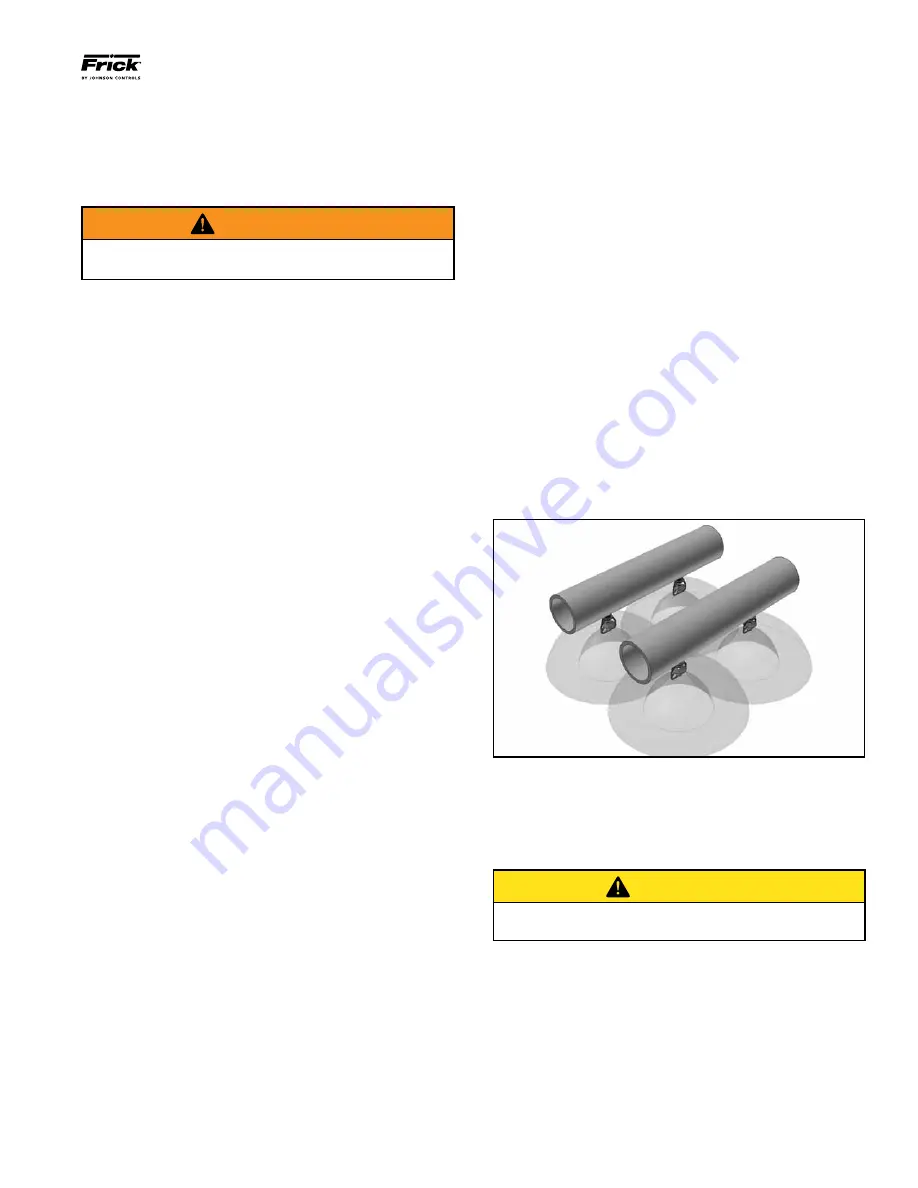
ECH EVAPORATIVE CONDENSERS
MAINTENANCE
140.910-IOM (DEC 13)
Page 17
Adjustable Motor Base
Coat the motor base slides and adjusting screws (see Figure
10 in the Operation section) every 3 months using good quality
corrosion inhibiting grease such as one of those recommended
for lubricating the fan shaft bearings below.
WARNING
Check to ensure the controls for the fan motor are set to
allow a maximum of 6 on-off cycles per hour.
FAN SHAFT BEARINGS
Two pillow block ball bearings support the fan shaft. Each bearing
is equipped with a lubrication fitting and a slinger/locking collar
to keep out moisture.
Inspection and Maintenance
•
Lubricate the bearings with only a manual grease gun. Do
not use high-pressure grease guns since they may rupture
the bearing seals.
•
Lubricate the bearings with only one of the following
compatible water resistant greases* which are suitable
for ambient temperatures ranging from -65°F (-53.9°C) to
+250°F (121.1°C).
Amoco-Rycon Premium#3
MobilGrease
®
-AW2
Chevron-SRI
Shell-Alvania RL3™
Citgo-Polyurea MP2™
Shell-Alvania #3
Conoco-Polyurea 2™
Shell-Dolium “R”
Exxon-Polyrex
®
EM
SKF-LGHP2™
Exxon-Unirex N™
Unocal76-Unilife Grease™
*NOTE: List of brand names is for identification only and are
not exclusive recommendations.
•
Lubricate the bearings as follows:
1.
Initial Start-up:
Normally, no lubrication is required
since the bearings have been lubricated at the factory
prior to shipment. However, if the unit has been stored
at the job site for more than 1 year, both bearings
should be lubricated with new grease before initial
operation.
When lubricating, purge the old grease
from the bearing by gradually adding grease until
a bead of new grease appears at the seal on the
underside of the bearing.
2.
Seasonal Start-up:
Purge both bearings with new
grease prior to start-up.
3.
Operation:
Purge bearings every 2,000 hours of
operation or once every 3 months, whichever occurs
first.
4.
Extended Shutdown:
Purge bearings with new grease
prior to any prolonged storage or downtime.
HEAT TRANSFER SECTION
Fill and Drift Eliminator
The ECH has PVC fill with integral drift eliminators.
Inspection and Maintenance:
•
Inspect and clean the fill with the integral eliminators at
least quarterly.
•
The inspection procedure is as follows:
1. Shut off the fan and the spray pump.
2. Inspect the fill for obstructions, damage and fouling.
•
Remove any obstructions from the fill.
•
Remove any minor fouling chemically. Contact your local
water treatment consultant for advice.
•
Major fouling requires cleaning and flushing. Follow the
procedures listed in the SYSTEM CLEANING section at the
end of the MAINTENANCE section.
WATER DISTRIBUTION SYSTEM
The water is distributed through a corrosion resistant polyvinyl
chloride (PVC) system. The fill and drift eliminators are also
made of PVC, which requires no protection against rot, decay,
rust, or biological attack.
Inspect and clean the spray nozzles and heat transfer section
each month.
The inspection procedure is as follows:
•
Shut off the fan, but leave the spray pump running.
•
Check to see if the nozzles are producing the spray pattern
shown in Figure 15.
Figure 15 - Nozzle Spray Pattern
•
Clean any nozzles which are clogged. If necessary, the
nozzle and rubber grommet may be removed for cleaning.
•
Inspect the coil surface. Any corrosion, damage, or
obstructions must be corrected.
CAUTION
Don’t use steam or high pressure water to clean PVC
eliminators or materials other than steel.
WATER LEVEL CONTROL
There are two types of water level controls used on Frick units:
•
Mechanical makeup valve assembly
•
Optional electric water level control package
The ECH water makeup valve assembly is located on the air
inlet face.