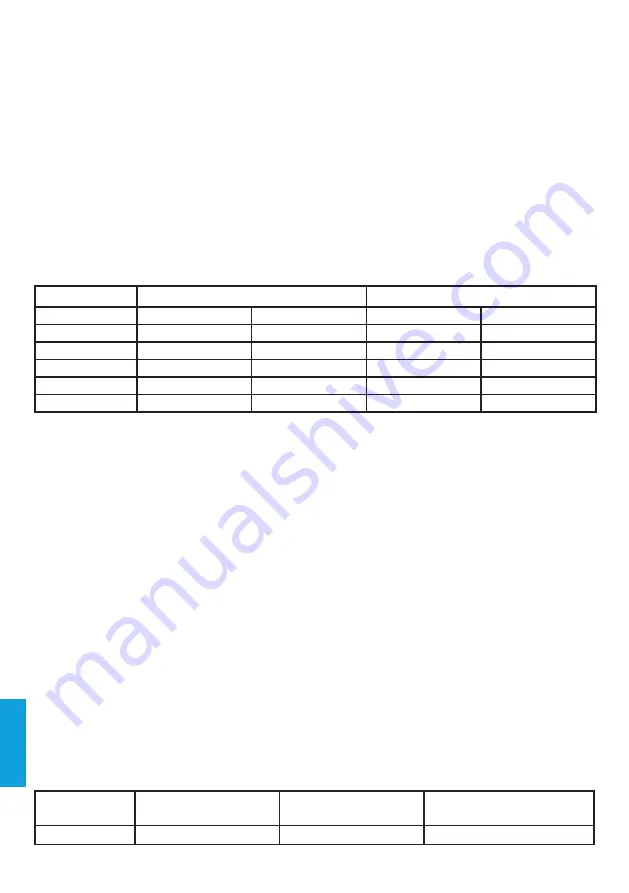
EN
4. Operation instructions
1. Turn the machine “ON” using the main power switch. Open the valve of the gas bottle
and adjust the gas flow on the pressure regulator.
2. Select the diameter of MIG torch nozzle according to the welding wire diameter. Set
up the parameters the welding mode and the cooling mode.
- If you choose MMA welding mode(with or without VRD function) adjust the MMA weld
-
ing parameters .
- If you choose TIG welding mode, adjust the TIG welding parameters.
- If you choose MIG/MAG welding mode, adjust the welding parameters on the control
panel of wire feeder.
3. According to thickness and process of workpiece, adjust the voltage and the current.
Select the “synergy” or “manual” function by pressing the “K” button on the control
panel of wire feeder.
4. Inductance adjustment can change the ARC strenght.
5. Begin to weld by pressing.
Wireφ(mm)
Short circuit transition
Granular transition
Current(A)
Voltage (V)
Current(A)
Voltage (V)
0.6
40~70
17~19
160~400
25~38
0.8
60~100
18~19
200~500
26~40
1.0
80~120
18~21
200~600
27~40
1.2
100~150
19~23
300~700
80~120
1.6
140~200
20~24
500~800
32~44
Welding
mode
Thin wire
C0
2
welding
Thick wire
C0
2
welding
Thick wire, big current
C0
2
welding
C0
2
(l/min)
5-15
15-25
25-50
4.1 Setting the welding current
The selection of welding current ,voltage and ARC will influence the stability, welding
quality and the productivity during the welding process. In order to keep a good weld
-
ing quality, the welding current should match the voltage and the ARC well. Select the
wire diameter according to the globular transfer and the production requirement.
Refer to the below list, choose the common welding current, ARC and voltage.
-The option of the welding speed
The welding quality and productivity should be taken into consideration for the option
of welding speed. In case that the welding speed increases, it weakens the protection
efficiency and speeds up the cooling process. As a consequence, it is not optimal for
the seaming. In the event that the speed is too slow, the work piece will be easily dam
-
aged, and the seaming is not ideal. In practical operation, the welding speed should
not exceed 30m/hour.
-The length of wire stretching out
The length of wire stretching out the nozzle should be appropriate. The increase of the
length of wire stretching out of the nozzle can improve the productivity, but if it is too
long, excessive spatter will occur in the welding process. Generally, the length of wire
stretching out the nozzle should be 10 times as the welding wire diameter.
-The setting of the C0
2
flow volume
The protection efficiency is the primary consideration. Besides, inner-angle welding has
better protection efficiency than external-angel welding. For the main parameter, refer
to the following figure.
25
24
Содержание MIG 520 COOLPULSE
Страница 14: ...HU 14...
Страница 16: ...EN INDEX INTRODUCTION 3 MAIN PARAMETERS 4 WARNING 5 INSTALLATION 6 7 OPERATION 8 12 CAUTIONS MAINTENANCE 13 16...
Страница 28: ......
Страница 31: ......
Страница 32: ...www iweld hu...