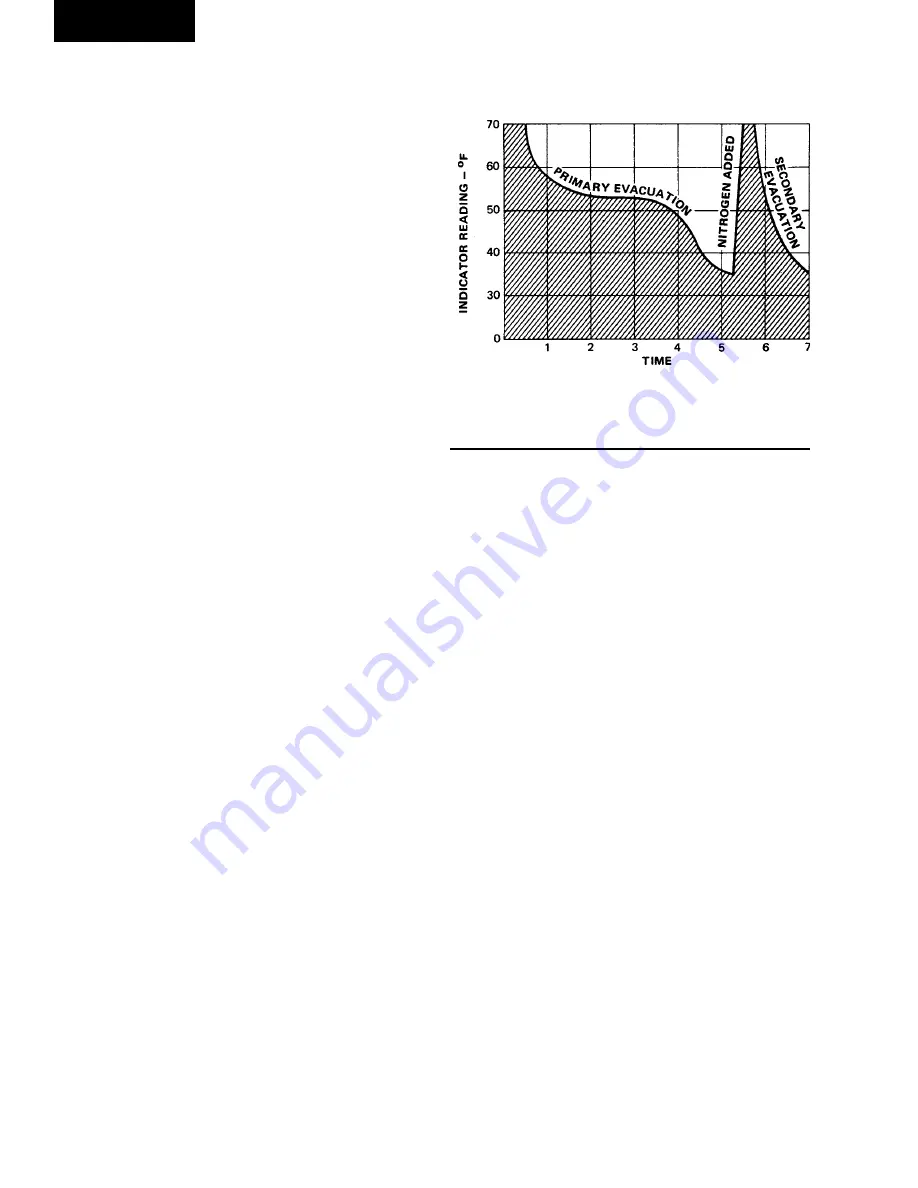
JOHNSON CONTROLS
FORM 160.75-O1 (309)
26
maintenance
Vacuum dehYdration
To obtain a sufficiently dry system, the following instruc
-
tions have been assembled to provide an effective method
for evacuating and dehydrating a system in the field. Al
-
though there are several methods of dehydrating a system,
we are recommending the following, as it produces one of
the best results, and affords a means of obtaining accurate
readings as to the extent of dehydration.
The equipment required to follow this method of de-
hydration consists of a wet bulb indicator or vacuum
gauge, a chart showing the relation between dew point
temperature and pressure in inches of mercury (vacuum),
(See Table 2) and a vacuum pump capable of pumping
a suitable vacuum on the system.
operation
Dehydration of a refrigerant system can be obtained
by this method because the water present in the system
reacts much as a refrigerant would. By pulling down
the pressure in the system to a point where its satu-
ration temperature is considerably below that of room
temperature, heat will flow from the room through the
walls of the system and vaporize the water, allowing
a large percentage of it to be removed by the vacuum
pump. The length of time necessary for the dehydration
of a system is dependent on the size or volume of the
system, the capacity and efficiency of the vacuum pump,
the room temperature and the quantity of water present
in the system. By the use of the vacuum indicator as
suggested, the test tube will be evacuated to the same
pressure as the system, and the distilled water will be
maintained at the same saturation temperature as any
free water in the system, and this temperature can be
observed on the thermometer.
If the system has been pressure tested and found to be
tight prior to evacuation, then the saturation temperature
recordings should follow a curve similar to the typical
saturation curve shown as FIG. 10.
The temperature of the water in the test tube will drop as
the pressure decreases, until the boiling point is reached,
at which point the temperature will level off and remain
at this level until all of the water in the shell is vaporized.
When this final vaporization has taken place the pressure
and temperature will continue to drop until eventually
a temperature of 35°F (1.6°C) or a pressure of 5 mm
Hg. is reached.
When this point is reached, practically all of the air has
been evacuated from the system, but there is still a small
amount of moisture left. In order to provide a medium
for carrying this residual moisture to the vacuum pump,
nitrogen should be introduced into the system to bring it
to atmospheric pressure and the indicator temperature will
return to approximately ambient temperature. Close off
the system again, and start the second evacuation.
The relatively small amount of moisture left will be car-
ried out through the vacuum pump and the temperature
or pressure shown by the indicator should drop uni-
formly until it reaches a temperature of 35°F (1.6°C)
or a pressure of 5 mm Hg.
When the vacuum indicator registers this temperature
or pressure, it is a positive sign that the system is evac-
uated and dehydrated to the recommended limit. If this
level cannot be reached, it is evident that there is a leak
somewhere in the system. Any leaks must be corrected
before the indicator can be pulled down to 35°F or 5
mm Hg. in the primary evacuation.
During the primary pulldown, keep a careful watch on
the wet bulb indicator temperature, and do not let it fall
below 35°F (1.6°C). If the temperature is allowed to fall
to 32°F (0°C), the water in the test tube will freeze, and
the result will be a faulty temperature reading.
fig. 10 –
SATuRATION CuRVE
LD00474
Содержание York MaxE YK Series
Страница 2: ...Page 2 of 2 ...
Страница 3: ......
Страница 4: ......
Страница 5: ......
Страница 6: ......
Страница 7: ......
Страница 8: ......
Страница 9: ......
Страница 10: ......
Страница 11: ......
Страница 12: ......
Страница 13: ......
Страница 14: ......
Страница 15: ......
Страница 16: ......
Страница 17: ......
Страница 18: ......
Страница 19: ......
Страница 20: ......
Страница 21: ......
Страница 22: ......
Страница 23: ......
Страница 24: ......
Страница 25: ......
Страница 26: ......
Страница 27: ......
Страница 28: ......
Страница 29: ......
Страница 30: ......
Страница 31: ......
Страница 32: ......
Страница 33: ......
Страница 34: ......
Страница 35: ......
Страница 36: ......
Страница 37: ......
Страница 38: ......
Страница 39: ......
Страница 40: ......
Страница 41: ......
Страница 42: ......
Страница 43: ......
Страница 44: ......
Страница 45: ......
Страница 46: ......
Страница 47: ......
Страница 48: ......
Страница 49: ......
Страница 50: ......
Страница 51: ......
Страница 52: ......
Страница 53: ......
Страница 54: ......
Страница 55: ......
Страница 56: ......
Страница 57: ......
Страница 58: ......
Страница 59: ......
Страница 60: ......
Страница 61: ......
Страница 62: ......
Страница 63: ......
Страница 116: ...FORM 160 75 O1 309 17 JOHNSON CONTROLS 3 FIG 6 schematic drawing yk compressor lubrication system LD08577a ...
Страница 135: ...JOHNSON CONTROLS FORM 160 75 O1 309 36 SI metric conversion ...
Страница 137: ...JOHNSON CONTROLS FORM 160 75 O1 309 38 NOTES ...
Страница 138: ...FORM 160 75 O1 309 39 JOHNSON CONTROLS NOTES ...