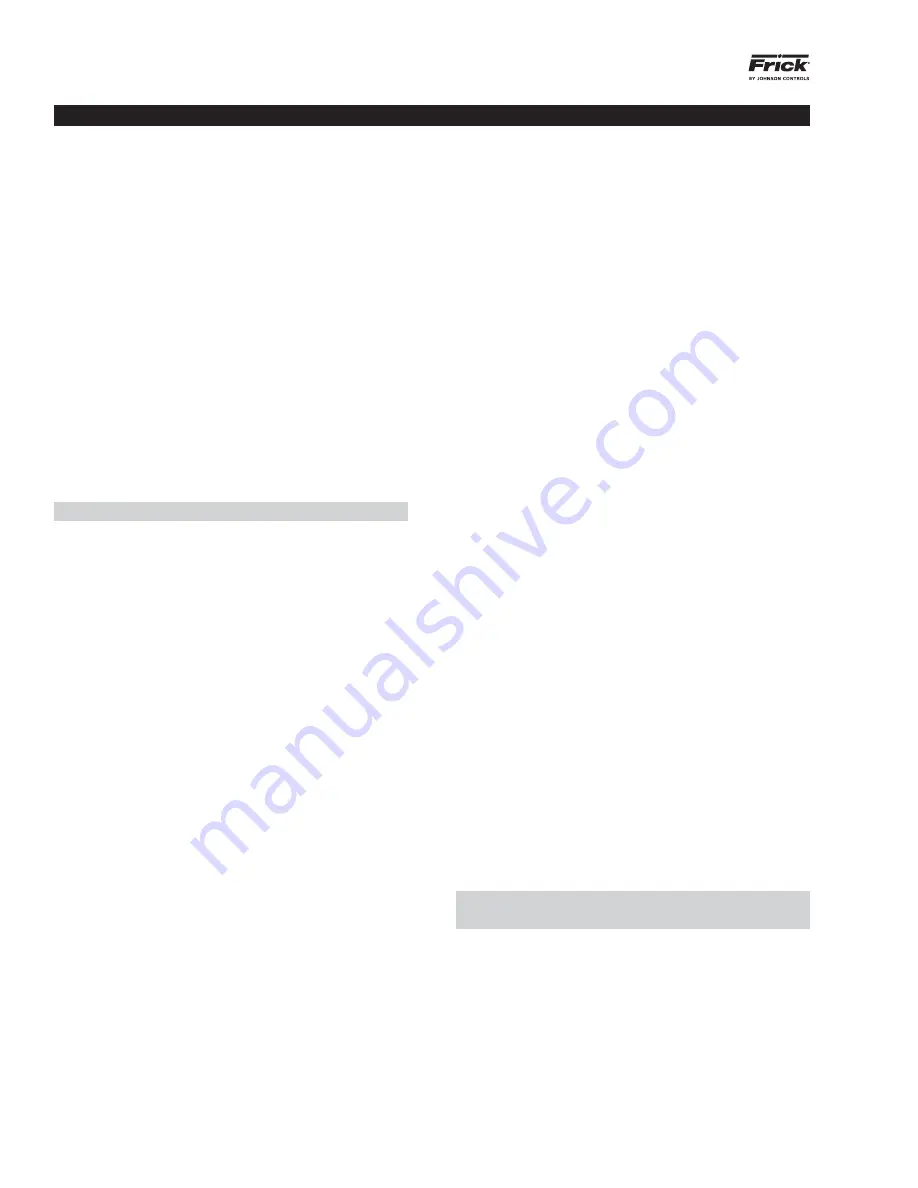
IDC INDUCED DRAFT EVAPORATIVE CONDENSERS
MAINTENANCE
S140-500 IOM (FEB 08)
Page 24
Section 5.0 Troubleshooting
Accurate troubleshooting is greatly facilitated by knowing
proper unit capacities, dimensions, and other specifi cations.
Detailed information for specifi c units is provided in the form
of a drawing package shipped/submitted with the equipment
delivery. Reference
Figure 5-1. IDC Series Standard Unit
Specifi cations
and
Figure 5-2. IDC Series Standard Unit
Dimensions
for basic design, capacities, and troubleshooting
data for Imeco IDC units.
Once it is found that a unit is not performing to specifi cations,
experienced maintenance personnel know that a methodical
troubleshooting approach signifi cantly reduces the time nec-
essary to pinpoint appropriate responses. Use of the following
troubleshooting guide is strongly recommended to minimize
unnecessary repair costs and downtime.
The key to effi cient use of the troubleshooting guide is to
eliminate the simplest cause(s) until it is possible to isolate
the specifi c problem/s that need to be rectifi ed. For example,
a fi ve-minute determination of local ambient wet bulb tem-
perature may prove that a unit is operating under extreme
weather conditions. A maintenance troubleshooting “log” can
prove invaluable in keeping up-to-date on such conditions
and issues.
The following discussion details possible conditions and re-
lated causes for troubleshooting IDC condenser units:
5.1 Condition: High Condensing Pressure
Possible Cause # 1: IDC Unit / Cooling System Power
Failure Or Brownout
•
Check all fans, pumps, and control panels, for inter-
nal power distribution failures (such as blown fuses or
overloads) or eliminate them from consideration. Also,
determine if the utility or stand-by power supply back up
has failed to supply adequate, consistent power. Should
main or standby power supply equipment need updating,
contact a local electrical expert or design/build contractor
to provide for consistent power.
Possible Cause # 2: Excessive Wet Bulb Temperature
•
Wet bulb temperature can be determined by using a “sling
sychrometer” to take a reading near the inlet of the cooling
tower/s. Background or ambient wet bulb is determined
with the sling sychrometer at an upwind location or by
cross-referencing local ambient “dry bulb” and humidity
levels.
•
If background wet bulb is in specifi cation and the wet bulb
at the inlet is out of specifi cation – exhaust air recirculation
may be excessive. Refer to the siting discussion provided in
Section 1.0 and consult with the cooling system engineer
to determine if re-siting or other cooling system changes
are needed.
Possible Cause # 3: Insuffi cient Water Flow/Pressure
To Spray Tree
•
Check water fl ow and pressure at the IDC inlet pipe con-
nection. Even if this was checked and confi rmed at the time
of start-up, changes to plant water supply or internal piping
may have created additional pressure drops (line losses)
between the pump/s and the spray tree connection.
•
The IDC spray-piping tree requires 2-10 PSI at the connec-
tion at the fl ow rates (in GPM) specifi ed for the unit. This
information is available from the local representative.
•
For remote pump applications, water must be supplied
at the pressure and fl ow rate specifi ed on the customer
drawings.
Possible Cause # 4: Inadequate Water Distribution
•
In the event that a few nozzles prove to be clogged or
restricted, it may be necessary to remove the spray
piping “tree” and clean all of the nozzles thoroughly (as
discussed in Section 4.0 Maintenance). This will ensure
that all nozzles are clean and properly realigned before
re-installing the spray tree.
Possible Cause # 5: Low Fan Output
•
Check fan voltage and amp draw readings and compare
to specifi cations. If amp draw is excessive, check airfl ow
pathways to ascertain that no restrictions exist. Restrictions
may be blocking fl ow through intake louvers, eliminators,
or the fan guard. Clear all air restrictions and rotate fan to
check for binding blade tips in the orifi ce.
•
If the fan has an adjustable-pitch propeller, check an-
gle-of-attack adjustment location on each blade. All blades
should have the same angle as specifi ed for the unit. If
amp draw is still low, increase the setting for all fi ns by a
fraction of a degree and take new amp draw readings.
Possible Cause # 6: Inadequate Water Treatment
•
Check scale buildup on coil. Scale buildup 1/32" thick can
cause a 30% capacity reduction (as rated in cooling tons
per hour).
Possible Cause # 7:
Improperly Sized Or Applied Ancil-
lary Component Or System Piping
•
Check system piping against system designer’s plans and
specifi cations. Look for unusual mixed piping sizes/materi-
als, excessive vertical/horizontal distances, “add-on” fl ow
restricting devices, and poor quality pipe-fi tting and support
anchors.
Possible Cause # 8: IDC Unit Experiencing “Recircula-
tion” Due To Improper Siting
•
Recirculation of warm, moist exhaust air can rob up to
30% of the IDC unit’s cooling capacity. Since this is a
highly variable condition depending on weather conditions
and the operational timing of nearby cooling units, plant
maintenance is encouraged to consult with the cooling
system design engineer.
•
Generally speaking, an IDC unit should be located above
roof level, as far away as possible from other exhaust
stacks, and upwind of higher wind-diverting structures.
Any diversion from these rules-of-thumb should be re-
examined by the system design engineer.
Possible Cause # 9: Noncondensables In Receiver or
Condenser
•
Check condenser and receiver to determine if non-con-
densables have contaminated the system. If non-condens-
ables are found, proceed with repairs as prescribed by the
refrigeration equipment/system supplier (e.g., evacuating
the refrigerant lines/system and recharging after eliminat-
ing leak or source of contamination).
5.2 Condition: Excessive Deposits, Scale, Or
Turbidity
Possible Cause # 1: Inadequate Filtration Or Treatment
Of Spray Water
•
Filtration is an inherent requirement for evaporative cooling
systems due to the concentration of dissolved solids and
“washing” of air particulate. Recommended fi lters types
include bag, mesh, centrifugal, and sand & gravel.
•
Filtration equipment must be maintained regularly. All fi lters
(partial/side fl ow designs in particular) must be cleaned or
back-fl ushed regularly.
•
In the event that plant-cooling system seems to have
inadequate fi ltration, Imeco recommends that the system
design engineer consult with a local water treatment ex-
pert. Until the situation is resolved, blow-down rates should