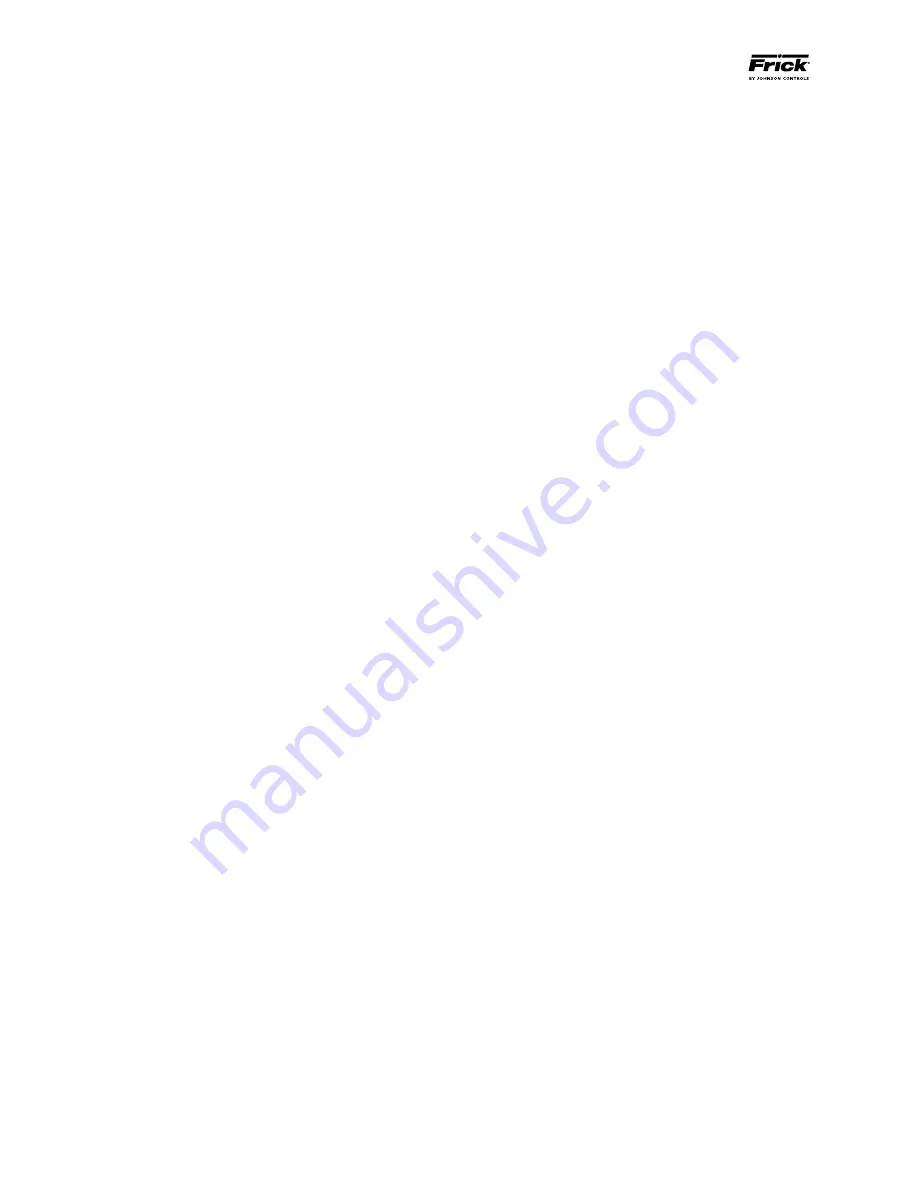
RWF ROTARY SCREW COMPRESSOR UNITS
OPERATION
S70-600 IOM (OCT04)
Page 16
COMPRESSOR OIL COOLING SYSTEMS
The RWF unit can be equipped with one of several systems
for controlling the compressor oil tempera ture. They are single
or dual-port liquid injection and thermo syphon or water-
cooled oil coolers. Each system is autom ati cally controlled,
independent of compressor loading or unloading.
Oil cooling systems should maintain oil temperature within
the following ranges for R-717 and R-22:
Liquid Injection
External*
Oil Cooling
Oil Cooling
130 - 170°F
120 - 160°F
* Thermosyphon oil cooling (TSOC) or Water cooled oil
cooling (WCOC).
SINGLE-PORT LIQUID INJECTION
The single-port liquid injection system is desig ned to permit
liquid refrigerant injection into one port on the compressor
at any given moment and operates as outlined.
Solenoid valve YY5 is energized by the micro processor
when the temperature sensor, in stalled in the oil manifold,
exceeds the LICO set point. High-pressure liquid refriger ant
is then supplied to the tempera ture control valve (TCV). The
temperature control valve is equal ized to a constant back
pressure by the dif feren tial pressure control valve (PDCV).
The differential pressure control valve uses dis charge gas
to maintain downstream pressure. The gas downstream of
the differential pressure control valve is bled off to the com-
pressor suction to ensure steady and constant opera tion of
the valve.
Refer to P & I DIAGRAMS section for piping
and instrumentation drawings.
BOOSTER OR SWING DUTY APPLICATION
Discharge gas from the high-stage compressor is required
to assist the differen tial pressure control valve (PDCV) in
providing the temperature control valve (TCV) with a constant
back pressure.
A solenoid valve YY6 is installed before the differential
pressure control valve (PDCV) to prevent migration of high
pressure gas during shutdown. A Frick-installed timer limits
the high pressure gas to only thirty seconds duration, since
intermediate gas pressure and spring tension are sufficient to
maintain closure on unit shutdown. A metering valve is also
provided for use as a service valve and to allow discharge
gas flow regulation to prevent excessive force and resulting
closure “hammering”.
A field-installed 1/4 inch OD tubing connection is required
between the high stage compressor discharge piping line (or
receiver) and the check valve.
Refer to P & I DIAGRAMS
section for piping and instrumentation drawings.
NOTE: An oil pump may be required for booster or swing
duty applications.
DUAL-PORT LIQUID INJECTION
The dual-port liquid injection system is design ed to obtain
the most efficient compressor performance at high and low
compression ratios by permitting injection of liquid refriger ant
into one of two ports optimally located on the com pressor.
This minimizes the performance penalty incurred with liquid
injection oil cooling.
The dual-port system contains all the com ponents of the
single-port system with the addition of a double acting so-
lenoid valve YY7 and operates as outlined.
Solenoid valve YY5 is energized by the micro processor when
the temperature sensor, in stalled in the oil manifold, exceeds
the LICO set point. Liquid refrigerant is then passed through
the tempera ture control valve (TCV) to the doub le-acting so-
lenoid valve YY7. Depending on the compressor’s operating
volume ratio (Vi), the micropro cessor will select the flow of
the liquid refrigerant to either com pressor port SL-1 or SL-2,
whichever is more efficient.
When the compressor operates BELOW 3.5 Vi, compres sor
port SL-1 supplies the liquid cool ing. When the (Vi) rises
ABOVE 3.5 Vi, port SL-2 supplies the liquid cooling.
The temperature control valve is equalized to a constant back
pressure by the differential pres sure control valve (PDCV).
Both the differential pressure control valve (PDCV) and the
double-acting solenoid valve YY7 use discharge gas to main-
tain downstream pressure. The gas downstream of both valves
is bled off to the compres sor suction to ensure steady and
constant operation of the valves.
Refer to P & I DIAGRAMS
section for piping and instrumentation drawings.
LIQUID INJECTION ADJUSTMENT
PROCEDURE
Adjustments must be made to ensure the oil is at the proper
temperature. When the adjustments have been made cor-
rectly, the oil temperature, the discharge temperature and
the temperature of the oil in the separator should all be ap-
proximately the same. (Refer to P&I Diagram)
Carefully insert The bulb from the thermal expansion valve
( TXV ) into the well in the discharge pipe between the com-
pressor and the oil separator. Then open the valve to the oil
separator high pressure connection.
Next, open the refrigerant supply valve, remove the cap on
the pressure regulating valve (PCV ), and close the adjust-
ing valve.
For low temperature oil – 125° to 135°F
After the unit has been started, wait for the oil temperature to
reach 122°F. This is the preprogrammed temperature to open
the liquid feed solenoid in the liquid injection supply line.
Open the adjusting valve only until the needle on the gauge
begins to move a very small amount.
Next, adjust the pressure regulating valve to approximately
80 psig by turning the adjustment ring inside the top of the
valve with a 5/16" Allen wrench. Turn the wrench clockwise
to raise the oil temperature, and counterclockwise to lower
the oil temperature.
Содержание Frick RWF 100
Страница 40: ...RWF ROTARY SCREW COMPRESSOR UNITS MAINTENANCE S70 600 IOM OCT04 Page 40 P I DIAGRAM ...
Страница 43: ...RWF ROTARY SCREW COMPRESSOR UNITS MAINTENANCE S70 600 IOM OCT04 Page 43 P I DIAGRAM LIQUID INJECTION BOOSTER ...
Страница 52: ...RWF ROTARY SCREW COMPRESSOR UNITS MAINTENANCE S70 600 IOM OCT04 Page 52 OPERATING LOG SHEET ...
Страница 57: ...RWF ROTARY SCREW COMPRESSOR UNITS MAINTENANCE S70 600 IOM OCT04 Page 57 ...