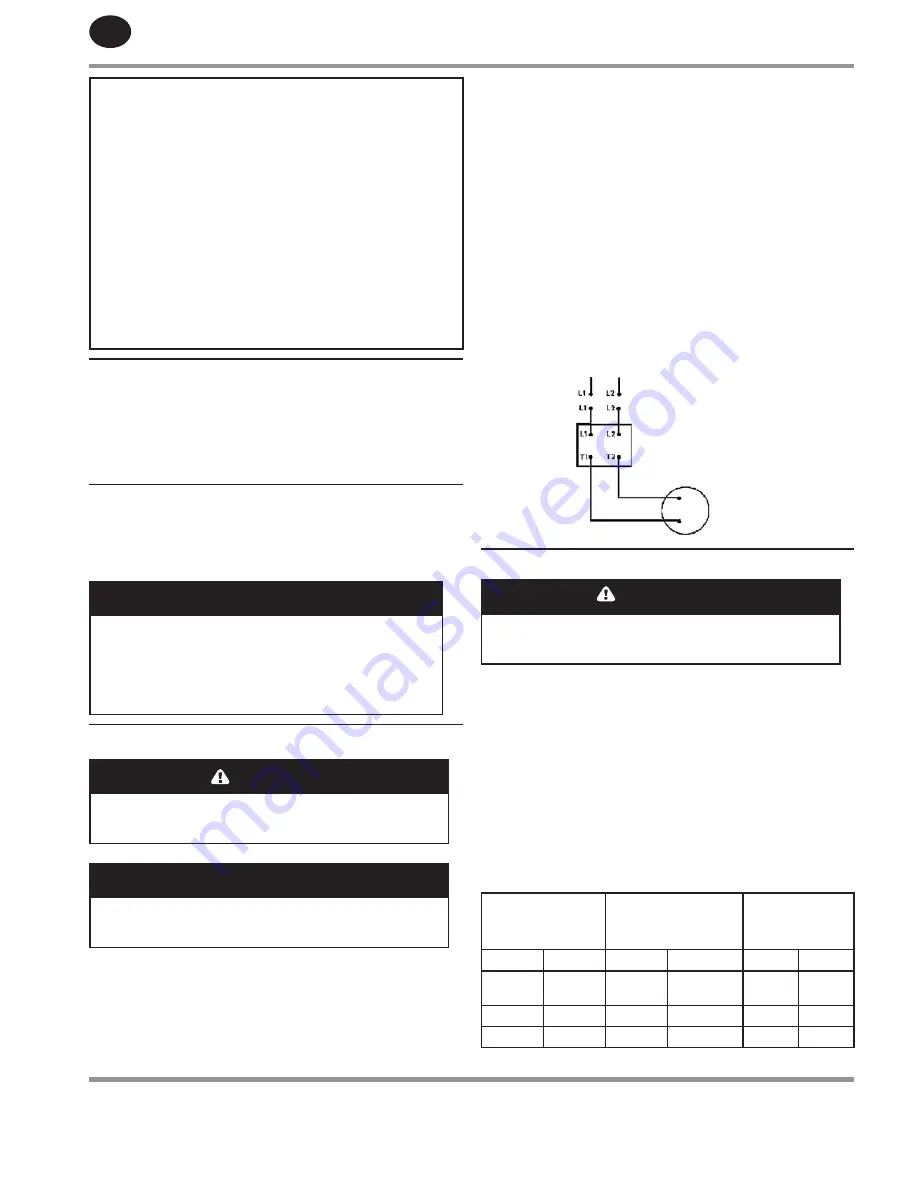
22204945 Rev C
EN-7
EN
SYNTHETIC COMPRESSOR LUBRICANT MATERIAL COMPATIBILITY
LIST
COMPATIBILITY LIST SUITABLE :
FKM (Fluoroclastomer), PTFE, Epoxy (Glass Filled), Oil Resistant Alkyd,
Fluorosilicone, Fluorocarbon, Polysulfide, 2-Component Urethane,
Nylon, POM (Polyoxymethylene/Polyacctel), High Nitrile Rubber (Buna
N. NBR more than 36% Acrylonitrile), Polyurethane, Polyethylene,
Epichlorohydrin, Polyacrylate, Melamine, Polypropylene, Baked
Phenolics, Epoxcy, Modified Alkyds (® indicates trademark of DuPont
Corporation).
NOT RECOMMENDED :
Neoprene, Natural Rubber, SBR Rubber, Acrylic Paint, Lacquer, Varnish,
Polystyrene, PVC, ABS, Polycarbonate, Cellulose Acetate, Low Nitrile
Rubber (Buna N. NBR less than 36% Acrylonitrile), EPDM, Ethylene Vinyl
Acetate, Latex, EPR, Acrylics, Phenoxy, Polysulfones, Styrene Acrylonitrile
(San), Butyl.
GENERAL REQUIREMENTS
The piping, fittings, air receiver tank, etc. must be certified safe for at least
the maximum working pressure of the unit. Use hard-welded or threaded
steel or copper pipes and cast iron fittings that are certified safe for the
unit’s discharge pressure and temperature. DO NOT USE PVC PLASTIC. Use
pipe thread sealant on all threads, and make up joints tightly to prevent air
leaks.
CONDENSATE DISCHARGE PIPING
If installing a condensate discharge line, the piping must be at least one
size larger than the connection, as short and direct as possible, secured
tightly and routed to a suitable drain point. Condensate must be disposed
of in accordance with local, state, and federal laws and regulations.
NOTICE
All compressed air systems generate condensate which
accumulates in any drain point (e.g. tanks, filters, drip legs,
aftercoolers, dryers). This condensate contains lubricating
oil and/or substances which may be regulated and must be
disposed of in accordance with local, state, and federal laws and
regulations.
ELECTRICAL WIRING
WARNING
Electrical installation and service should be performed by a
qualified electrician who is familiar with all applicable local, state
and federal laws and regulations.
NOTICE
This product should be connected to a grounded, metallic,
permanent wiring system, or an equipment-grounding terminal
or lead on the product.
GENERAL
The motor rating, as shown on the motor nameplate, and the power
supply must have compatible voltage, phase and hertz characteristics.
WIRE SIZE
The electrical wiring between the power supply and electric motor varies
according to motor horsepower. Power leads must be adequately sized
to protect against excessive voltage drop during start-up. Information
for selecting the proper wire size and securing connections should be
provided with the motor. If not, refer to the National Electric Code (NEC) or
applicable local, state and federal laws and regulations. If other electrical
equipment is connected to the same circuit, the total electrical load must
be considered in selecting the proper wire size. DO NOT USE UNDERSIZE
WIRE.
FUSES
Refer to the National Electric Code to determine the proper fuse or circuit
breaker rating required. When selecting fuses, remember the momentary
starting current of an electric motor is greater than its full load current.
Time-delay or “slow-blow” fuses are recommended.
Single-Phase Wiring
COMPRESSOR LUBRICATION
CAUTION
Do not operate without lubricant or with inadequate lubricant.
Ingersoll Rand is not responsible for compressor failure caused
by inadequate lubrication.
SYNTHETIC COMPRESSOR LUBRICANT
We recommend Ingersoll Rand synthetic compressor lubricant from start-
up. See the WARRANTY section for extended warranty information.
ALTERNATE LUBRICANTS
You may use XL-300 or a comparable petroleum-based lubricant that is
premium quality, does not contain detergents, contains only anti-rust,
anti-oxidation, and anti-foam agents as additives, has a flashpoint of 440°F
(227°C) or higher, and has an auto-ignition point of 650°F (343°C) or higher.
See the petroleum lubricant viscosity table below. The table is intended
as a general guide only. Heavy duty operating conditions require heavier
viscosities. Refer specific operating conditions to
Ingersoll Rand
for
recommendations.
Temperature
Around Compressor
Viscosity at 100
°
F
(37.8
°
C)
Viscosity Grade
°F
°C
SUS
Centistokes
ISO
SAE
40 &
below
4.4 &
below
150
32
32
10
40-80
4.4-26.7
500
110
100
30
80-125
26.7-51.0
750
165
150
40
RELEASED 05/Apr/2018 15:16:08 GMT
Содержание SS5L5
Страница 3: ...22204945 Rev C EN 3 EN May 2015 RELEASED 05 Apr 2018 15 16 08 GMT...
Страница 17: ...22204945 Rev C EN 17 EN RELEASED 05 Apr 2018 15 16 08 GMT...
Страница 23: ...RELEASED 05 Apr 2018 15 16 08 GMT...
Страница 24: ...ingersollrandproducts com 2018 Ingersoll Rand RELEASED 05 Apr 2018 15 16 08 GMT...