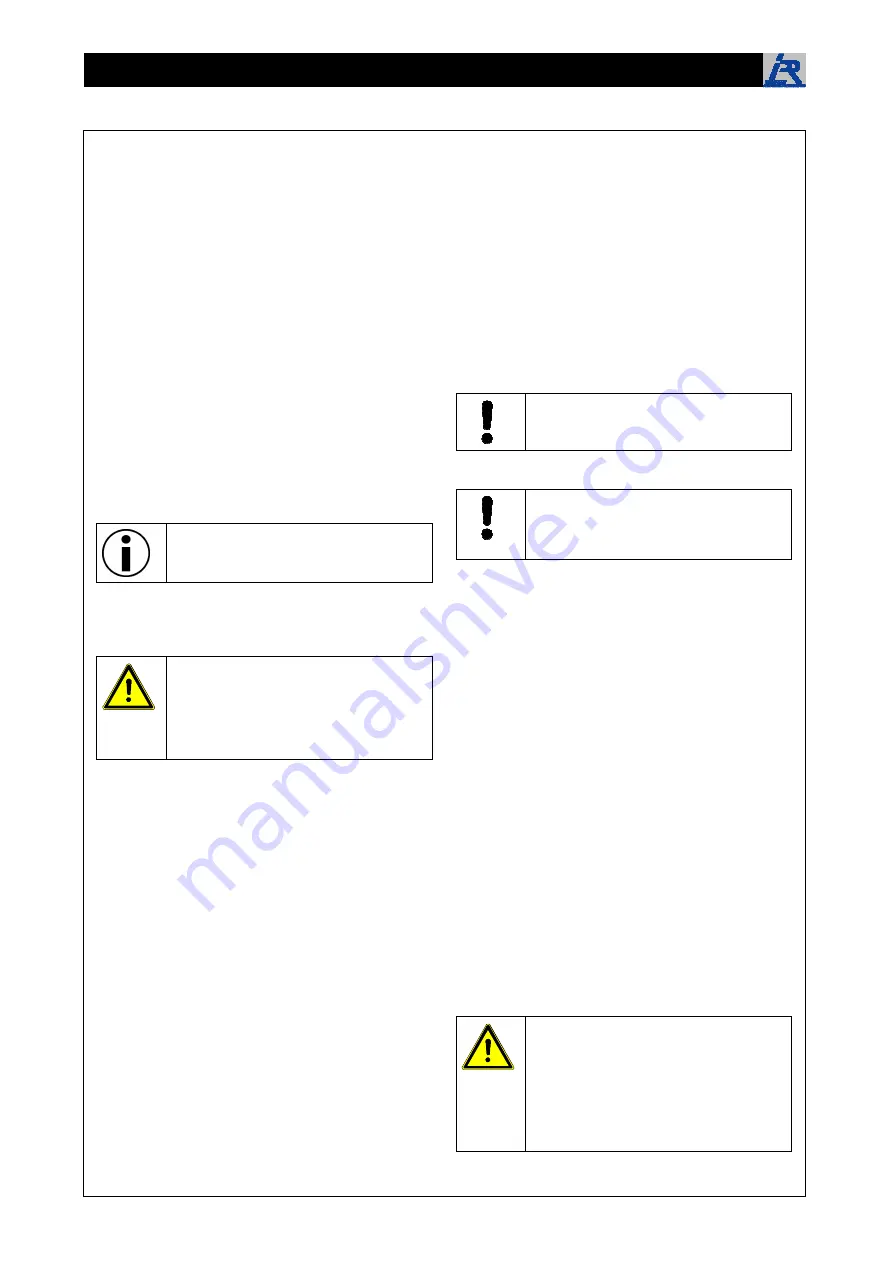
Assembly Instructions
Tool Changer TK-35
WZW_TK-35_V2.0
4
5.2.
23B
Packing
The packing is to be such as to protect the components up to the
assembly stage from transportation damage, corrosion and other
kinds of damage. Thus, the packing is to be left intact and only
removed just before actual assembly.
Only recyclable materials are used for the packing.
Dispose of packaging materials in accordance with the
respectively valid statutory regulations and local requirements.
5.3.
24B
Storage
Store packs under the following conditions:
Do not store outdoors.
Store at a dry and dust-free location.
Do not expose to corrosive media.
Protect from direct sunlight.
Avoid mechanical shocks.
Temperature for storage: 15 °C to 35 °C
Relative air humidity: max. 60%.
In cases of storage exceeding 3 months, regularly check on
the general condition of all the parts and packing. If need
be, either recondition the conservation protection or renew
it.
There may also be information on the packs
themselves extending beyond the requirements set
out here. They are to be correspondingly kept to.
6.
5B
Assembly and commissioning
CAUTION!
Before assembling the tool changer, the energy
supply needs to be disconnected and the line
system relieved of pressure.
Make a note of the safety instructions and general
hazards listed on Page 2.
6.1.
25B
Assembly
The assembly drill holes and pneumatic connections can be
taken from our ongoing catalogue or the internet.
The tool changer is only to be fastened at the threads provided
for the purpose. If needed, manufacture an appropriate adapter
flange or acquire it from the manufacturer.
Tighten the assembly bolts with thread locking adhesive (e.g.
Loctite 4052) or with Schnorr/Nord lock washers, as appropriate.
Provide compressed air at 4,5-8 bar, install pneumatic
connections at the housing; close off any connections not
needed.
Connect electrical signal lines on the robot and tool sides. To this
end, use either sub-D plug connections or IP65 type plug con-
nections depending on version.
6.2.
26B
Commissioning
There is no extra switch-on/off procedure for the system. The
system is ready-for-operations following installation at the ro-
bot/tool and when the compressed air is supplied. Alternatively,
the system is shut down when the robot is immobilized and the
supply of compressed air interrupted.
In the case of a drop in air pressure, the system is automatically
locked. Only when the system is supplied with compressed air
can the tool be disconnected.
7.
6B
Malfunctions
Tool changer does not lock/unlock
Check on supply of air, replace any non-tight lines, if
necessary
Air pressure too low, raise the air pressure
Examine tool changer seals and renew, if necessary
Tool changer does not dock
Foreign matter/contamination present; clean the tool
changer
Ball resetting ring jams or is faulty; grease or possibly renew
8.
7B
Maintenance and repairs
NOTE!
Make a note of the safety instructions and general
hazards listed on Page 2.
8.1.
27B
Cleaning and upkeep
NOTE!
Corrosive cleaning agents could damage the tool
changer seals and result in them ageing more
rapidly.
Make a note of the following when cleaning and tending to the
tool changers:
Use protective caps and the like to firmly close all the
openings
Check that all connections are tight
Use a metal cleaner
Remove any coarse dirt and keep the coupling surfaces
clean.
8.2.
28B
Maintenance
No particular maintenance is necessary under normal operations
given that the Tool changer is used as originally intended.
To retain tool changer functions, we recommend carrying out the
following maintenance steps at least 2x a year:
Clean tool changer
Check screws and connectors, if necessary retighten them
Check tool changer functions, if necessary repair it
Inspect tool changer for outer damage, defects and wear, if
necessary repair it
Check O-ring seal at the sealing surface if necessary
remove it
8.3.
29B
Repairs
The manufacturer provides you with a comprehensive tool
changer repair service.
Repairs are only to be carried out by authorized specialist
personnel.
CAUTION!
Risk of injury from tensioned compression
springs
There is a strongly tensioned compression spring
in the piston chamber on the robot side. This
stored spring tension could result in serious injuries
arising when dismantling.
- Be careful when opening and taking apart