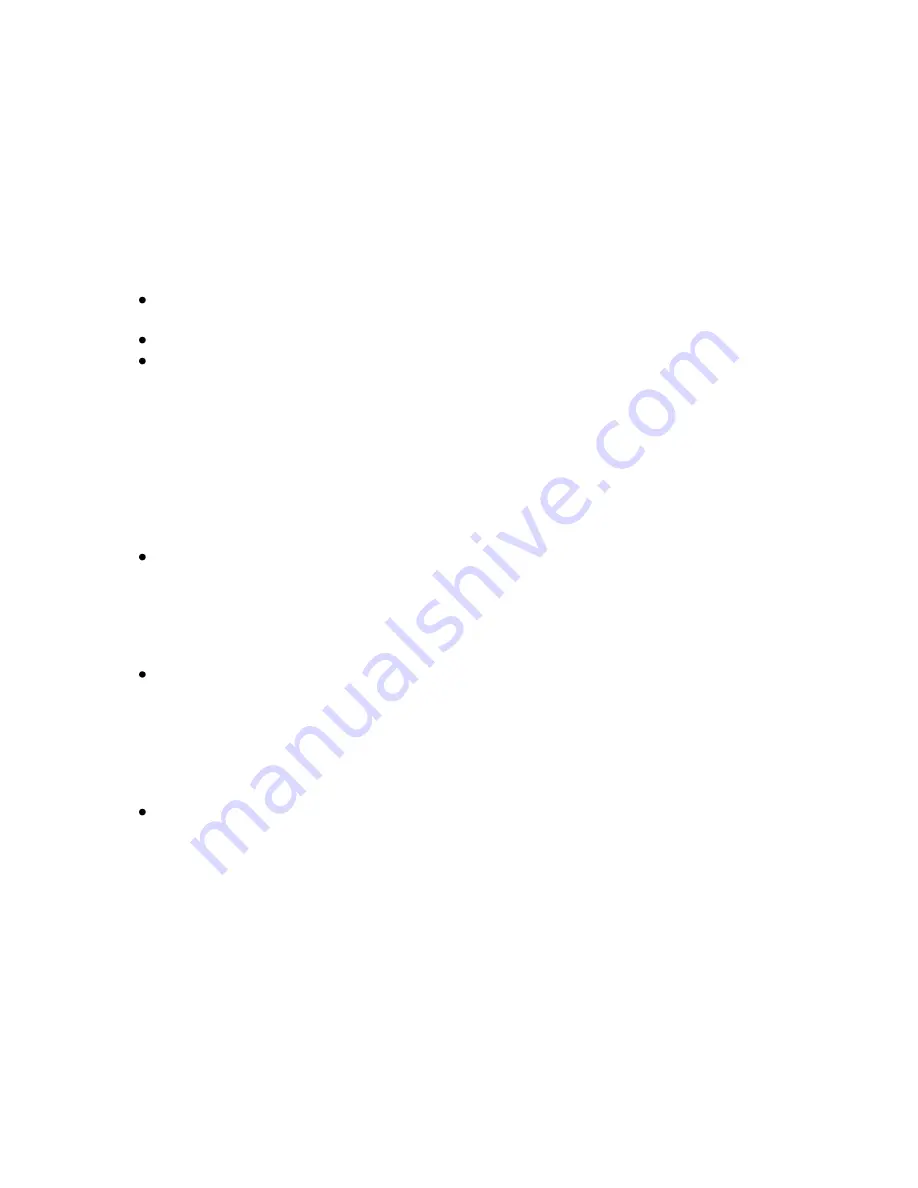
isel
- CAN - I/O
– Modules: Operating Instruction
Page - 2
1
Introduction
1.1
General function, benefit in application
The CAN-I/O-Module is an Input/output-module for
peripheral
automation
by
linking intelligent modules to the CAN bus (Controller Area Network).
Such modules are:
Positioning modules for numerical axes, e.g. IMD10, IMD20, IMD40 or CPC12
interface from
isel
Germany
AG
HF-Inverter for working spindles
I/O-Modules for binary (analog) input/output, e.g. CAN-I/O-Modules from
isel
Germany
AG
All CAN-Modules are intelligent, that means they have at least one microprocessor
with integrated on chip or separate CAN-Controller. The CAN-I/O-Modules follow the
CANopen- Standard Device profile for I/O-Modules: CiA Draft Standard Proposal
DS301 V4.0 und DS401 V2.0.
The
advantages
of using I/O-Modules with CAN interface are:
The binary (analog) Inputs and Outputs are available close to the process
sensors (inputs) as well as to the actuators (outputs). A costly, susceptible and
EMC sensitive cabling to the (central) CNC-Controller (CNC-Master, CNC-
Control) will be cancelled.
Additional modules can be integrated and configured in a simply way:
1. Plug node to CAN-Bus
2. Set a new node address for the I/O module
3. Assign the respective software driver (DLL) to the application software (ProNC
or Remote)
There are extensive diagnostic- and test-possibilities because every CAN-I/O-
Module is intelligent. That means, that the modules are able to give status and
error information to the CNC-Master (this is also the CAN Master) on demand.