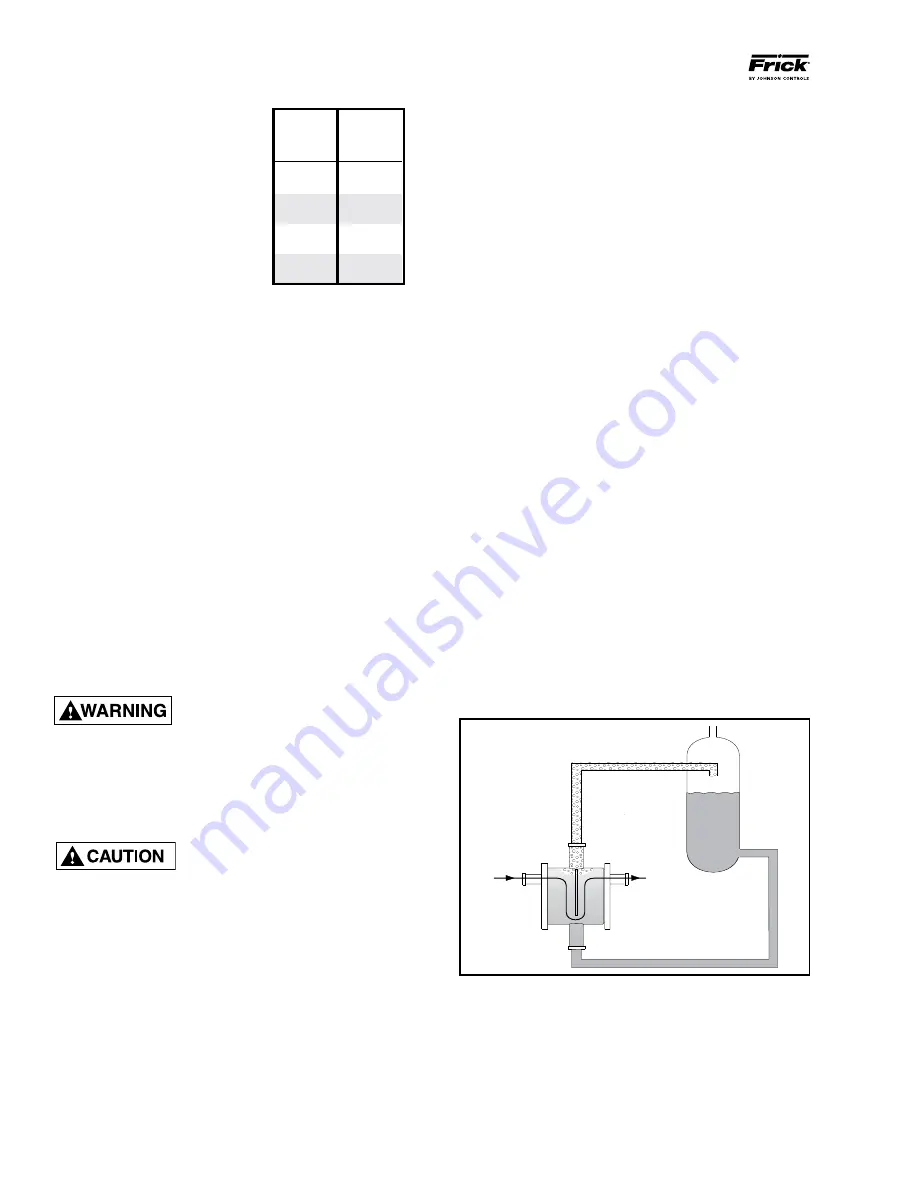
RWF ROTARY SCREW COMPRESSOR UNITS
INSTALLATION
S70-600 IOM (OCT04)
Page 6
100
55
134
55
177
120
222
120
270
120
316
140
399
140
480
150
OIL CHARGE
The normal charging level is mid-
way in the top sight glass located
midway along the oil separator
shell.
Normal operating level is
midway between the top and bottom
sight glass. The table gives the ap-
proximate oil charge quantity.
*Includes total in oil separator and
piping. Add 5 gal. for oil cooler up to
Model 270, 10 gal. for 316 - 480.
Add oil by attaching the end of a suitable pressure type
hose to the oil charging valve, located on the top of the oil
separator between the compressor and motor. Using a pres-
sure-type pump and the recommended Frick
®
oil, open the
charging valve and pump oil into the separator.
NOTE: Fill
slowly because oil will fill up in the separator faster than
it shows in the sight glass.
Oil distillers and similar equipment which act to trap oil must
be filled prior to unit operation to normal design outlet levels.
The same pump used to charge the unit may be used for
filling these auxiliary oil reservoirs.
NOTE: The sight glass located in the coalescing end
of the separator near the discharge connection should
remain empty.
OIL HEATER(S)
Standard units are equipped with two or three 500 watt oil
heaters, providing sufficient heat to maintain the oil tem-
perature for most indoor applications during shutdown cycles
to permit safe start-up. Should additional heating capacity
be required because of low ambient temperature, contact
Frick
®
. The heaters are energized only when the unit is not
in operation.
DO NOT ENERGIZE THE HEATERS
when there is no oil in the unit, the
heat ers will burn out. The oil heat-
ers will be energized whenever 120 volt control power is
applied to the unit and the com pressor is not run ning,
unless the 16 amp circuit breaker in the micro enclosure
is turned off.
OIL FILTER(S)
Use of filter elements other than
Frick may cause warranty claim
to be denied.
The oil filter(s) and coalescer filter element(s) shipped with
the unit are best suited to ensure proper filtration and op-
eration of the system.
THERMOSYPHON OIL COOLING
Thermosyphon oil cooling is an economical, effective method
for cooling oil on screw compressor units. Ther mosyphon
cooling utilizes liquid refrigerant at condenser pressure and
temperature that is partially vaporized at the condenser tem-
perature in a plate and shell vessel, cooling the oil to within
15°F of that temperature. The vapor, at condensing pressure,
is vented to the condenser inlet and reliquified. This method is
the most cost effective of all currently applied cooling systems
since no compres sor capacity is lost or compressor power
penalties in curred. The vapor from the cooler need only be
con densed, not compressed. Refrigerant flow to the cooler is
automatic, driven by the thermosyphon principle and cooling
flow increases as the oil inlet temperature rises.
EQUIPMENT
- The basic equipment required for a ther-
mosyphon system consists of:
1.
A source of liquid refrigerant at condensing pressure and
temperature, located in close proximity to the unit to mini-
mize piping pressure drop. The liquid level in the refrigerant
source must be 6 to 8 feet minimum above the center of the
oil cooler.
2.
A plate and shell oil cooler with:
Plate Side: Oil 400 lb design
Shell Side: Refrigerant 400 lb design
Due to the many variations in refrigeration system design
and physical layout, several systems for assuring the above
criteria are possible.
SYSTEM OPERATION
- Liquid refrigerant fills the cooler
shell side up to the Thermosyphon receiver liquid level.
Hot oil (above the liquid temperature) flowing through the
cooler will cause some of the refrigerant to boil and vaporize.
The vapor rises in the return line. The density of the refrig-
erant liquid/vapor mixture in the return line is considerably
less than the density of the liquid in the supply line. This im-
balance provides a differential pressure that sustains a flow
condi tion to the oil cooler. This relationship involves:
1.
Liquid height above the cooler.
2.
Oil heat of rejection.
3.
Cooler size and piping pressure drops.
Current thermosyphon systems are using two-pass oil cool-
ers and flow rates based on 3:1 overfeed.
The liquid/vapor returned from the cooler is separated in the
receiver. The vapor is vented to the condenser inlet and need
only be reliquified since it is still at condenser pressure. See
Figure 2.
BASIC*
CHARGE
(gal.)
RWF
MODEL
NO.
Figure 2
OIL TEMPERATURE CONTROL
- Oil temperature will gen-
erally run about 15 - 35°F above condensing tempera ture.
In many cases, an oil temperature control is not required if
condensing temperature is above 65°F as oil tempera ture
can be allowed to float with condenser temperature.
Condensing Temperature:
65°F - 105°F
Oil Temperature:
80°F - 140°F
HOT OIL IN
FROM
SEPARATOR
120-140 F
OIL OUT
O
TO SYSTEM CONDENSER
95 F
2.5#/FT
O
3
95 F
36#/FT
O
3
TS RECEIVER
Содержание Frick RWF 100
Страница 40: ...RWF ROTARY SCREW COMPRESSOR UNITS MAINTENANCE S70 600 IOM OCT04 Page 40 P I DIAGRAM ...
Страница 43: ...RWF ROTARY SCREW COMPRESSOR UNITS MAINTENANCE S70 600 IOM OCT04 Page 43 P I DIAGRAM LIQUID INJECTION BOOSTER ...
Страница 52: ...RWF ROTARY SCREW COMPRESSOR UNITS MAINTENANCE S70 600 IOM OCT04 Page 52 OPERATING LOG SHEET ...
Страница 57: ...RWF ROTARY SCREW COMPRESSOR UNITS MAINTENANCE S70 600 IOM OCT04 Page 57 ...