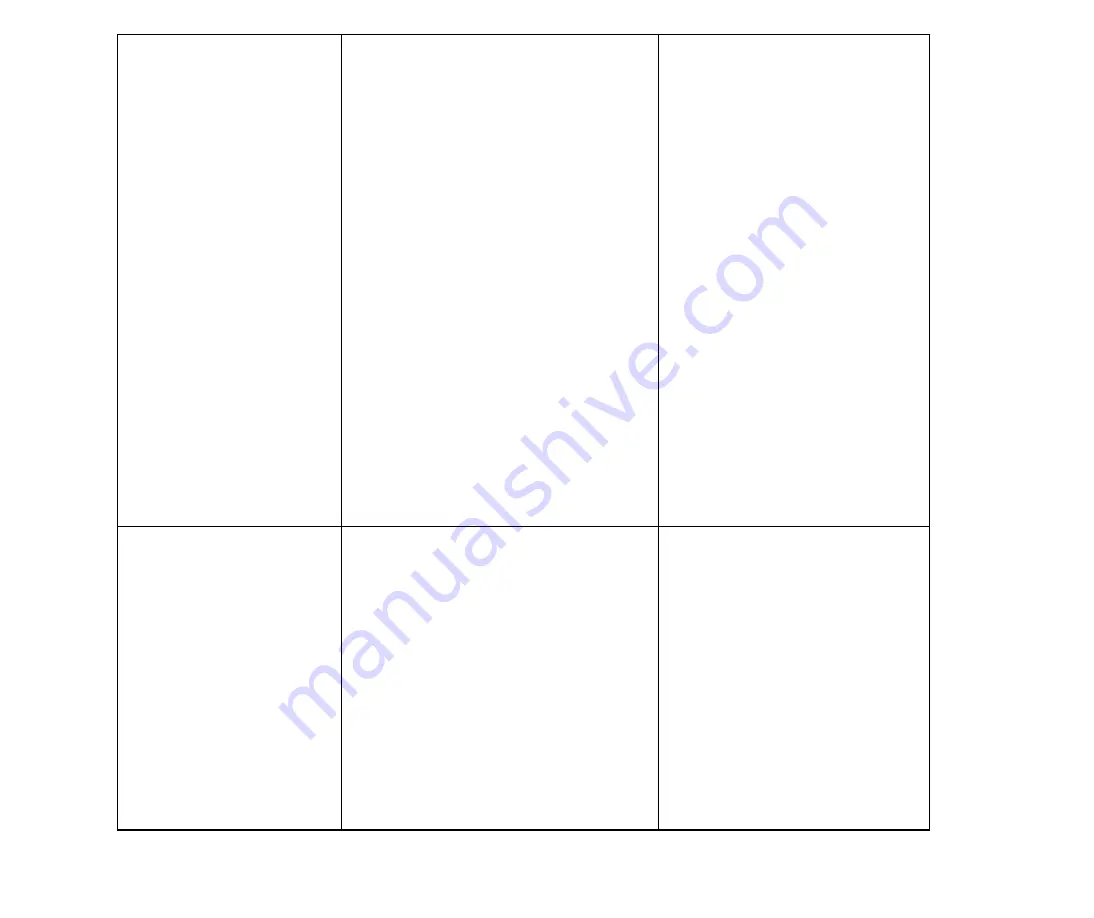
6. Turn on the machine and it
appears normal, it can start arc
in TIG mode, but the welding
point appears black.
a. The magnet valve or the gas tube is
blocked.
b. The magnet valve is damaged.
c. The connecting cable matching socket
CON3 on HF PCB PZ-35-A0 with socket
CON7 on control panel PK-31-A0 is in
loose connection.
d. Some part in the magnet valve control
circuit on HF PCB PZ-35-A0 or on control
panel PK-31-A0 is damaged.
e. The welding torch is damaged.
f. The tungsten is of bad quality or the
argon is impure.
a. Clear.
b. Replace.
c. Check.
d. Check with a multi-meter if
MOSFET VT2, diode D6, zener
diode Z1 on HF PCB or audion Q1
on control PCB PK-31-A0 is
damaged or if the magnet valve
control cable matching the socket
CON2 is disconnected.
e. Remove the welding torch and the
gas-electricity tie-in, and press the
welding torch switch. If there is
gas out, the welding torch is
damaged. Replace it.
f.
Replace them if necessary.
7. The welding current is
unstable and out of control.
a. The connecting cable matching socket
CON2 on control PCB PK-05-A4 with
socket CON11 on control panel
PK-31-A0 is in loose connection.
b. The capacitor C1/C2/C3/C4/C5/C6 on
bottom PCB PZ-03-B0 leaks or is
damaged.
c.
The input cable or output cable is too slim
and too long.
d. Loose connection exists inside the
machine, e.g. the connecting cable
matching socket CON4 on control panel
with the remote control.
a. Check and replace it if necessary.
b. Check and replace it if necessary.
c. Enlarge the cross section area of
the cable.
d. Check.