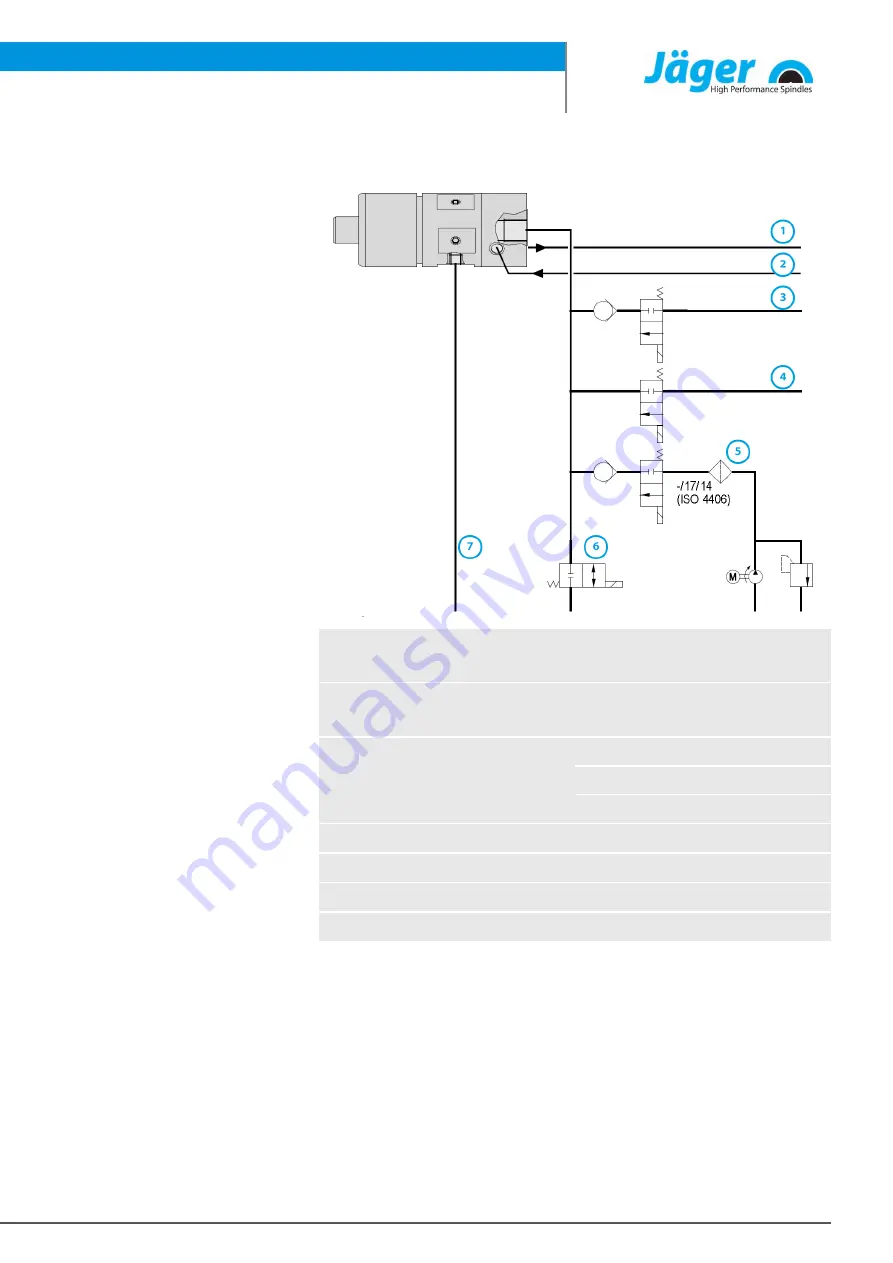
Installation
Item no. 10408017, Revision 05
35 ( 52 )
8.5
Setting the internal coolant supply
1
Internal cooling (as required)
M5
Max. 10 bar
2
Internal cooling (as required)
M5
Max. 10 bar
3
Compressed air
At 0 rpm
10 bar
Up to 10,000 rpm
5 bar
Above 10,000 rpm
No pressure
4
Minimum quantity cooling lubrication
Max. 5 bar
5
Cooling lubricant
Max. 80 bar
6
Vent
G1/8"
7
Leakage
5 x M5
Ü
Keep lines short.
Ü
Do not exceed the pressures specified above.
Ü
Avoid pressure pulsation.
Ä
Max. ±5 bar.
Ü
Avoid pressure peaks.
Low-pulsation delivery of media (±2 bar) by the pump increases the service
life of the cooling lubricant system components and reduces the noise level.