows as example the essential elements of the
signal path in ULTRAFLOW® 54 (type 65-5-XXHX-XXX, q
p
0.6…2.5 m
3
/h): Piezo-electric elements transmit and receive the
ultrasound signal, which is reflected into and through the measuring tube to the receiver via reflectors. Due to
superposition of velocities of water and sound signal, ultrasound propagates faster with the flow than against the flow.
Figure 28. Signal path in ULTRAFLOW® 54 (type 65-5-XXHX-XXX, q
p
0.6…2.5 m
3
/h). Sound signals are transmitted by the
transducers via 2 reflectors. The signal's transit times with and against the flow vary for the significant sound path
distance (parallel with the measuring tube). In this case, the flow is flowing from right to left.
For the calculation of the transit time difference, the signal path along the flow is crucial, and the transit time to the
measuring distance is calculated as:
𝑡 =
𝑙
𝑐 ± 𝑣
where:
𝑡
is the transit time from sender to receiver of the sound signal along the measuring distance
𝑙
.
[s]
𝑙
is the measuring distance.
[m]
𝑐
is the sound propagation velocity in stagnant water.
[m/s]
𝑣
is the average flow velocity of water.
[m/s]