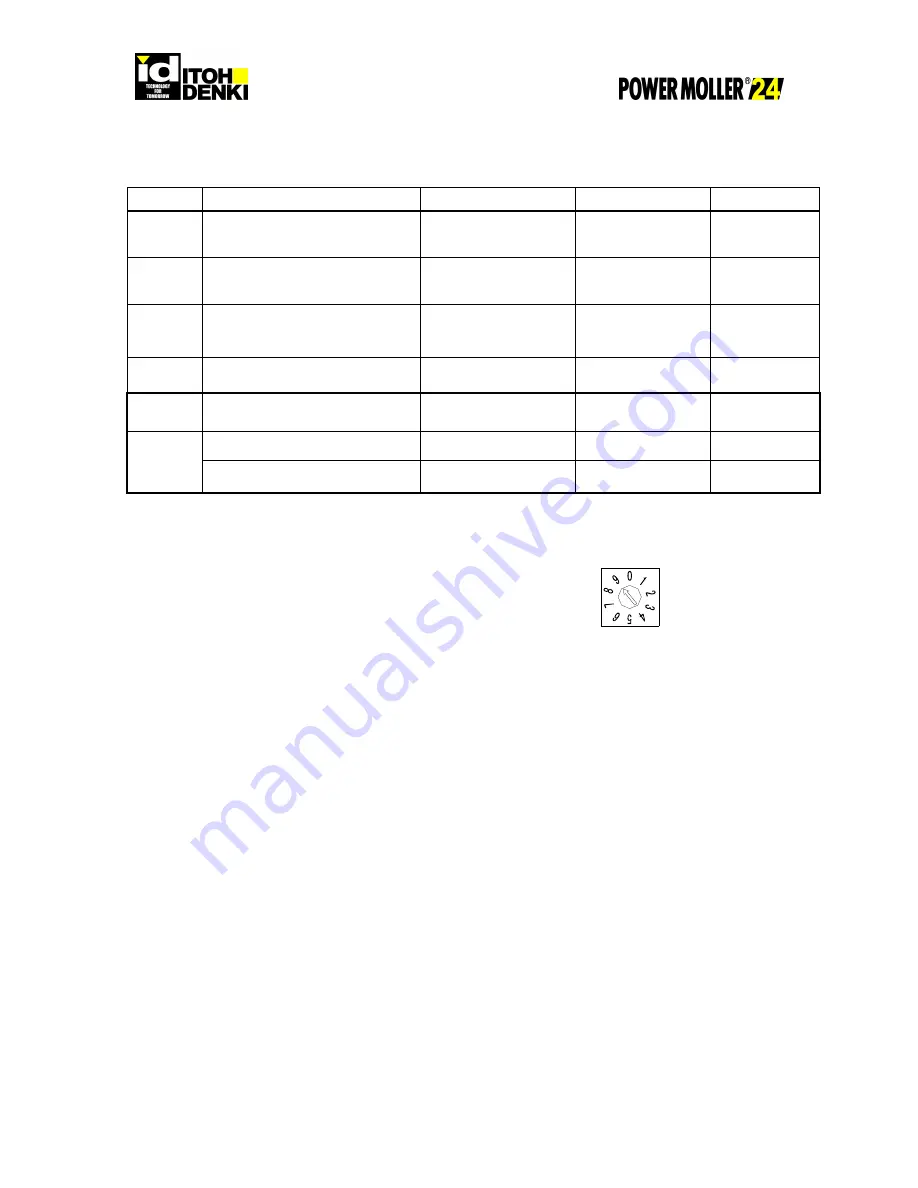
SPECIFICATIONS SUBJECT TO CHANGE WITHOUT NOTICE
Page 5 of 11
www.itohdenki.com
ITOH DENKI, USA, INC.
135 Stewart Road
Ph: 570.820.8811
Hanover Industrial Estates
Fx: 570.820.8838
Hanover Township, PA 18706
rev13-0314
OPERATION
DIP Switches (SW1) – User Settings
DIP-SW
Function
ON setting
OFF setting
Initial setting
1
Thermal device / low voltage /
back EMF recovery
Manual
Automatic
(Thermal restarts
1min after cool down)
ON
2
Speed change selection
External
(0~10V DC applied)
Internal
(Rotary switch)
OFF
3
DIR*
(no external DIR signal;
viewed from cable side)
FS/FP – CCW
FE – CW
FS/FP – CW
FE – CCW
OFF
4
Error signal activity
Active during normal
status
Active during
abnormal status
ON
5
Brake mode
Servo
Dynamic
OFF
Error output (FN type)
PNP
NPN
OFF
6
Error output (FP type)
PNP
NPN
ON
*External direction signal only - If a direction change signal should occur while the motor is
running, the motor will first stop for 0.5s. Then, the motor will start in the new direction.
Rotary switch (SW2)
Applicable when using internal speed control (DIP-SW2 OFF)
Factory default position 9 (highest speed)
Potentiometers*
VR1 – Acceleration
Adjust acceleration time from 0~2.5s after the RUN signal is applied
VR2 – Deceleration
Adjust deceleration time from 0~2.5s after the RUN signal is removed
* VRs turn 270°
Brake
Servo Brake mode with DIP-SW 1-5 ON
-
Holds Power Moller in position 0.2s after the RUN signal is removed
-
If external force moves the Power Moller it will return back to its initial stopped position
-
Maximum holding force is 17.7 lb-in at 1.0 A (Based on a PM486FE-60)
-
Servo brake does not function during an error condition
Motor pulse output signal
- NPN (0V) output from CN2-5
- Two (2) pulses per motor revolution