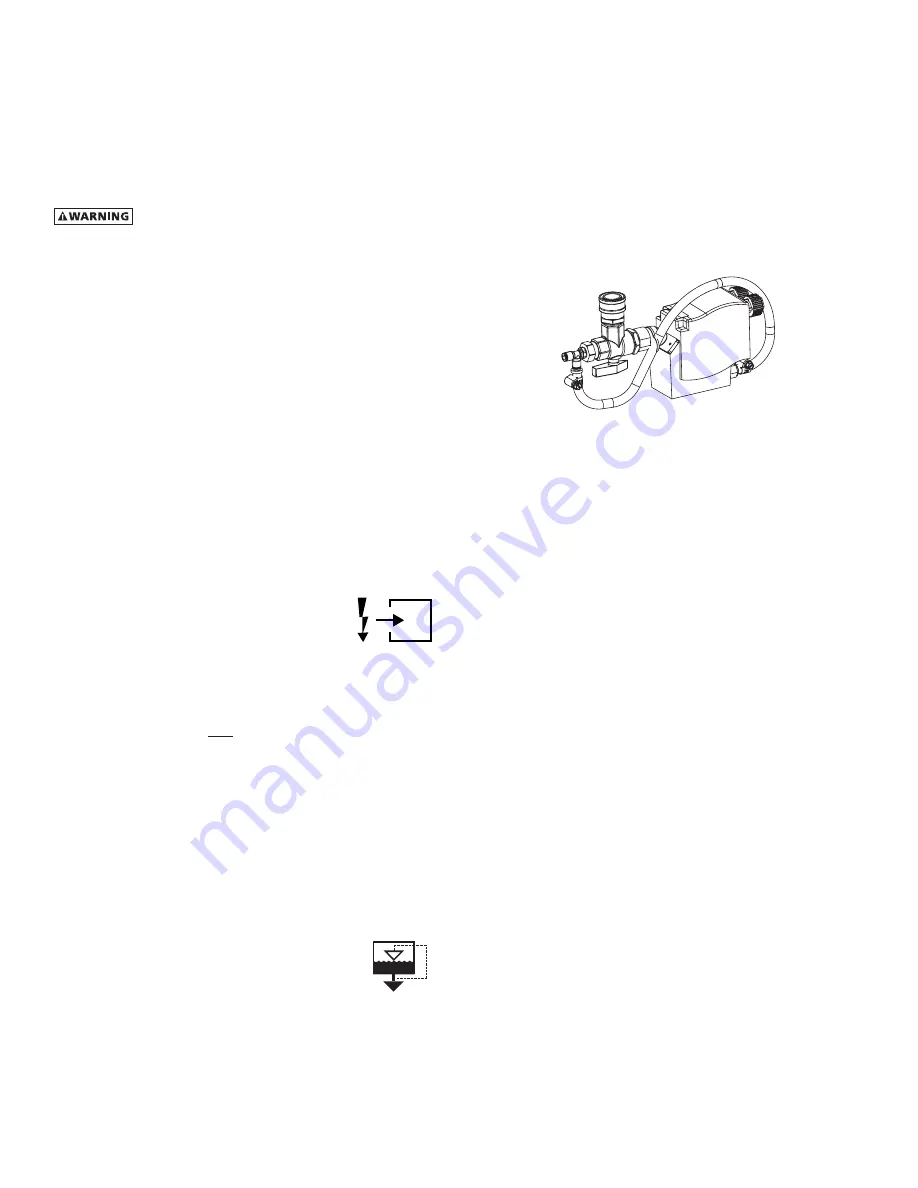
4
1.2 Mounting
Mount on floor or shelf free from vibration.
1.3 Piping connections
A. Air Inlet - Connect compressed air line from air source
to air inlet. (Reference markings on dryer or see callout
drawing on page 14 for air inlet/outlet connection
locations.)
Refer to Serial Number Tag for maximum
working pressure. Do not exceed dryer’s Maximum Working
Pressure.
NOTE: Install dryer in air system at highest pressure possible
(e.g. before pressure reducing valves).
NOTE: Install dryer at coolest compressed air temperature
possible. Maximum inlet compressed air temperature: 120°F
(49°C). If inlet air exceeds this temperature, precool the air
with an aftercooler.
B. Air Outlet – Connect air outlet to downstream air lines.
C. Bypass piping – If servicing the dryer without interrupting
the air supply is desired, piping should include inlet and
outlet valves and an air bypass valve.
D. Water cooled models – cooling water inlet and outlet
1. Connect cooling water supply to cooling water inlet.
2. Connect cooling water return line to cooling water
outlet connection.
NOTE: Strainer and water regulating valve are supplied on
water cooled models.
1.4 Electrical connections
IMPORTANT: Use copper supply wires only.
A. Dryer is designed to operate on the
voltage, phase, and frequency listed on
the serial number tag.
B. Connect power source to terminal strip in electrical
enclosure.
NOTE: Refrigeration condensing unit is designed to run
continuously and should NOT be wired to cycle on/off with
the air compressor.
NOTE: CHECK FOR CORRECT PHASING OF UNIT. After starting
the dryer, if an unusual noise is heard, or if the discharge
line does not get hot, the refrigeration compressor may be
running in the reverse direction. Immediately stop the dryer,
reverse two of the power leads, restart the dryer, and verify
the unusual noise is corrected and the refrigerant discharge
line is hot. FAILURE TO DO SO MAY DAMAGE THE COMPRESSOR
AND VOID THE WARRANTY.
1.5 Moisture separator
A. An automatic electric demand drain (EDD)
discharges condensate removed by the
separator. It may be desirable to pipe
the condensate from the EDD outlet to a
suitable drain.
B. For manual draining, convenient dryer depressurization,
and EDD service, a three-way valve assembly has been
installed at the bottom of the moisture separator (and
cold coalescing filter where applicable). Review the
following for proper drain function:
• Automatic Draining - Valve handle should be
positioned parallel to the valve body (as shown), with
the arrow on the handle pointing toward the EDD. In
this position, condensate will flow from the bowl to
the EDD.
• Drain Isolation (Shutdown) - Valve handle shall be
turned perpendicular to the valve body (rotate 90°). In
this position, condensate flow is shutoff.
• Manual Draining - Drain valve handle shall be rotated
slightly past the drain isolation position to allow
throttling through the valve for manual discharge and
depressurization.
• NOTE: The quick disconnect fitting allows removal of
the entire drain assembly.
However, the unit must
be depressurized prior to disassembly or serious
injury may occur.
NOTE: Discharge is at system pressure. Drain line should be
anchored.
NOTE: Condensate may contain oil. Comply with applicable
laws concerning proper disposal.
1.6 Operation
A. Verify that isolation valves are open. If the drain fails to
discharge after the valve is energized, the electronic
control circuit will repeatedly energize the valve in an
attempt to clear the discharge port. If, after 60 seconds,
the drain still fails to discharge, the control circuit then
switches to the alarm mode. In this mode the valve
is de-energized and the red alarm light is activated on
the drain and the dryer controller. The valve is then
automatically energized every 4 minutes for 5 seconds.
Check the drain operation. Push drain (push-to-test)
button on the Energy Management Monitor control
board to energize drain. A flow of condensate and/or air
should be present at the drain outlet. The alarm mode
automatically clears after the drain returns to normal
operation.
B. Condensate enters the reservoir
(1)
through the inlet
port. When the condensate level in the reservoir covers
the capacitance sensor, an electronic signal is sent to the
solid state countdown processor. The processor delays
the opening of the solenoid valve for a given period
of time. Once the time has elapsed, the solid state
processor transmits information to energize the coil in
the solenoid valve
(2)
. The magnetic force of the coil
Содержание TF 171E
Страница 14: ...14 WIRING DIAGRAM 575 460 3 60 Transformer Pack...
Страница 18: ...18 NOTES...
Страница 19: ...19...