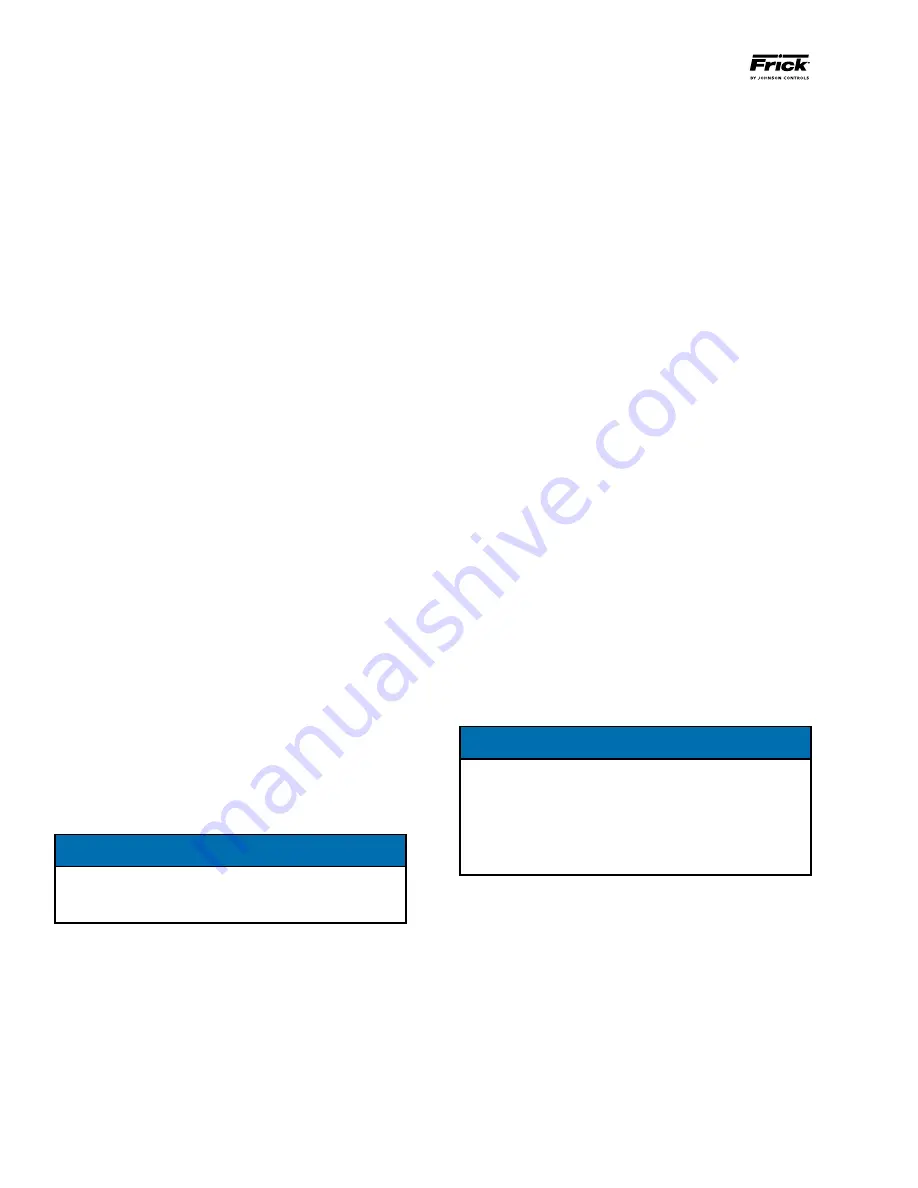
FRICK
®
QUANTUM
™
HD VILTER
®
RETROFIT
INSTALLATION INSTRUCTIONS
090.040-I02 (AUG 2014)
page 4
7.
The existing temperature sensors must be replaced. The
temperature sensor kit that comes with the
QUANTUM
™
HD
retrofit includes the following.
4 - ICTD, 1/4" MPT, temperature sensors (suction,
discharge, oil and separator temperature)
4 - 24', 2 wire, shielded cables with integrated DIN
connector
1 - 4-hole, 3/4" strain relief
Once each of the new temperature sensors are prop-
erly installed, plug in the cables and route back to the
QUANTUM
™
HD
where they will be gathered and ran through
the 4-hole 3/4" strain relief provided in the kit. Use one of
the 4 holes provided at the bottom left side of the enclosure
for the entry of these cables.
8.
Before making the final wiring connection for the tem-
perature sensors, refer to the multipage drawing that is
provided in the new controller or the panel wiring diagrams
in the 090.040-M publication. Temperature probe cabling
is grounded at the ground block in the panel. Cut off the
shield and drain wire at the probe end and use heat shrink
or electrical tape to cover the bare wire, preventing contact
with ground.
9.
Connect the red (or white) and black wires to the analog
I/O board as shown on the on the panel wiring diagrams in
the 090.040-M publication.
10.
If the existing pressure transducers are not the newer
4-20mA type, they must be replaced. The signal from the
older standard Vilter
®
pressure transducer is not a standard
sensor signal range.
The pressure transducer kit that comes with the
QUANTUM
™
HD
retrofit includes the following.
1 - 0-200psia 1/4" MPT Transducer (suction pressure)
3 - 0-500psia 1/4" MPT Transducer (discharge, oil &
pre-filter pressure)
4 - 24', 3 wire, shielded cables with integrated DIN
connector
1 - 4-hole, 3/4" strain relief
Once each of the pressure transducers are properly installed,
plug in the cables and route back to the
QUANTUM
™
HD
.
Gather the cables and run through the 4-hole 3/4" strain relief
provided in the kit. Use one of the 4 holes provided at the
bottom left side of the enclosure for the entry of these cables.
NOTICE
If the existing sensors are 4-20mA they can be used
and need to be configured properly for signal type and
range in Analog I/O Configuration.
11.
Refer to the panel wiring diagrams in the Maintenance
manual (090.040-M or 090.020-M) and connect the red,
black, and white wires of the pressure transducers to the
QUANTUM
™
HD
analog board. The shield of the transducer
cable is grounded inside the transducer and should not be
grounded inside the cabinet.
12.
The motors/actuators for the capacity and volume slides
need to be the current optical actuators. If the existing motors
are the old gear driven type, these will need to be replaced
with the optical actuators before proceeding.
The position feedback cable from the capacity and volume
slide actuators will be routed back to the
QUANTUM
™
HD
and through 2 of the 4 holes in the 3/4" strain relief that
is provided. The capacity slide actuator is the one that is
physically higher on the compressor. To avoid any incidental
damage, disconnect the cables for control and signal at the
optical actuators before wiring these devices to the digital
and analog boards. They will be reconnected later..
13.
Refer to the Vilter
®
specific drawings that come with
the
QUANTUM
™
HD
for instruction on properly landing the
power, signal and common wires of the signal cable for the
capacity and volume slide position on the analog I/O board.
These drawings also include connection information for the
load, unload and common wire for the control cable to the
digital board.
14.
Before starting the AC control wiring, the following items
should be checked in the compressor starter. Refer to the
compressor motor starter diagrams.
A.
The compressor requires a minimum of 2 KVA trans-
former for 120 VAC control and heater power.
B.
The compressor starter must have a ground wire
pulled from the three-phase source. The ground
must be connected to the starter backplate and the
neutral terminal (2) on the secondary side of the
control transformer.
C.
Verify that the current transformer (CT) is placed as
shown on the motor starter diagram in the motor
starter IOM and is sized according to the CT selection
calculation.
D.
Verify that auxiliary contacts are provided on the
compressor and oil pump contactor.
E.
Verify that the compressor motor overloads are sized
properly.
F.
If the compressor and oil pump starters do not have
interposing relays already provided, the relays must
be mounted and wired as shown on the drawings.
NOTICE
The most common electronic control panel problems
are due to undersized AC power wiring, poor grounds,
and control power supplied from lighting panels that
have other devices tied to them that generate large
amounts of AC line noise. please follow these directions
carefully.
(See p.8 for additional information on Installing
Electronic Equipment in an Industrial Environment.)
Metal oxide varistors (MOV or surge suppressor) are recom-
mended for the compressor starter coil, oil pump starter coil
(if applicable) and liquid injection solenoid coil (if applicable).
The MOVs should be placed directly at the coils of these de-
vices. Placement of the MOVs at the control panel terminal
strip negates the surge suppression effect.
15.
Using 10 AWG wire, connect the control transformer in
the compressor starter panel to the proper terminals in the
QUANTUM
™
HD
control panel, as shown in the IOM on the
compressor motor starter diagrams and the panel wiring
diagrams. These wires are: black or red (1), white (2), and
green (GND). (Copper ground only. Conduit ground is not
acceptable.)