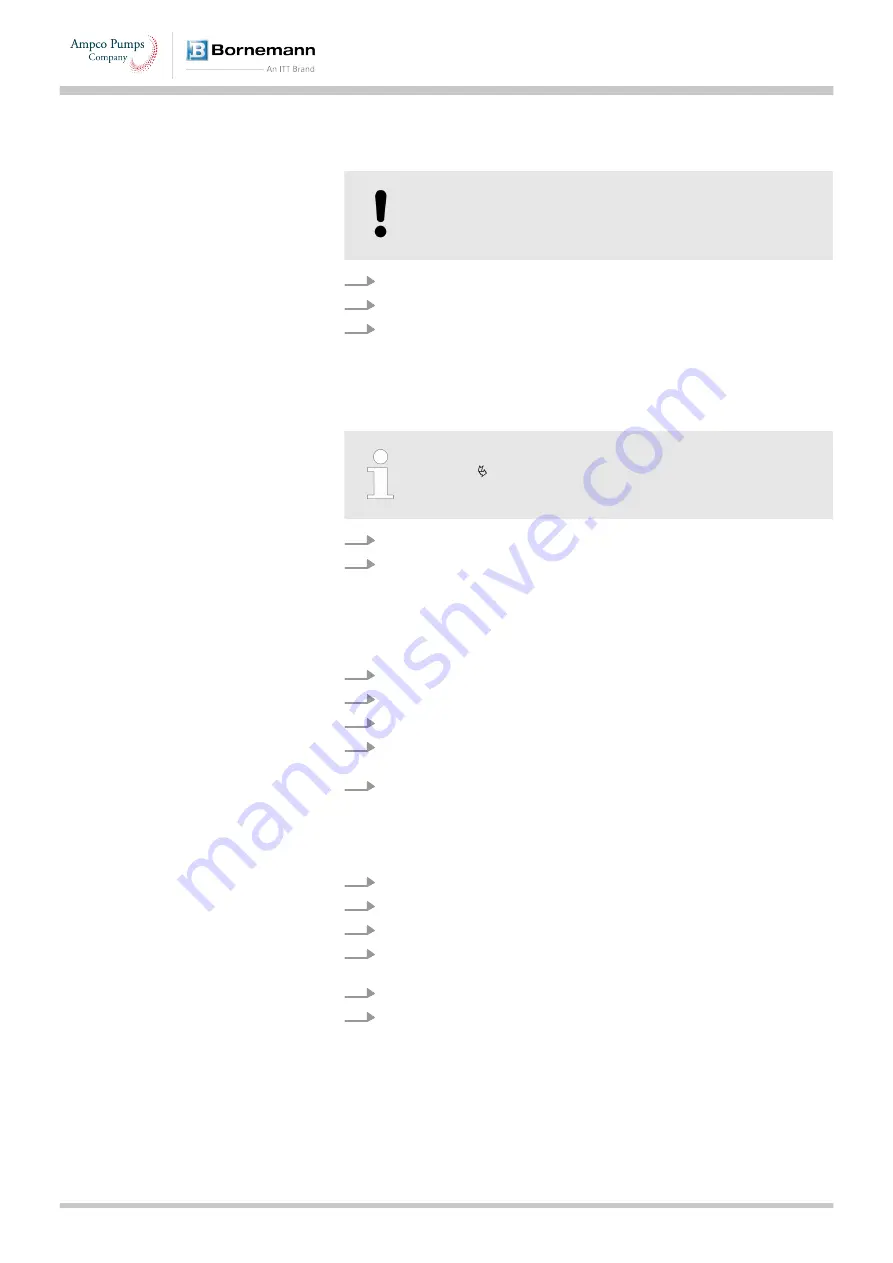
5.7.1 Avoiding contamination of the pipes
NOTICE!
Property damage resulting from pump contamination!
–
Ensure that no contaminants enter the pump.
1.
Prior to assembly, clean all pipe sections and valves.
2.
Ensure that flange seals do not protrude inwards.
3.
Remove blank flanges, plugs, protective film and/or protective paint on the
flanges.
5.7.2 Installing auxiliary pipes
Observe the manufacturer's instructions of any auxiliary operating
systems (
manufacturer's documentation).
1.
Install auxiliary pipes such that these are tension-free and leak-tight.
2.
Avoid air pocket formation: always lay lines such that these rise or fall
towards the pump.
5.7.3 Installing the inlet line
1.
Remove the transport locks from the pump.
2.
Install inlet line.
3.
Ensure that the flange seals do not protrude.
4.
Attach connection for filling the pump. When doing so, ensure that the con-
nection sizes account for the viscosity of the pumped medium.
5.
Check inlet line for correct direction of flow.
5.7.4 Installing the outlet line
1.
Remove the transport locks from the pump.
2.
Install outlet line.
3.
Ensure that the flange seals do not protrude inwards.
4.
If no pressure safety valve is included in the system: incorporate suitable
absolute pressure limiting into the system.
5.
Check outlet line for correct direction of flow.
6.
Equip outlet line with non-return protection (note installation direction).
5.7.5 Checking that the pipe connection is tension free
n
Pipe installed and cooled.
Prerequisite
Installation and connection
43
Type SLH-4U
0
3
/20
20
JP Rev. 1