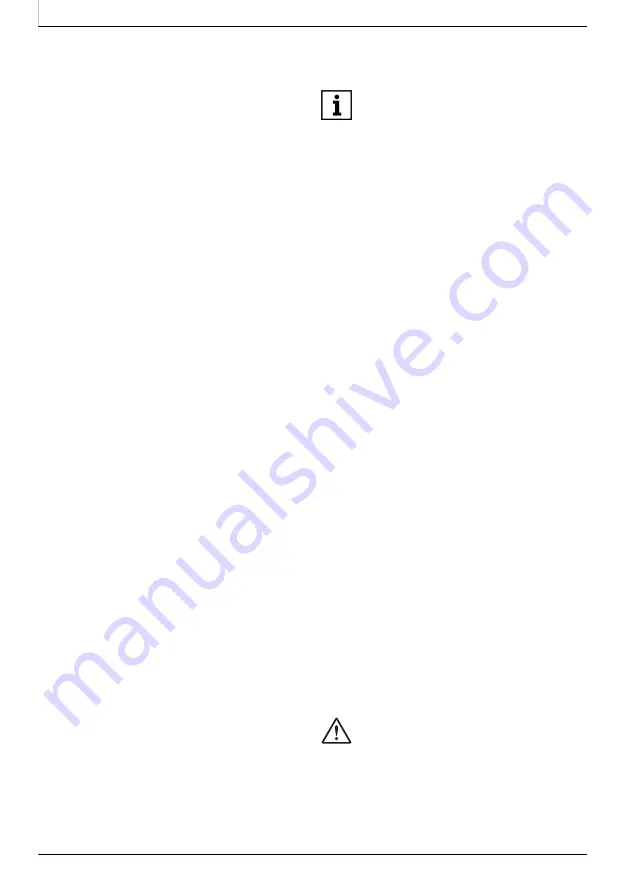
Operation
4
Operation
4.1
Setting the downstream pres-
sure
To compensate for pressure fluctuations
and to protect the downstream installation,
the downstream pressure can be regulated
via the pressure reducer. The factory pre-
set downstream pressure of 4 bar can be
changed to a value between 1.5 bar and
6 bar depending on the upstream pressure:
1.
Undo the countersunk screw on the
handwheel of the pressure reducer.
2.
Turn the handwheel clockwise
(= pressure increase), or turn counter-
clockwise (= pressure reduction).
3.
Open a drawing point behind the device
for a short time. This results in a pres-
sure relief and the set downstream pres-
sure can be read off from the down-
stream pressure gauge.
4.
When the desired downstream pressure
has been reached, retighten the coun-
tersunk screw on the pressure reducer
handwheel to prevent automatic adjust-
ment of the downstream pressure.
4.2
Cleaning of the sieve insert
(backwashing)
A regular cleaning process is necessary to
remove the residues from the sieve fabric
of the device. This process is called
back-
washing
.
Suction pipes are provided for backwash-
ing, which rotate around the sieve fabric
of the fine filter. The backwashing valve
opens on the bottom side of the device.
By reversing the water flow from inside to
outside, deposits on the sieve fabric are
carried away and rinsed out with the back-
wash water. The suction pipes also clean
the inside of the transparent filter bowl with
wiper lips during their movement.
The degree of contamination and cleaning
process can be observed from the outside.
INFO_NO_HEADER
The device is backwashed with
filtered water. The filtered water
supply of the domestic installation
remains intact during the backwash-
ing process. No dirty water can reach
the pure water side during the back-
washing.
4.2.1 Backwashing interval
If cleaning is not performed soon enough,
the result may be damage to the sieve
insert. Large quantities of filtered particles
can deform the sieve fabric and in extreme
case lead to tearing of the sieve fabric.
In addition, larger deposit quantities can
impair the backwashing function mechani-
cally.
According to DIN EN 13443-1 backwashing
the device is required at the latest every six
months.
The manufacturer recommends a back-
washing:
•
at least every 2 months
•
if the water pressure drops
•
if the filter is visibly dirty
Experience has shown that new installa-
tions in the early stages of installation lead
to increased dirt deposits. In this case, a
more frequent backwashing is necessary.
4.2.2 Backwashing
WARNING
Persons who, due to their phys-
ical, sensory or mental abilities
or their inexperience or lack of
knowledge, are unable to operate
the device safely may not operate
it without supervision or instruc-
tion from a responsible person.
1703301 • 2020/07
JUDO JPM-QC
13
Содержание 8165020
Страница 11: ...Installation 3 4 1 Drainage options for the backwash water 1703301 2020 07 JUDO JPM QC 11...
Страница 15: ...When recommissioning the device proceed as with a new installation 1703301 2020 07 JUDO JPM QC 15...
Страница 20: ...Technical data 7 2 Spare parts 20 JUDO JPM QC 1703301 2020 07...