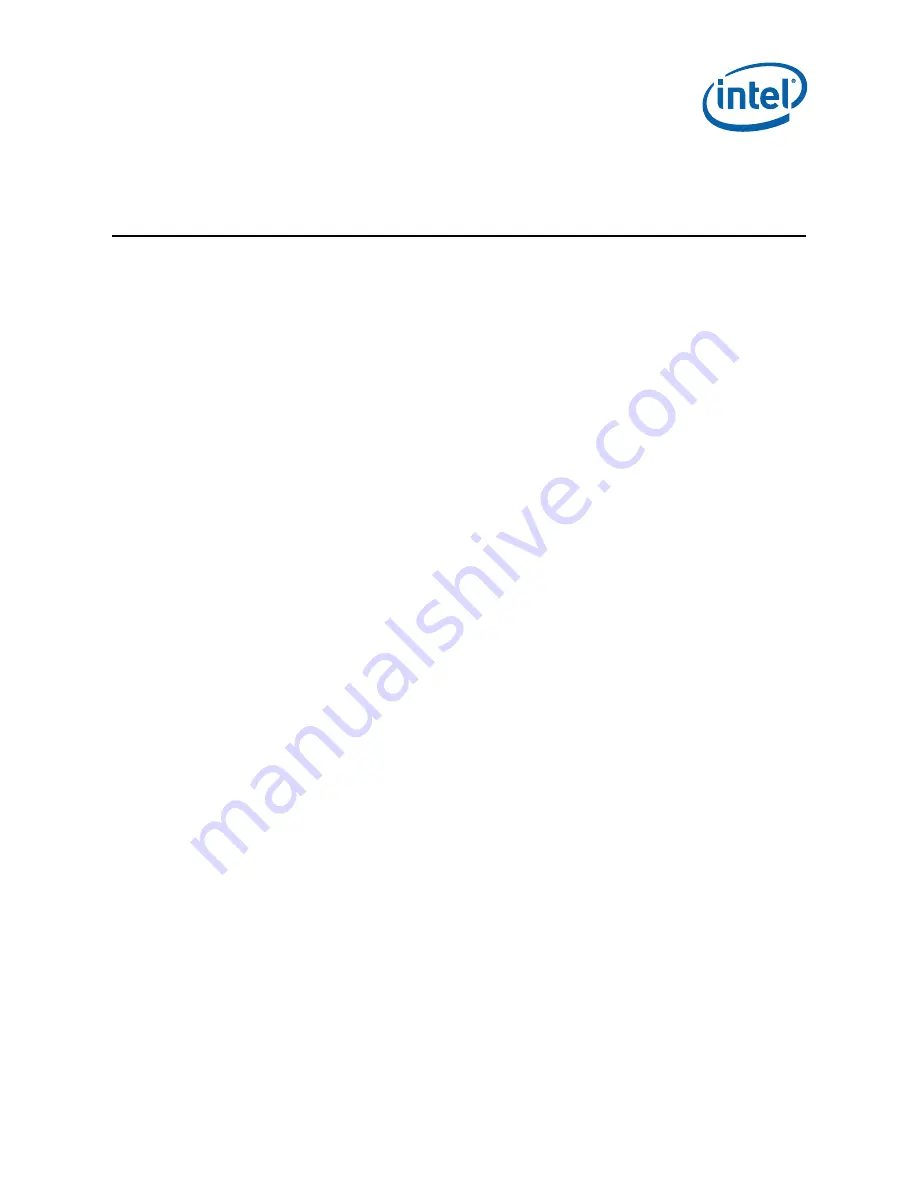
Thermal Metrology
Thermal and Mechanical Design Guidelines
17
3
Thermal Metrology
The system designer must measure temperatures in order to accurately determine the
thermal performance of the system. Intel has established guidelines for proper
techniques of measuring GMCH component case temperatures.
3.1
Case Temperature Measurements
To ensure functionality and reliability of the GMCH the T
C
must be maintained at or
below the maximum temperature listed in Table 2. The surface temperature measured
at the geometric center of the die corresponds to T
C
. Measuring T
C
requires special
care to ensure an accurate temperature reading.
Temperature differences between the temperature of a surface and the surrounding
local ambient air can introduce error in the measurements. The measurement errors
could be due to a poor thermal contact between the thermocouple bead and the
surface of the package, heat loss by radiation and/or convection, conduction through
thermocouple leads, or contact between the thermocouple cement and the heatsink
base (if a heatsink is used). To minimize these measurement errors a thermocouple
attach with a zero-degree methodology is recommended.
3.1.1
Thermocouple Attach Methodology
1.
Mill a 3.3 mm [0.13 in] diameter hole centered on bottom of the heatsink base.
The milled hole should be approximately 1.5 mm [0.06 in] deep.
2.
Mill a 1.3 mm [0.05 in] wide slot, 0.5 mm [0.02 in] deep, from the centered hole
to one edge of the heatsink. The slot should be in the direction parallel to the
heatsink fins (see Figure 5).
3.
Attach thermal interface material (TIM) to the bottom of the heatsink base.
4.
Cut out portions of the TIM to make room for the thermocouple wire and bead.
The cutouts should match the slot and hole milled into the heatsink base.
5.
Attach a 36 gauge or smaller K-type thermocouple bead to the center of the top
surface of the die using cement with high thermal conductivity. During this step,
make sure no contact is present between the thermocouple cement and the
heatsink base because any contact will affect the thermocouple reading.
It is
critical that the thermocouple bead makes contact with the die
(see
6.
Attach heatsink assembly to the GMCH, and route thermocouple wires out through
the milled slot.
Содержание 82G35
Страница 6: ...6 Thermal and Mechanical Design Guidelines...
Страница 10: ...Introduction 10 Thermal and Mechanical Design Guidelines...
Страница 16: ...Product Specifications 16 Thermal and Mechanical Design Guidelines...
Страница 20: ...Thermal Metrology 20 Thermal and Mechanical Design Guidelines...
Страница 30: ...Mechanical Drawings 30 Thermal and Mechanical Design Guidelines Figure 11 GMCH Package Drawing...