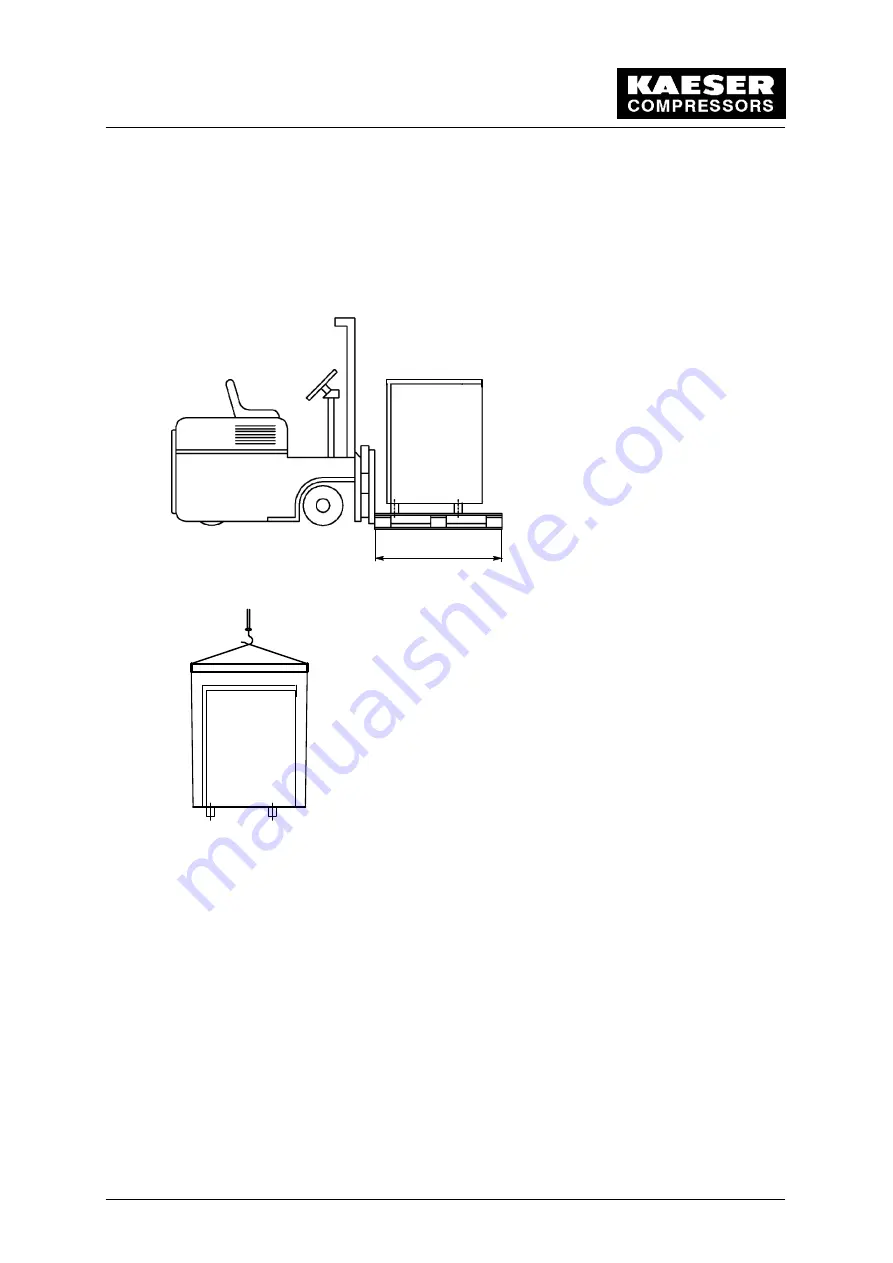
Transport
4 --- 11
4
Transport
4.1
Transport Instructions
We recommend a fork lift truck or lifting equipment for transporting the compressor pack-
age to avoid damage to the cabinet and framework.
min. 32”
Do not exert any side forces on the compressor
unit when transporting with lifting equipment!
Attention :
4.2
Packaging
The packaging provided with this compressor as delivered is intended to safeguard the
package against normal road transport damage. Please dispose of in an environmentally
friendly way and arrange for it to be recycled if possible.
Содержание SM 8
Страница 9: ...Technical Specification 1 6...
Страница 16: ...Construction and Operation 5 13...
Страница 17: ...Construction and Operation 5 14...
Страница 54: ...Appendix 11 51 11 Appendix 11 1 Wiring Diagram...
Страница 55: ......
Страница 56: ......
Страница 57: ......
Страница 58: ......
Страница 59: ......
Страница 60: ......
Страница 61: ......
Страница 62: ......
Страница 63: ......
Страница 64: ......
Страница 65: ......
Страница 66: ......
Страница 67: ......
Страница 68: ......
Страница 69: ......
Страница 74: ...SM 8 SM 11 A 08 B 07 C 14 D 11...
Страница 76: ......
Страница 78: ......
Страница 80: ......
Страница 82: ......