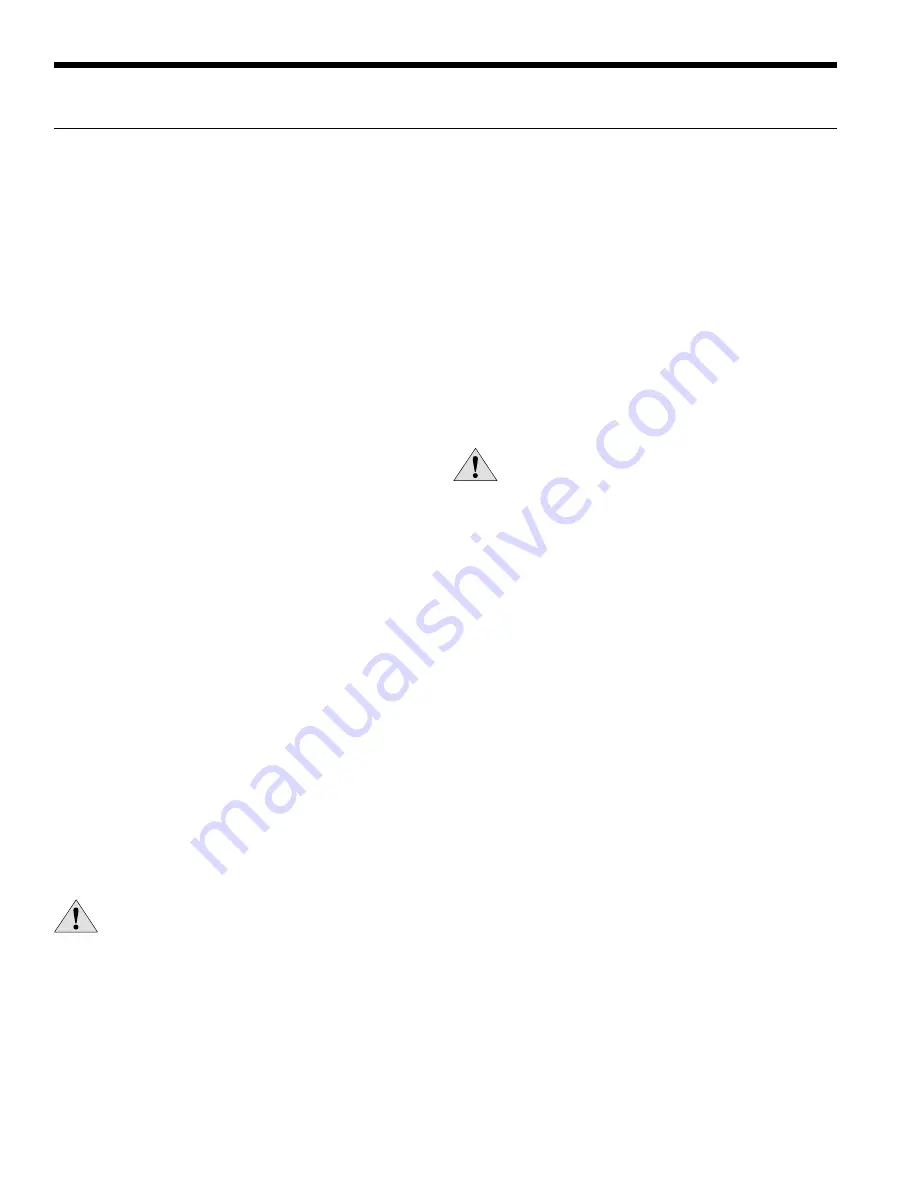
10
RW SERIES REVERSIBLE CHILLER INSTALLATION MANUAL
General
System piping should be kept as simple as possible to minimize
the pressure drop, but hand valves should be field installed to
facilitate unit servicing. The piping installation should provide
service personnel with the ability to measure and/or monitor water
temperatures and pressures.
Source and load fluid connections are provided with 2-inch
[50.8mm] Victaulic grooved nipples (see Figure 4). Each nipple will
also have a PT port installed for test and balance purposes. It will
be the installing contractor’s responsibility to adequately support
incoming piping to avoid damage to the unit’s piping or heat
exchangers. The water lines should be routed so as not to interfere
with access to the unit.
For any installation where the transmission of vibration through
the piping connections could cause unacceptable noise levels
in occupied spaces it is important to provide adequate vibration
damping. One method is to use the optional Adapter Hose Kit (kit
number TKC16S-4). This Kit consists of four pieces of a braided
stainless steel flexible hose with a 2” Victaulic connection on one
end and a 2” MPT connection with pipe union on the other. Overall
length of each piece is 18”.
NOTE:
Units are factory run-tested using propylene glycol. Prior to
connecting piping to unit, thoroughly flush heat exchangers.
Before final connection to the unit, the supply and return hose
kits must be connected to each other, bypassing the unit, and
the system flushed to remove dirt, piping chips and other foreign
material. Normally, a combination balancing and close-off (ball)
valve is installed at the return, and a rated gate or ball valve is
installed at the supply. The return valve can be adjusted to obtain
the proper water flow. The valves allow the unit to be removed
for servicing.
The proper water flow must be delivered to each unit whenever the
unit heats or cools. The proper flow rate cannot be accurately set
without measuring the water pressure drop through the refrigerant-
to-water heat exchanger.
A 3 GPM flow rate per ton [0.054 LPS
per kW] of cooling capacity (2.25 GPM per ton [0.0404 LPS per
kW] minimum) is required.
Field Connected Water Piping
CAUTION: Remove the plastic protective caps in the ends of each of the four water pipes on the heat exchangers
prior to piping connection. Failure to remove the caps will result in serious damage and could void the warranty.
NOTE
: The placement and connection of the water circulating
pump(s) must be taken into consideration prior to designing the
final water piping systems.
Closed Loop Tower/Boiler Systems
The water loop is usually maintained between 60°F [15.5°C] and
90°F [32.2°C] for proper heating and cooling operation. This is
accomplished with a cooling tower and a boiler.
To reject excess heat from the condenser water loop, the use of a
closed-circuit evaporative cooler or an open type cooling tower with
a secondary heat exchanger between the tower and the condenser
water loop is recommended. If an open type cooling tower is
used without a secondary heat exchanger, continuous chemical
treatment and filtering of the water must be performed to ensure
the water is free from damaging materials.
CAUTION: Water piping exposed to outside
temperature may be subject to freezing.
Open Loop Well Water Systems
Installation of an open loop system is not recommended without
using a secondary heat exchanger unless water quality guidelines
are met.
Earth Coupled Systems
All supply and return water piping should be insulated to
prevent excess condensation from forming on the water lines.
Ensure pumping system is capable of providing adequate flow
rate at the system pressure drop, 3.0 GPM per ton [0.054 LPS
per kW] (source side) is recommended. Antifreeze in the loop
is strongly recommended.
Содержание RW Series
Страница 39: ...THIS PAGE INTENTIONALLY LEFT BLANK ...