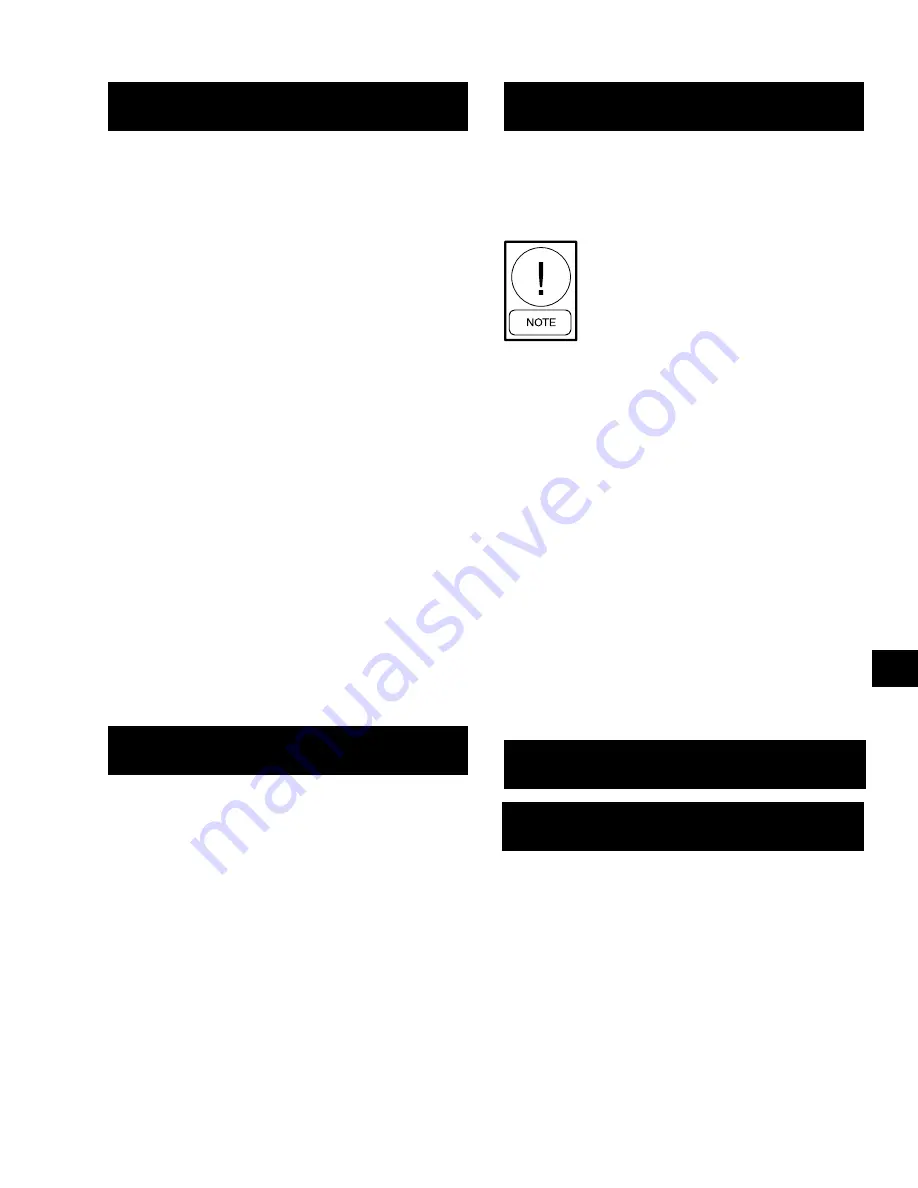
FORM 150.72-NM1 (1020)
129
JOHNSON CONTROLS
7
The Suction Pressure Cutout is a software cutout that
helps protect the chiller from an evaporator freeze-up
should the system attempt to run with a low refrigerant
charge or a restriction in the refrigerant circuit.
Repeated starts after resetting a low
suction pressure fault will cause evapo
-
rator freezeup. Whenever a system
locks out on this safety or any safety,
immediate steps should be taken to
identify the cause.
At system start, the cutout is set to 10% of programmed
value. During the next 3 minutes the cutout point is
ramped up to the programmed cutout point. If at any time
during this 3 minutes the suction pressure falls below the
ramped cutout point, the system will stop.
This cutout is
completely ignored for the first 30 seconds of system run
time to avoid nuisance shutdowns, especially on units
that utilize a low pressure switch in place of the suction
pressure transducer.
After the first 3 minutes, if the suction pressure falls
below the programmed cutout setting, a “transient
protection routine” is activated. This sets the cutout at
10% of the programmed value and ramps up the cutout
over the next 30 seconds. If at any time during this 30
seconds the suction pressure falls below the ramped
cutout, the system will stop.
The Motor Protector/Mechanical High Pressure Cutout
protects the compressor motor from overheating or the
system from experiencing dangerously high discharge
pressure.
This fault condition is present when CR1 (SYS 1) or
CR2 (SYS 2) relays de-energize due to the HP switch
or motor protector opening. This causes the respective
CR contacts to open causing 0VDC to be read on the
inputs to the microboard. The fault condition is cleared
when a 30VDC signal is restored to the input.
S Y S 1 L O W S U C T P R E S S
S Y S 2 L O W S U C T P R E S S
S Y S 1 M P / H P C O F A U L T
S Y S 2 M P / H P C O F A U L T
S Y S 1 M P / H P C O I N H I B
S Y S 2 M P / H P C O I N H I B
The PUMPING DOWN message indicates that a
compressor in the respective system is presently in the
process of pumping the system down. When pumpdown
is initiated on shutdown, the liquid line solenoid or EEV
will close and a compressor will continue to run. When
the suction pressure decreases to the suction pressure
cutout setpoint or runs for 180 seconds, whichever
comes first, the compressor will cycle off.
Fault Safety Status Messages
Safety Status messages appear when safety thresholds
in the unit have been exceeded. Safeties are divided
into two categories – system safeties and unit safeties.
System safeties are faults that cause the individual
system to be shut down. Unit safeties are faults that cause
all running compressors to be shut down. Following are
display messages and explanations.
System Safeties
System safeties are faults that cause individual systems
to be shut down if a safety threshold is exceeded for 3
seconds. They are auto reset faults in that the system
will be allowed to restart automatically after the fault
condition is no longer present. However, if 3 faults on
the same system occur within 90 minutes, that system
will be locked out on the last fault. This condition is then
a manual reset. The system switch (under OPTIONS
key) must be turned off and then back on to clear the
lockout fault. Fault messages will be displayed whenever
a system is locked out.
The Discharge Pressure Cutout is a software cutout in
the microprocessor and is backed-up by a mechanical
high pressure cutout switch located in the refrigerant
circuit. It assures that the system pressure does not
exceed safe working limits. The system will shutdown
when the programmable cutout is exceeded and will be
allowed to restart when the discharge pressure falls 40
PSIG below the cutout.
Discharge transducers must be
installed for this function to operate.
S Y S 1 P U M P I N G D O W N
S Y S 2 P U M P I N G D O W N
S Y S 1 H I G H D S C H P R E S
S Y S 2 H I G H D S C H P R E S
Содержание YORK Tempo YLAA Series
Страница 4: ...JOHNSON CONTROLS 4 FORM 150 72 NM1 1020 THIS PAGE INTENTIONALLY LEFT BLANK...
Страница 12: ...JOHNSON CONTROLS 12 FORM 150 72 NM1 1020 THIS PAGE INTENTIONALLY LEFT BLANK...
Страница 14: ...JOHNSON CONTROLS 14 FORM 150 72 NM1 1020 THIS PAGE INTENTIONALLY LEFT BLANK...
Страница 18: ...JOHNSON CONTROLS 18 FORM 150 72 NM1 1020 THIS PAGE INTENTIONALLY LEFT BLANK...
Страница 36: ...JOHNSON CONTROLS 36 FORM 150 72 NM1 1020 THIS PAGE INTENTIONALLY LEFT BLANK...
Страница 49: ...FORM 150 72 NM1 1020 49 JOHNSON CONTROLS THIS PAGE INTENTIONALLY LEFT BLANK...
Страница 71: ...FORM 150 72 NM1 1020 71 JOHNSON CONTROLS THIS PAGE INTENTIONALLY LEFT BLANK...
Страница 73: ...FORM 150 72 NM1 1020 73 JOHNSON CONTROLS 5 5...
Страница 75: ...FORM 150 72 NM1 1020 75 JOHNSON CONTROLS 5 5...
Страница 77: ...FORM 150 72 NM1 1020 77 JOHNSON CONTROLS 5 5...
Страница 79: ...FORM 150 72 NM1 1020 79 JOHNSON CONTROLS 5 5...
Страница 81: ...FORM 150 72 NM1 1020 81 JOHNSON CONTROLS 5 5...
Страница 83: ...FORM 150 72 NM1 1020 83 JOHNSON CONTROLS 5 5...
Страница 85: ...FORM 150 72 NM1 1020 85 JOHNSON CONTROLS 5 5 LD13901...
Страница 87: ...FORM 150 72 NM1 1020 87 JOHNSON CONTROLS 5 5...
Страница 89: ...FORM 150 72 NM1 1020 89 JOHNSON CONTROLS 5 5 LD13232...
Страница 90: ...JOHNSON CONTROLS 90 FORM 150 72 NM1 1020 Technical Data DUAL PUMP WIRING LD13237 FIG 21 DUAL PUMP WIRING...
Страница 91: ...FORM 150 72 NM1 1020 91 JOHNSON CONTROLS THIS PAGE INTENTIONALLY LEFT BLANK...
Страница 92: ...JOHNSON CONTROLS 92 FORM 150 72 NM1 1020 Technical Data WIRING LD13238 FIG 22 WIRING...
Страница 93: ...FORM 150 72 NM1 1020 93 JOHNSON CONTROLS 5 5 LD13239...
Страница 160: ...JOHNSON CONTROLS 160 FORM 150 72 NM1 1020 Unit Operation FIG 28 CONDENSER FAN LOCATIONSWIRING DIAGRAMS...
Страница 176: ...JOHNSON CONTROLS 176 FORM 150 72 NM1 1020 THIS PAGE INTENTIONALLY LEFT BLANK...
Страница 191: ...FORM 150 72 NM1 1020 191 JOHNSON CONTROLS 10 NOTES...