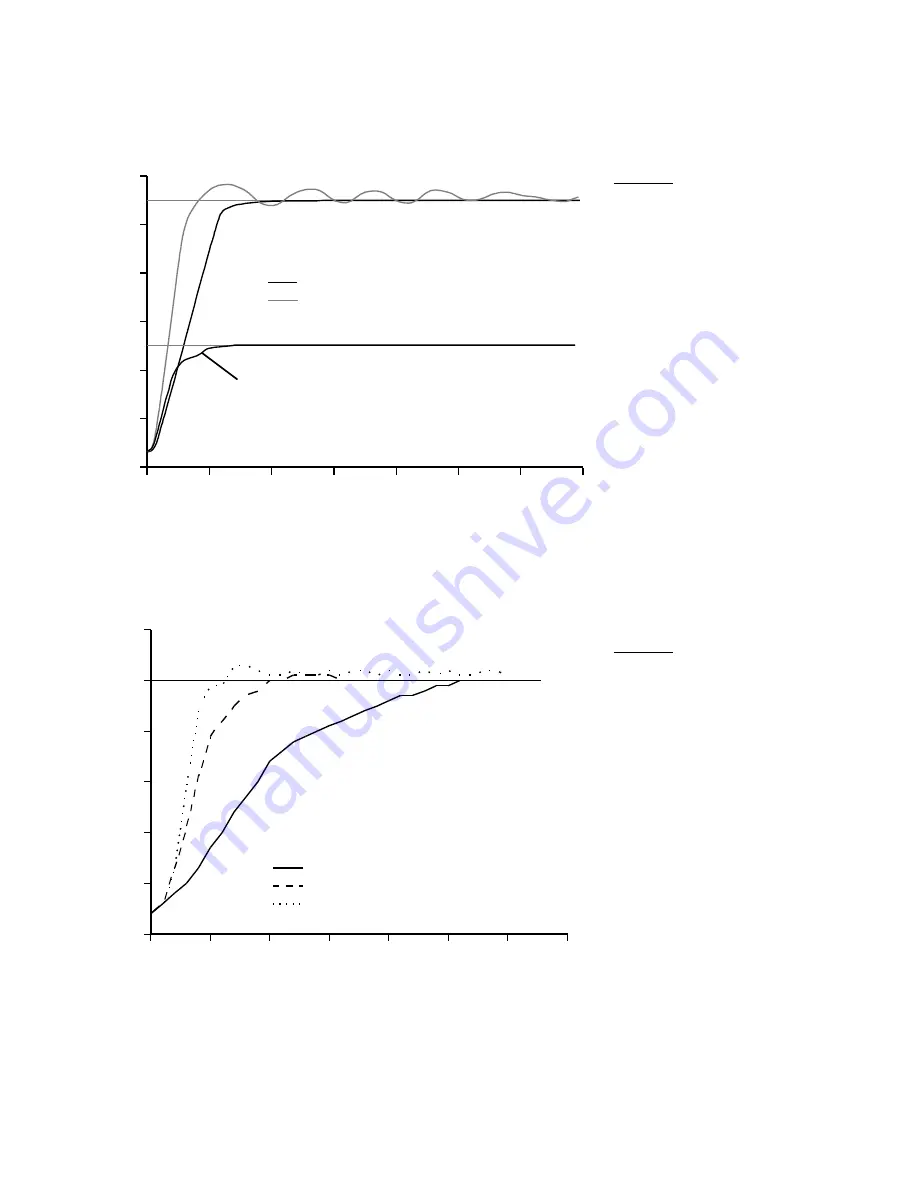
3.7
Affect of Power Setting on Heating Profile. The following graphs show the effect of selected power
levels on heating performance in a variety of situations. Each example contains 1 optimal and 1 or 2 less
optimal settings demonstrating use of the power reduction circuit.
0
10
20
30
40
50
60
70
20
30
40
50
60
70
80
Conditions: Set point = 75 C
Laboratory oven
o
Power Setting = 50 - 500 ml
Power Setting = > 2L
Conditions: Set point = 45 C
HPLC Column wrapped with heating tape
Power Setting = 50 - 500 ml
o
Temp
C
o
Time (min)
2 0
3 0
4 0
5 0
6 0
7 0
8 0
0
1 0
20
3 0
40
5 0
6 0
7 0
Temp.
o
C
Time (min)
Power Setting = 10-100 ml (i.e., 10% power)
Power Setting = 50-500 ml (i.e., 25% power)
Power Setting = 300 ml - 2 L (i.e., 50% power)
Conditions: Set point = 70
o
C
50 ml Toluene
100 ml Round bottomed flask
Graph 1
This graph shows typical
heating profiles for a laboratory
oven and an HPLC column. In
the example of the oven the
heating curves for 2 different
power levels are shown. The
50 - 500 ml setting is the
appropriate amount of power to
heat to 75
o
C and thus results in
a smooth heating curve. The
> 2L power setting is too much
power and results in oscillation
around the set point.
Graph 2
This graph shows the affect of
different power settings when
heating liquids with heating
mantles. The 10 - 100 ml
setting (10% power) is under
powered and results in slow
heating. The 300 ml - 2 L
setting (50% power) is too much
power and results in sporadic
control. The controller adapts
to a wide range of power
settings. In this example the
power is varied by a factor of
5X, nevertheless, reasonable
control is maintained in each
case.
16