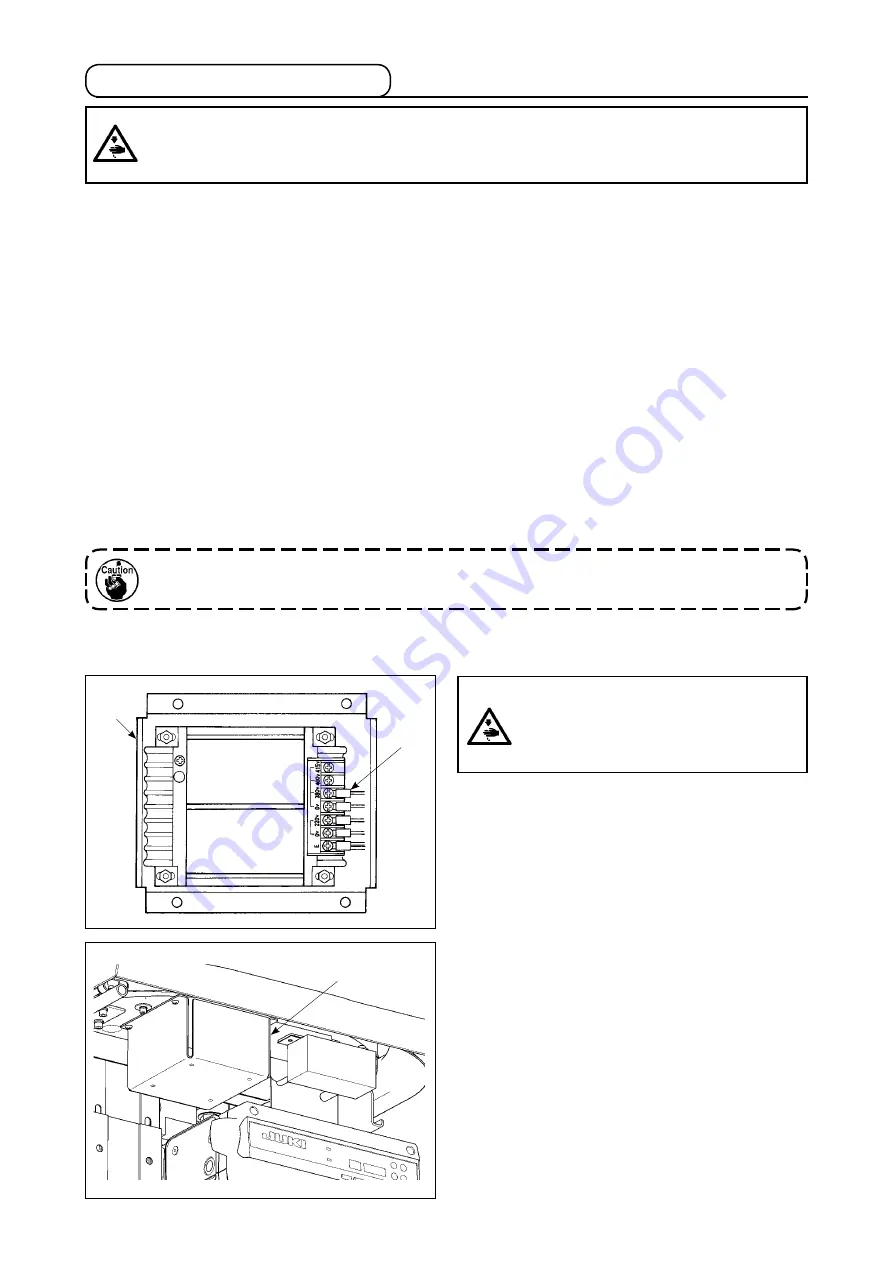
– –
Connection of the power plug to the power depends on the specifications of the product. Adjust the power
plug to the power specifications to connect.
This product performs operation by the single-phase connection for 3-phase 380/400/415V.
[Caution when changing the power source of the high voltage optional transformer]
When usng hgh voltage optonal transformer
1
wth
the nput voltage of 400V or 45V, t s necessary to
replace nput power source cord
2
of hgh voltage
optonal transformer
1
. Change power source nput
cord
2
(sky blue) that s connected to 380V to the
connecton of 400V or 45V.
The hgh voltage optonal transformer
1
s nstalled
on the undersde of the wooden table.
To change over the power supply, remove transform-
er box
3
.
1
2
3-12. Connecting the power plug
1
In case of the product of single-phase, 200 to 240V specifications (CE specifications) :
Connect the sky-blue and brown wres of the power cord to the power termnal (AC00 to 40V) and the
yellow/green wre to the ground (earth) termnal respectvely.
3
In case of the product of 3-phase, 200 to 240V specifications :
Connect the red, whte and black wres of the power cord to the power termnal (AC00 to 40V) and the
yellow/green wre to the ground (earth) termnal respectvely.
4
In case of the product with the optional high voltage transformer :
Connect the black wres (3 peces) of the power cord to the power termnal (AC380 to 45V) and the yel-
low/green wre to the ground (earth) termnal respectvely.
It s possble to connect to 380/400/45V by settng of the nput tap of transformer (standard settng at
the tme of delvery : 380V).
2
In case of the product of single-phase, 200 to 240V specifications (other than CE specifications) :
Connect the black and whte wres of the power cord to the power termnal (AC 00 to 40V), and the
yellow/green wre to the ground (earth) termnal respectvely.
3
CAUTION
:
To prevent possible accidents caused by leakage or dielectric strength, an appropriate power plug
shall be installed by a person who has an expert knowledge of electricity. Be sure to connect the
power plug to the receptacle that is well grounded.
To prevent accidents, perform the work af-
ter leaving the sewing machine alone more
than 4 minutes in the state that the power
switch is turned OFF and the power cord
is drawn out.
Содержание ASN-690
Страница 1: ... ENGLISH ASN 690 INSTRUCTION MANUAL ...