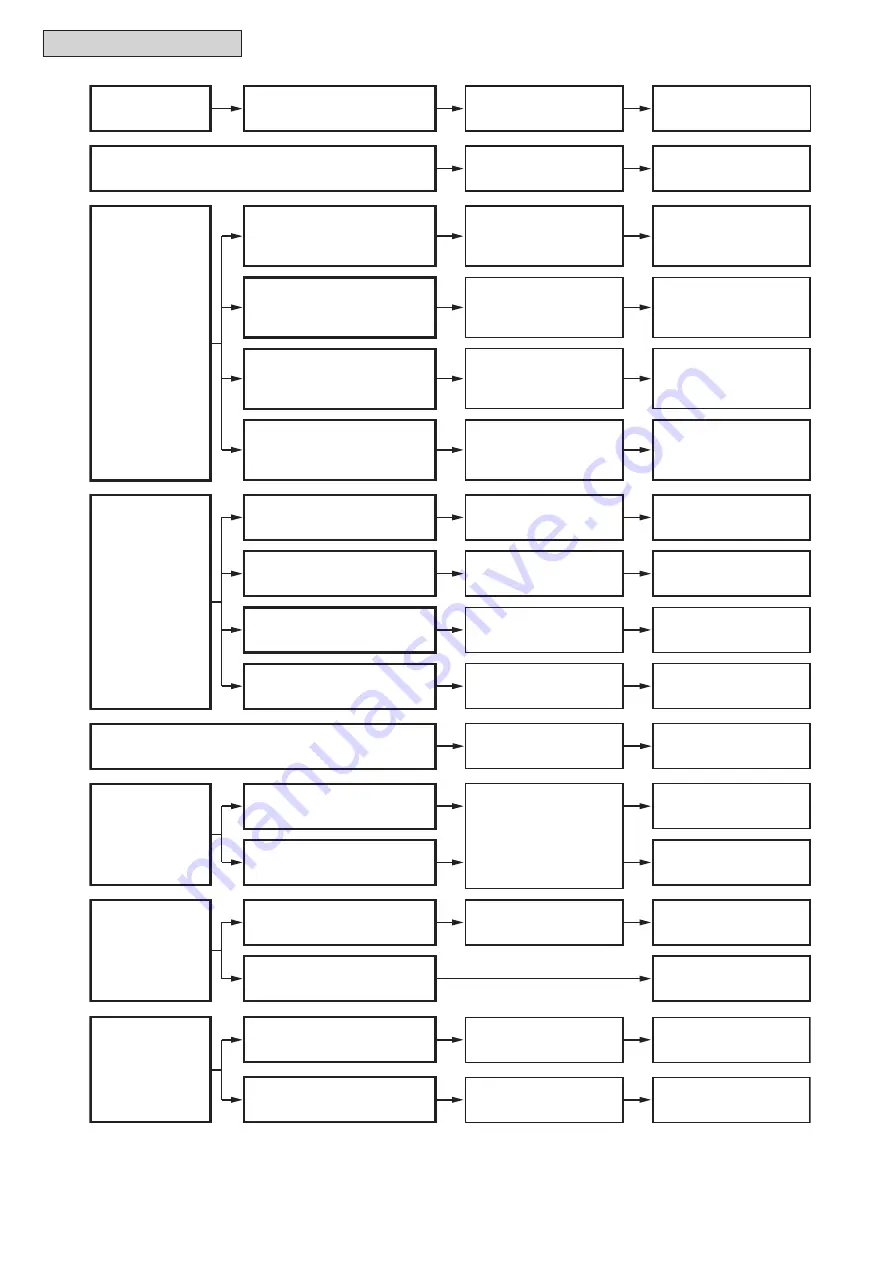
3-22
SM-18003
TROUBLESHOOTING
Correctly connect wires.
Check continuity
and looseness of
connection screws.
Check terminal Nos.
Incorrect Wiring
Disconnected Wire
Contact Failure
Incorrect Wiring
Replace or repair
wires, or tighten screws.
O.U. PCB: Outdoor Unit PCB
I.U. PCB: Indoor Unit PCB
Cause
Check Item
Action
(Turn OFF Main Switch)
Event
Blown Fuse for
Power Source
or Activation of
Breaker
Check for breakage
of insulation.
Short Circuit between Wires
Measure insulation
resistance.
Short Circuit to Ground
Measure voltage with
tester.
Supply power.
Power Failure or No Power Supply
Measure resistance
between wires and
insulation resistance.
Faulty Comp. Motor
Measure resistance
between wires and
insulation resistance.
Replace outdoor unit
fan motor and fuse.
Replace O.U. PCB
if faulty.
Faulty Outdoor Unit
Fan Motor
Blown Fuse
on PCB
(Outdoor Unit)
Check for breakage
of wire insulation.
Remove cause of
short circuit and
replace fuse.
Short Circuit between Wires
Measure insulation
resistance.
Remove cause of
short circuit and
replace fuse.
Short Circuit to Ground
Disconnected
Wires,
Contact Failure or
Incorrect
Connection
Check continuity of
wires.
Check for looseness
of connection screws.
Check terminal Nos.
Replace and repair
wires, tighten screws
or correct wires.
Between Outdoor Unit
and Indoor Unit
Power Source Wiring
for Outdoor Unit
Measure resistance
of coil.
Replace magnetic
switch (CMC) and fuse.
Faulty Solenoid Coil for
Magnetic Switch (CMC)
for Comp. Motor
Measure resistance
between wires and
insulation resistance.
Replace fan motor
and fuse.
Faulty Outdoor Unit
Fan Motor
Correctly connect wires.
Replace it if faulty.
PCB Failure
(Outdoor Unit,
Indoor Unit)
Check connection.
Disconnected Wires to
I.U./O.U. PCB
Faulty I.U./O.U.PCB
Remove cause of
short circuit.
Replace fuse and/or
I.U./O.U. PCB if faulty.
Remove cause of
short circuit to ground.
Replace fuse and/or
I.U./O.U. PCB if faulty.
Replace comp. and
fuse. (O.U.) Replace
inverter PCB and/or
PCB if faulty. (O.U.)
Correctly connect wires.
Measure O.U. PCB
output.
2
Replace O.U. PCB.
Incorrect Power Supply Circuit of O.U. PCB
(Outdoor Unit and
Change-Over Box)
Содержание CICM008B21S
Страница 2: ......
Страница 10: ...viii SM 18003 ...
Страница 15: ...SM 18003 1 1 INSTALLATION 1 Installation ...
Страница 19: ...SM 18003 2 1 OPERATION 2 Operation ...
Страница 20: ...2 2 SM 18003 OPERATION 2 1 Indoor Unit Refer to the Operation Manual for Mini Cassette ...
Страница 22: ......
Страница 23: ...SM 18003 3 1 TROUBLESHOOTING 3 Troubleshooting ...
Страница 73: ...MAINTENANCE SM 18003 4 1 4 Maintenance ...
Страница 74: ...MAINTENANCE 4 2 SM 18003 4 1 Maintenance of Outdoor Unit Refer to the Service Manual for Outdoor Unit ...
Страница 99: ...SM 18003 5 1 EXTERNAL INPUT OUTPUT AND FUNCTION SETTING 5 External Input Output and Function Setting ...
Страница 138: ......
Страница 139: ...SM 18003 6 1 FIELD WORK INSTRUCTIONS 6 Field Work Instructions ...
Страница 148: ...6 10 SM 18003 FIELD WORK INSTRUCTIONS 6 8 Mollier Chart for R410A f t 3 l b ...
Страница 149: ...SERVICE PARTS LIST SM 18003 7 1 7 Service Parts List ...
Страница 150: ...SERVICE PARTS LIST 7 2 SM 18003 Refer to the Service Parts List for Mini Cassette ...
Страница 151: ......
Страница 152: ... 2018 Johnson Controls Inc SM 18003 Code No LIT 12013034 Issued April 2018 ...