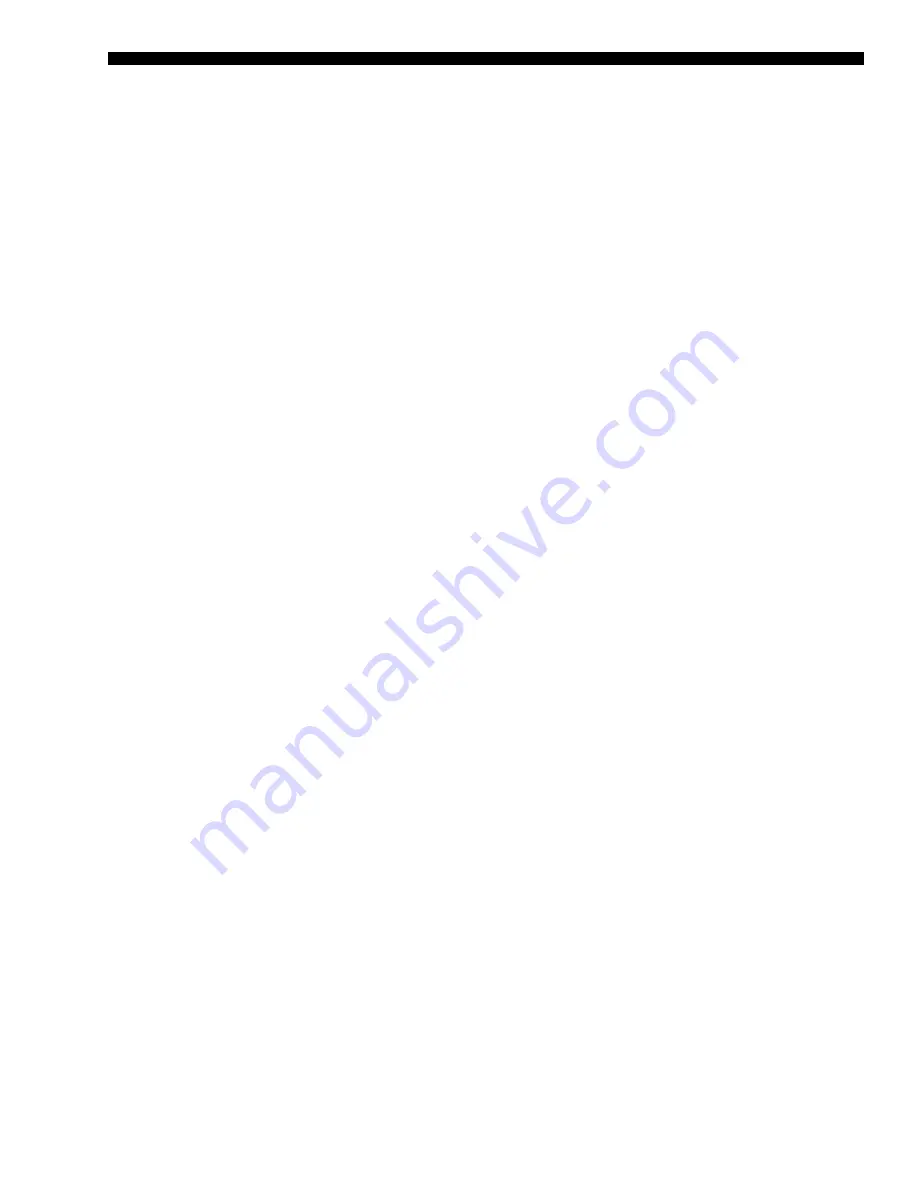
97
JOHNSON CONTROLS
FORM 100.50-EG12 (918)
g.
Safety Grate:
Safety grates capable of supporting a 300 pound center load
shall be provided over bottom supply air (SA) opening.
3.
Fan Motor:
Fan motors shall be NEMA design ball-bearing types with electrical
characteristics and horsepower as specified. Motors shall be 1750 RPM, open drip-
proof type [TEFC optional]. [Optional shaft grounding rings on motors increase mo-
tor longevity when applied with a VFD.] The motor shall be located within the unit
on an adjustable base.
4.
Variable Air Volume (VAV) Fan Control:
Variable Air Volume (VAV) supply fan con-
trol shall be accomplished by using a VFD matched to the supply fan motor HP. The
VFD shall include an integral DC line reactor to reduce harmonic distortion in the
incoming and outgoing power feeds. If a DC line reactor is not provided, an AC line
reactor must be provided. Inlet guide vanes shall not be acceptable. VFD control
keypads shall be located in the control cabinet for accessibility and servicing while
the unit is operating.
Discharge Plenum
Select One of the Following Heat/No Heat Configurations:
1.
Cooling Only:
The discharge air temperature sensor shall be located in the dis-
charge plenum and be located such that it accurately measures the supply air tem-
perature. Walls shall be lined with a solid liner to prevent erosion of the insulation
and separate insulation from the air stream.
2.
Staged Gas Heat:
The heating section shall include an induced draft furnace in two
stages [four stages or six stages] of heating capacity.
Heat Exchanger:
The heat exchanger shall be constructed of tubular aluminized
steel [stainless steel], with stainless steel flue baffles and flue assembly.
Burner and Ignition Control:
The burner shall include a direct-driven induced-draft
combustion fan with energy efficient intermittent pilot spark ignition, redundant main
gas valves with pressure regulator.
Combustion Air Fan:
The inducer fan(s) shall maintain a positive flow of air through
each tube, to expel the flue gas and to maintain a negative pressure within the heat
exchanger relative to the conditioned space.
Safety Devices:
A high limit controller with automatic reset to prevent the heat ex-
changer from operating at an excessive temperature shall be included. A centrifugal
switch on the induced draft fan motor shaft shall prevent ignition until sufficient air-
flow is established through the heat exchanger. A rollout switch shall provide second-
ary airflow safety protection. The rollout switch shall discontinue furnace operation if
the flue becomes restricted.
Flue:
The furnace flue shall be shipped loose to protect it from damage during tran-
sit. The flue shall be field-mounted by the installing contractor. The flue outlet shall be
located above the unit to help prevent recycling of combustion gases back through
the heat exchanger. Agency Certification: Gas heating sections are ETL listed to both
US and Canadian safety standards.
3.
Modulating Gas Heat:
The heating section shall include an induced draft furnace
in 8:1 modulation [16:1, 24:1] of heating capacity.
Heat Exchanger(s):
The heat exchanger(s) shall be constructed of tubular alumi-
nized steel [stainless steel], with stainless steel flue baffles and flue assembly.
Содержание YPAL070
Страница 4: ...JOHNSON CONTROLS 4 THIS PAGE INTENTIONALLY LEFT BLANK FORM100 50 EG12 918 ...
Страница 73: ...73 JOHNSON CONTROLS FORM 100 50 EG12 918 Field Control Wiring Figure 9 FIELD CONTROL WIRING ld08184 ...
Страница 74: ...JOHNSON CONTROLS 74 FORM100 50 EG12 918 Figure 10 FIELD CONTROL WIRING Field Control Wiring Cont d ...