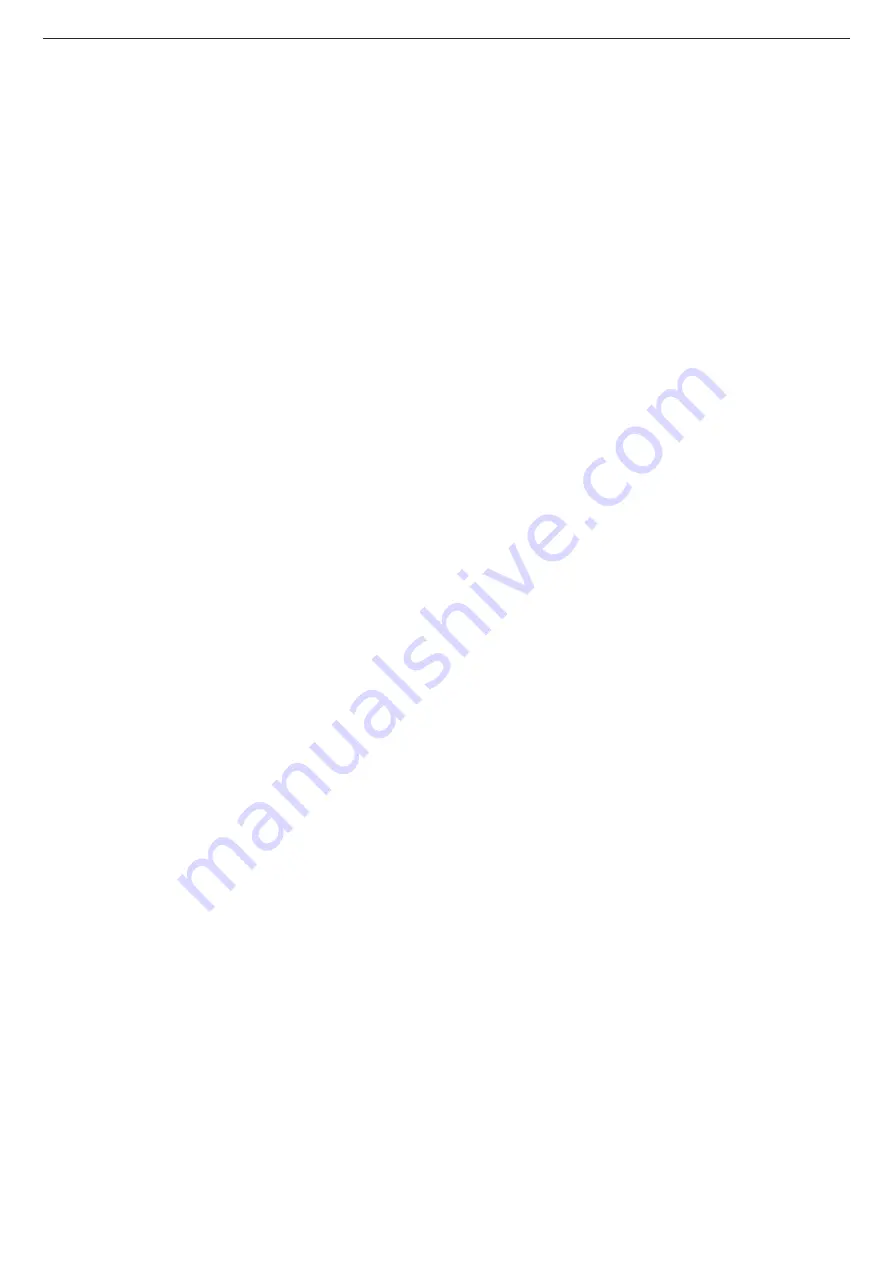
The M-226 and M-440 blenders are suitable for his use in food process. They can be used in any
process which needs to mix solids and liquids as powdered milk, whey, chocolates, sauces, brines,
fertilisers, lactose, stabilisers, etc.
4.3. PRODUCTS TO BE AVOIDED
4.4. APPLICATION
The products to be avoided in order to have a blender optimum operation are:
-
abrasives:
these products deteriorate the mechanical seals and impellers.
-
effervescent:
The gas that emits these products prevents the vacuum from forming and the
powder from falling from the hopper.
-
high temperatures
: it is not advised to work at temperatures above 65 oC. At higher temperatu-
re a product vapours may be given off that may cause the venturi to be blocked. This may also
cause cavitation in the blender as the temperature approaches the boiling point.
-
very high viscosities
: the blenders cannot pump products with a viscosity above 250 cPs.
-
incompatible products:
products incompatible with the various mechanical seals and
elastomers.
Other reasons why the powder may become damp or wet:
-
incorrect liquid-intake flow rate:
A very high flow rate and/or pressure may destroy the blen
-
der vortex, and it would then not be able to pump the liquid with sufficient speed. This can also
happen with a very low flow rate, as it causes the powder to accumulate on the impeller, thus
making it impossible to create the vortex in the centre of the impeller.
-
incorrect pressure:
the differential pressure of the blender must be low (6-9 m), the same as
the pressure at the blender intake which must negative.
-
high viscosity
: a viscous product naturally causes counterpressure. Adding this to the coun-
terpressure caused by the grille leads to very high pressure. It is advisable to remove the grille,
which is an optional part when highly viscous products need to be mixed.
-
high discharge pressure
: if the discharge pipe is too long or its diameter is too small, or visco-
sity is very high, a very high counterpressure will be caused.
If counterpressure increases in the blender, the vortex diminishes thus reducing the mixing capacity
of the solid and liquid ingredients. To resolve these problems the piping must be of correct dimen-
sions, or if necessary, a pump must be fitted to the blender outlet. It may be a centrifugal pump, but
its pumping capacity is limited if the maximum mixture yield is required. it is also important to main-
tain negative pressure at the blender intake.
The amount of powder that can be added is very difficult to define, as a great number of variables are
involved like dampness, fatty material content, microscopic texture (smooth, rough), density, fluidity
(air volume in the product), powder type (granular, flaky, fines), etc.
General Information
INOXPA S.A.U.
02.002.30.02EN · (0) 2021/04
8