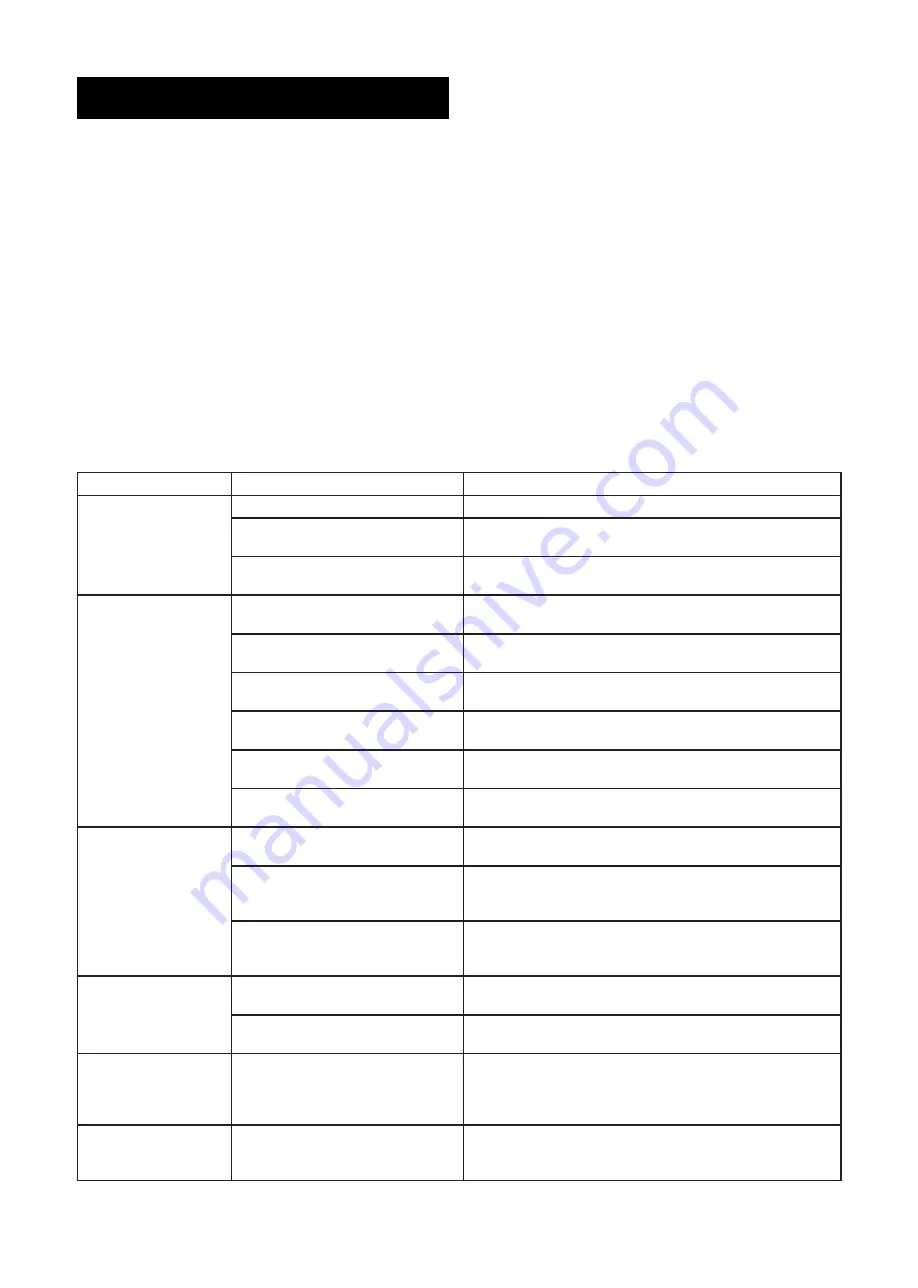
17
Important
•
After servicing, complete the relevant Service
Interval Record section of the Benchmark
Checklist located on pages 20 and 21 of this
document.
•
Servicing should only be carried out by competent
persons in the installation and maintenance of
unvented water heating systems.
•
Any spare parts used MUST be authorised parts.
•
Disconnect the electrical supply before removing
any electrical equipment covers.
•
NEVER bypass any thermal controls or operate
system without the necessary safety valves.
•
Water contained in the cylinder may be very hot,
especially following a thermal control failure.
Caution must be taken when drawing water from
the unit.
Spare Parts
A full range of spare parts are available for the
cylinder range (Table 05, page 18). Refer to the
technical data label on the unit to identify the model
installed and ensure the correct part is ordered. You
will need to quote the serial number, which is printed
on the data label.
Fault Finding
The fault finding chart (Table 04, below) will enable
operational faults to be identified and their possible
causes rectified. Any work carried out on the
unvented water heater and its associated controls
MUST be carried out by a competent installer for
unvented water heating systems. In case of doubt
contact
service support (see contact details on back
page).
Warning
DO NOT TAMPER WITH ANY OF THE SAFETY
VALVES OR CONTROLS SUPPLIED WITH THE
CYLINDER AS THIS WILL INVALIDATE ANY
GUARANTEE.
Fault Finding & Servicing
Fault
Possible cause
Remedy
No hot water
1. Mains water supply off.
1. Check and open stop cock.
2. Strainer blocked.
2. Turn off water supply. Remove strainer and clean (
see page 31).
3. Cold water combination valve
incorrectly fitted.
3. Check and refit as required.
Water from hot taps
is cold
1. Back up immersion heater not
switched on.
1. Check and switch on.
2. Back up immersion heater
thermal cut-out has tripped.
2. Check. Reset by pushing button (Figure 10, page 14).
3. Indirect programmer set to
central heating only.
3. Check. Set domestic to a hot water programme.
4. Indirect boiler not working.
4. Check boiler operation. If fault is suspected consult
boiler manufacturers instructions.
5. Indirect thermal cut-out has
tripped.
5. Check. Reset by pushing button. Check operation of
indirect thermostat (Figure 10, page 14).
6. Indirect motorised valve not
connected correctly.
6. Check wiring and/or plumbing connections to
motorised valve (see Figures 8 & 9, page 13).
Water discharges
from expansion relief
valve
1. Intermittently. Air volume in the
cylinder has reduced
1. See page 16 for details on how to test and recharge.
2. Continually. 3 bar pressure
reducing valve is not working
correctly.
2. Check pressure from 3 bar pressure reducing
valve. If greater than 3 bar replace pressure reducing
cartridge.
3. Continually. Expansion valve
seat damaged.
3. Remove expansion relief cartridge from 8 bar
pressure relief valve and check seating, if necessary fit
new cartridge.
Water discharges
from the T&P valve
intermittently
1. Air volume in the cylinder has
reduced
1. See page 16 for details on how to test and recharge.
2. 8 bar expansion relief valve
faulty.
2. Check valve and replace if necessary
Water discharges
from the T&P valve
continually
1. Thermal control failure. Note
water will be very hot.
1. Switch off power supply to immersion heater(s) and
shut down the boiler. DO NOT turn off the water supply.
When discharge stops check all thermal controls,
replace if faulty.
Milky water
1 Oxygenated water.
1. Water from a pressurised system releases oxygen
bubbles when flowing. The milkiness will disappear
after a short while.
Table 04: Fault Finding Chart
Содержание 120i
Страница 22: ...22 Notes...
Страница 23: ...23 Notes...