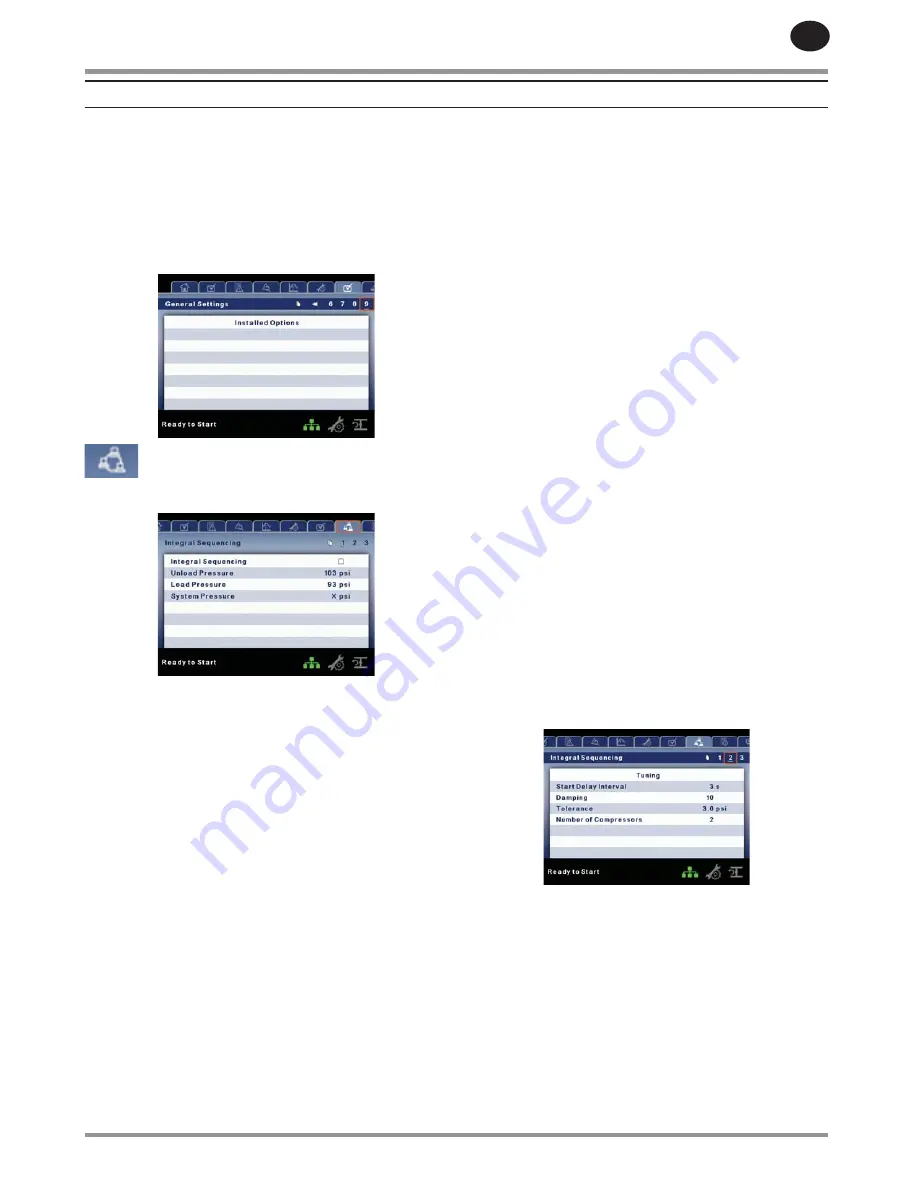
EN
80448608 Rev B
31
NIRVANA OIL-FREE COMPRESSOR
PAGE 9 - OPTION MODULE INFORMATION
The option module information screen allows the user to see
which software options have been installed in the controller.
An option module that is installed will show up with an “X”
in the appropriate box. The option part number is displayed
with the option name.
If no options are installed, this screen will not appear on the
controller.
INTEGRAL SEQUENCING FOLDER
PAGE 1 - SETUP
Integral Sequencing allows the compressor to be networked
with up to three other compressors (fixed or variable
speed) to maintain a stable system pressure by loading and
unloading compressors as needed. Integral sequencing
requires no additional hardware other than a serial two wire
connection daisy chained between all compressors in the
system, connected to port Com 1 on the controller.
For a compressor to be a member of the integral sequencing
system, the communication control setpoint in the operator
settings tab must be enabled and the compressor must be
started via the local start button. Integral sequencing system
will never start and stop machines, only load and unload
them. Integral sequencing relies on Auto-Restart to turn off
the compressor motor when not needed.
Note that the compressor’s address in the integral sequencing
system is defined by the Airbus address that is set on
the general settings folder. Also note that the pressure
signal used to determine when to load or unload another
compressor is based on the pressure reading from the
compressor assigned as the integral sequencing master.
The master controller MUST be started and running in
the sequence. Otherwise, compressors will revert to
their local setpoints.
•
•
•
If the master controller is telling a slave controller to
load and the slave’s local pressure is above its immediate
stop setpoint, the slave will unload locally, and remain
unloaded until pressure falls below the target setpoint.
Integral Sequencing –
Enabling Integral Sequencing
chooses this compressor to be the sequence Master. The
master’s system pressure sensor will be the pressure signal
used for the system. The default is disabled. Please make
sure all compressors are set up for integral sequencing
before enabling this function. It is important that only
one compressor in the system have this setpoint enabled,
otherwise system behaviour could be impacted. This setpoint
should also only be modified while the compressor is
stopped. Note that the Integral Sequencing master does not
have to be the compressor assigned Airbus address 1.
Unload Pressure –
Determines the pressure at which a
compressor will be unloaded by the system. The system
unload pressure should always be set lower than the local
immediate stop setpoint of compressors in the system. Note
that when under system control, the compressor will ignore
the local pressure setpoints except for protective functions.
Load Pressure –
Determines the pressure at which a
compressor will be loaded by the system. . The system
unload pressure should always be set lower than the local
immediate stop setpoint of compressors in the system. Note
that when under system control, the compressor will ignore
the local pressure setpoints except for protective functions.
System Pressure –
Shows the current pressure reading that
the system is using for control. This will only be shown on the
sequence Master controller. This will normally be the package
discharge pressure, however, if the compressor is equipped
with a remote sensor, this will be the remote pressure.
PAGE 2 - TUNING
Start Delay Interval –
Determines the amount of time
between loading compressors. This prevents all compressors
from loading at once. This setpoint should be set to the
longest starting time of any compressor in the system. In
general, this will be equivalent to the star/delta transition
time for a fixed speed machine, or ramp time for a VSD
machine.
Damping –
The pressure control “Damping” setting which is
used to tune how quickly the system responds to pressure
deviations. The default is 1.0 and should not normally be
changed.
•
•
RELEASED 06/Feb/2018 13:48:37 GMT