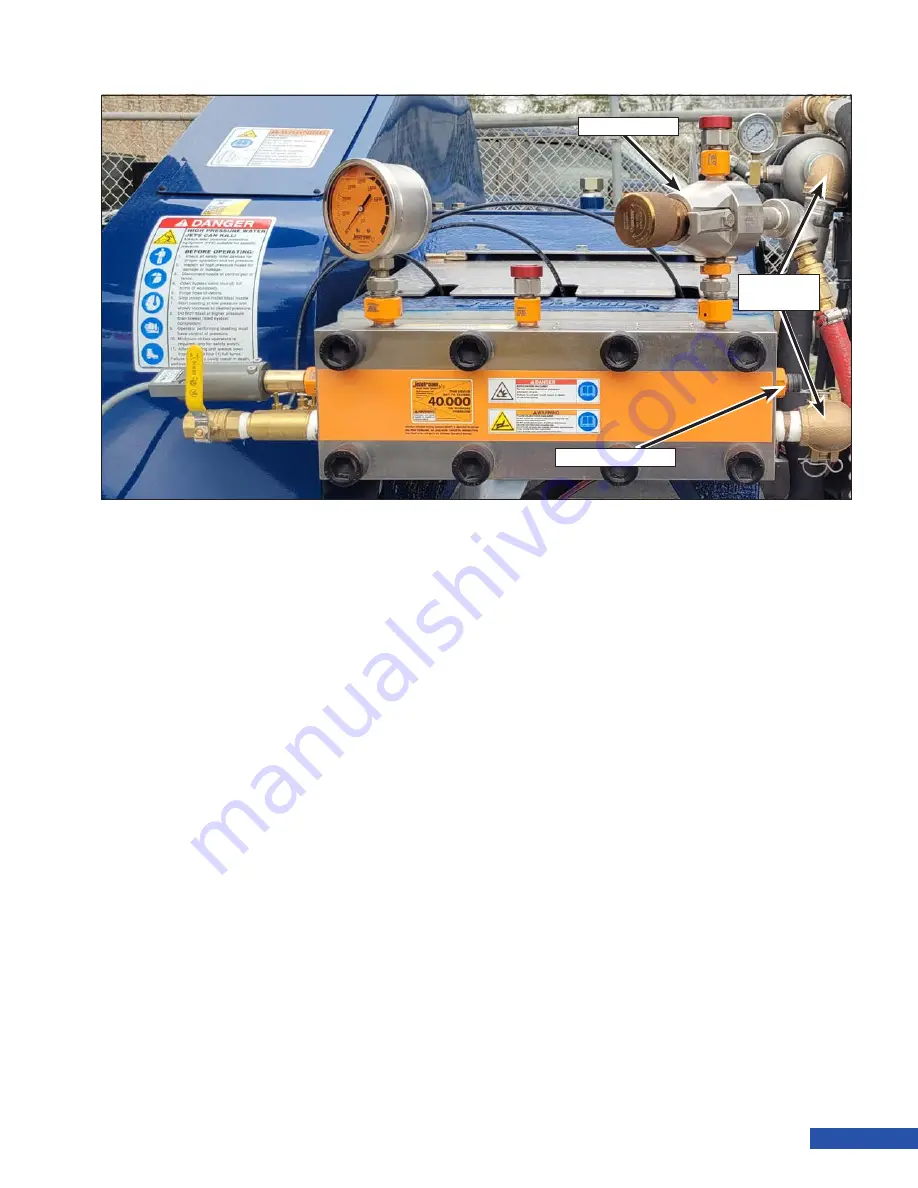
9
TwinForce™ Series Waterblast Unit
Hydro-Throttle Switch (Optional)
The hydro-throttle switch senses the pressure
within the pump and allows the engine to idle
when the operator is not blasting.
Refer to
“Using the Hydro-Throttle (Dump Sys
Rupture Discs
Two rupture discs are used in the system. The
rupture discs provide protection from excess
pressure in the system. If system pressure
were to exceed the rated pressure of the discs,
the discs would burst. If a disc bursts, water
will flow through the ruptured disc to provide
relief for the system and protect components
from excess pressure. Check the discs before
operating the pump. Keep a supply of rupture
discs on hand for use. If a rupture disc should
burst, there is no way to build pressure until
the disc is replaced. Use only genuine Jet-
stream rupture discs properly rated for the
intended operating pressure.
Bypass Valve
The bypass valve controls the pump pressure
by bleeding off excess water and diffusing it to
low pressure. Turning the knob allows the op-
erator to adjust pressure during operation and
relieve pressure when not waterblasting.
The bypass valve controls pressure by allowing
water to bypass though the valve. A discharge
hose is attached to the bypass valve. The hose
extends to the other side of the unit where it is
attached to a drain elbow. Water that bypasses
the valve will drain from the bypass drain
throughout operation.
The proper use of the bypass valve is to install
the correct size nozzle in the system so that
the bypass valve can be closed during opera-
tion. A combination of plunger size, engine
rpm, and nozzle will allow the bypass valve to
close at almost all flow rates.
Note:
For units employing a shut in sys-
tem, a regulator valve is substi-
tuted for a bypass valve.
Regulator Valve (Not Shown)
For shut-in systems (where no low pressure
water dumps from the gun), the bypass valve
is replaced with a regulator valve. The regu-
lator maintains constant system pressure
Discharge Fitting
Supply
Couplings
Bypass Valve
Figure 11: Pump Components (continued)
Содержание TwinForce Series
Страница 1: ...OPERATION MANUAL TwinForce Series Waterblast Unit...
Страница 2: ...Visual Safety System...
Страница 11: ...3 TwinForce Series Waterblast Unit...
Страница 22: ...14 Operation Manual...
Страница 42: ...34 Operation Manual...
Страница 48: ...40 Operation Manual...
Страница 52: ...44 Operation Manual...
Страница 100: ...92 Operation Manual...
Страница 104: ...96 Operation Manual...
Страница 106: ...A 2 Appendix A Technical Specifications...
Страница 107: ...B 1 TwinForce Series Waterblast Unit APPENDIX B LONG TERM STORAGE PROCEDURE...
Страница 108: ...B 2 Appendix B Long Term Storage Procedure...