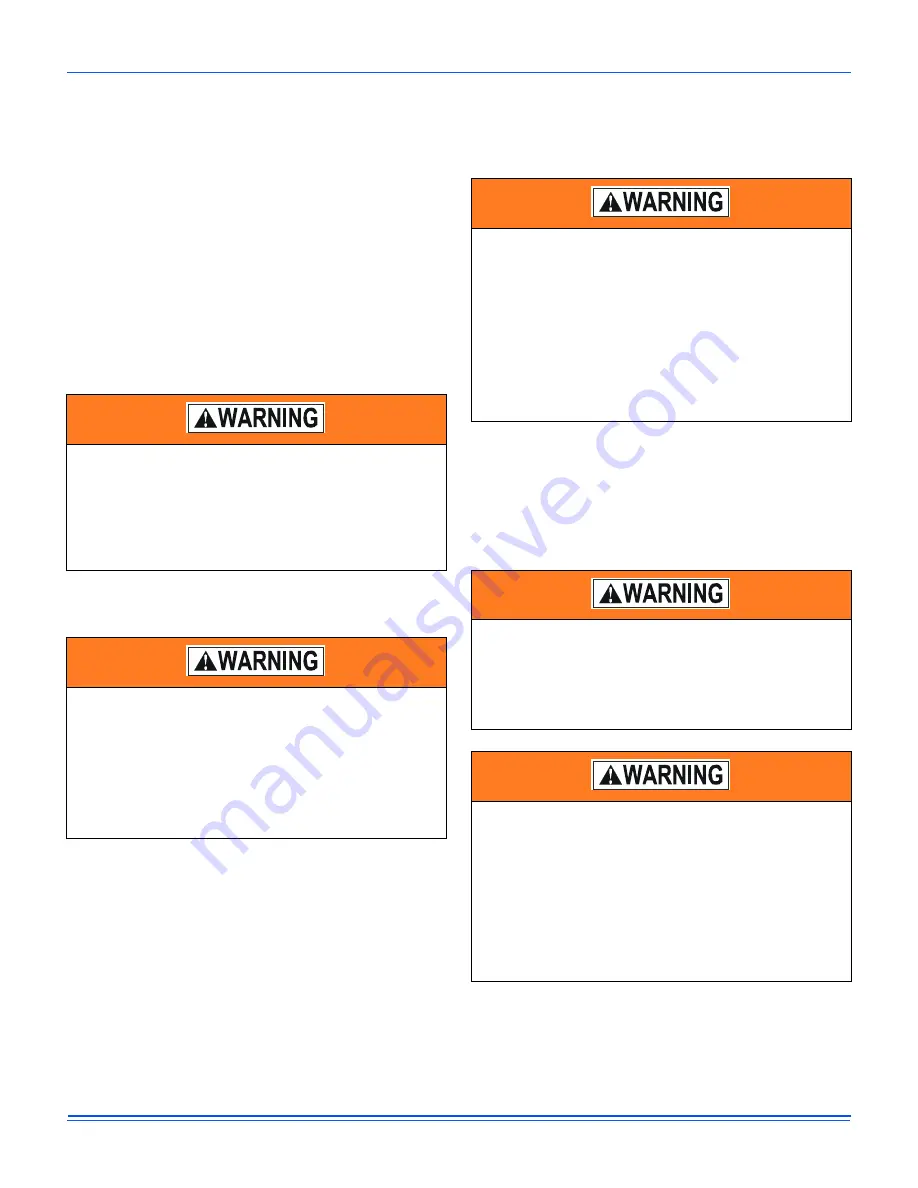
5566020-JIM-C-1019
36
Johnson Controls Ducted Systems
All LP gas equipment must conform to the safety standards of
the National Fire Protection Association.
For satisfactory operation, LP gas pressure must be 10.5 inch
W.C. at the unit under full load. Maintaining proper gas
pressure depends on three main factors:
• The vaporization rate which depends on the temperature
of the liquid and the wetted surface area of the containers.
• The proper pressure regulation. Two-stage regulation is
recommended.
• The pressure drop in the lines between regulators and
between the second stage regulator and the appliance.
The pipe size required depends on the length of the pipe
run and the total load of all appliances.
Complete information regarding tank sizing for vaporization,
recommended regulator settings, and pipe sizing is available
from most regulator manufacturers and LP gas suppliers.
Check all connections for leaks when piping is completed using
a soap solution.
Never use a flame.
Vent and combustion air
Venting slots in the heating compartment access panel remove
the need for a combustion air hood. The gas heat flue exhaust
is routed through the factory-installed exhaust piping with a
screen. If necessary, a flue exhaust extension may be installed
at the point of installation.
Options and accessories
Electric heat
Electric heaters are available as factory-installed options or
field-installed accessories. Refer to electric heat instructions for
installation. These heaters mount in the heat compartment with
the heating elements extending into the supply air chamber. All
electric heaters are fused and intended for use with single point
power supply.
Smoke detectors
The factory-installed smoke detector shuts down operation of
the unit by interrupting power to the UCB when smoke is
detected within its mounting compartment. The smoke detector
option is available for both supply and return air configurations.
Be aware that the supply air configuration has the sensor com-
ponent mounted in the blower section with its control module
mounted in the return air compartment.
You must test and maintain the detector on a regular basis
according to NFPA 72 requirements. You must clean the
detector at least once a year. For specific troubleshooting and
maintenance procedures, refer to the smoke detector's
installation instructions that accompany the unit.
LP gas is an excellent solvent and will quickly dissolve
white lead and most standard commercial compounds. A
special pipe dope must be used when assembling
wrought iron or steel pipe for LP. Shellac base
compounds such as Gaskolac or Stalastic, and
compounds such as Rectorseal #5, Clyde’s, or John
Crane may be used.
Fire or explosion hazard
Failure to follow the safety warning exactly could result
in serious injury, death, or property damage.
Never test for gas leaks with an open flame. Use a
commercially available soap solution made specifically
for the detection of leaks to check all connections. A fire
or explosion may result causing property damage,
personal injury, or loss of life.
The use of duct smoke detectors have specific limitations
as established by the National Fire Protection
Association. Note that duct smoke detectors are not a
substitute for other fire detection systems, including the
following.
• An open area smoke detector
• Early warning detection
• A building's regular fire detection system.
Refer to NFPA Code 72 and Standard 90A for additional
information.
Factory-installed smoke detectors may be subjected to
extreme temperatures during off times due to outside air
infiltration. These smoke detectors have an operational
limit of -4°F to 158°F. To prevent false alarms, you must
relocate smoke detectors installed in areas that could be
outside this range.
To ensure that adequate airflow reaches the smoke
detector's sensor, make sure that the holes of the
sampling tube face into the air stream, and that the far-
end of the sampling tube is sealed with the plastic end
cap.
The unit's supply airflow must be adjusted to provide a
pressure differential across the smoke detector's
sampling and exhaust ports of at least 0.01 inches of
water and no more than 1.11 inches of water, as
measured by a manometer.