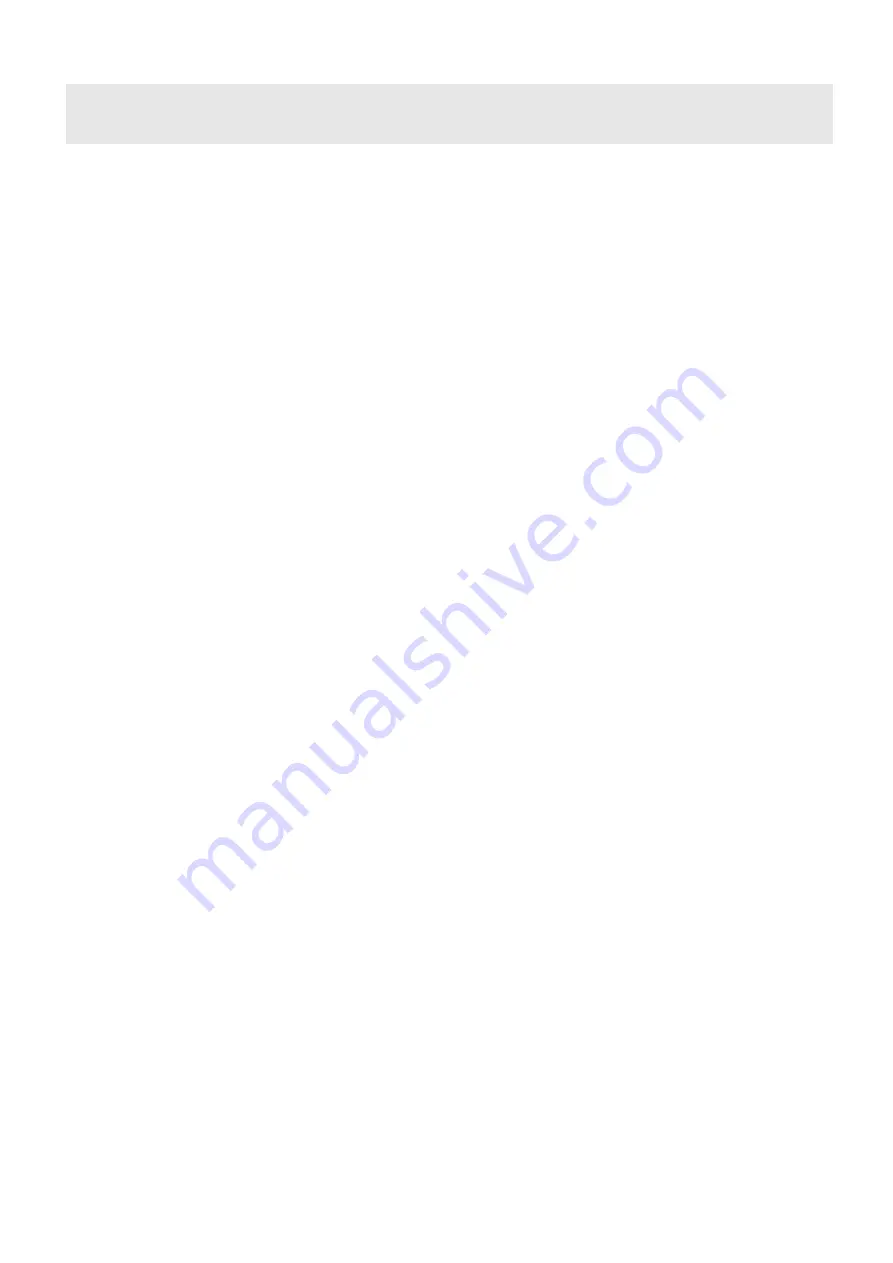
13
Maintenance
End Cap and Lubricating Systems are essential in order to protect and lubricate
the Bearing Units. These should be fitted back in place only when the guide
carriage has been mounted on the Shafts. Otherwise, it is important to ensure
the movable wipers are pressed back when sliding the guide carriage onto the
Shaft, to ensure they are not bent. Wipers located in the internal recesses of
the end-face End Cap and Lubricating Systems are also designed to take up the
lubricant. They are pressed against the guiding Shaft by a spring. These wipers
are supplied pre-charged with lubricant and can be topped up with lubricant
as required via the hole in the cap. In the event of considerable soiling, you
may need to replace the wipers. Suitable for use in dry conditions and over the
temperature range -20°C to +70°C.
If operating conditions are unusual - e.g. special type of installation, dust, short
stroke, influence of solvents etc. the lubrication intervals must be adapted
accordingly.
This information does not discharge the user from the obligation to carry out his
own assessments and checks.
It is important to bear in mind that our products are subject to a natural process
of wear and ageing.
The rollers of the guide are maintenance-free. The spring-loaded end cap and
lubricating felts can be topped up with lubricant as required via a hole.
Recommended re-oiling period: Every 6 months or every 2500 km. The felt
pieces are supplied in ready-oiled condition.
Synthetic lubrication oil ISO VG 460, e.g. item Track Oil for Linear Guides
(0.0.612.75).
Add the following quantity to each maintenance hole at the end of each mainte-
nance interval: 2 ml
Greases containing solid particles (e.g. graphite and MoS2 additives) must not
be used!
Oil Can for Linear Guides (one actuation delivers approx. 1 ml of oil).
To ensure adequate lubrication, the carriage must cover a minimum travel
distance. Minimum stroke length [mm]: 320 mm
Maintenance work needs to be carried out at regular intervals to ensure a chain
drive continues to run smoothly:
1. Lubrication
Once installation is complete, lubricate the Chain. Either oil or grease-based
lubricant can be used, as appropriate to the circumferential speed of the Chain
in the Chain Reverse Units, environmental requirements and the anticipated
loads. It is important to note that transported goods can also come into contact
with the lubricant, particularly when using the system as a transfer chain.
Lubrication must be checked regularly in line with the use of the Chain. It must
not be allowed to run dry under any circumstances.
2. Chain tension and backlash
Chains are traction devices that cannot be reversed without backlash. The
correct chain backlash can be set using the Chain Tensioning Blocks of the
Reverse Units, or by moving the Adapter Plate of the Chain Counter-Reverse
Unit. The tension on the Chain will need to be readjusted after a running-in
time of around 100 hours. The backlash on the Chain should be checked and
corrected at regular intervals, e.g. after lubricating.
3. Chain elongation and wear
Over long periods of use, the links in the Chain become elongated and
articulated surfaces are worn down by friction. When an overall elongation of
3% is reached, the Chain is worn-out and must be replaced. When replacing
the Chain, check for wear on the drive sprocket wheel and, if appropriate,
the sprocket wheels of any chain-driven conveyor rollers. Any visible trace of
erosion on the edges of the teeth is an indication that these drive components
also need to be replaced.
Ideal operating conditions:
Ambient temperature: 10°C ... 40°C
Load:
< 5%