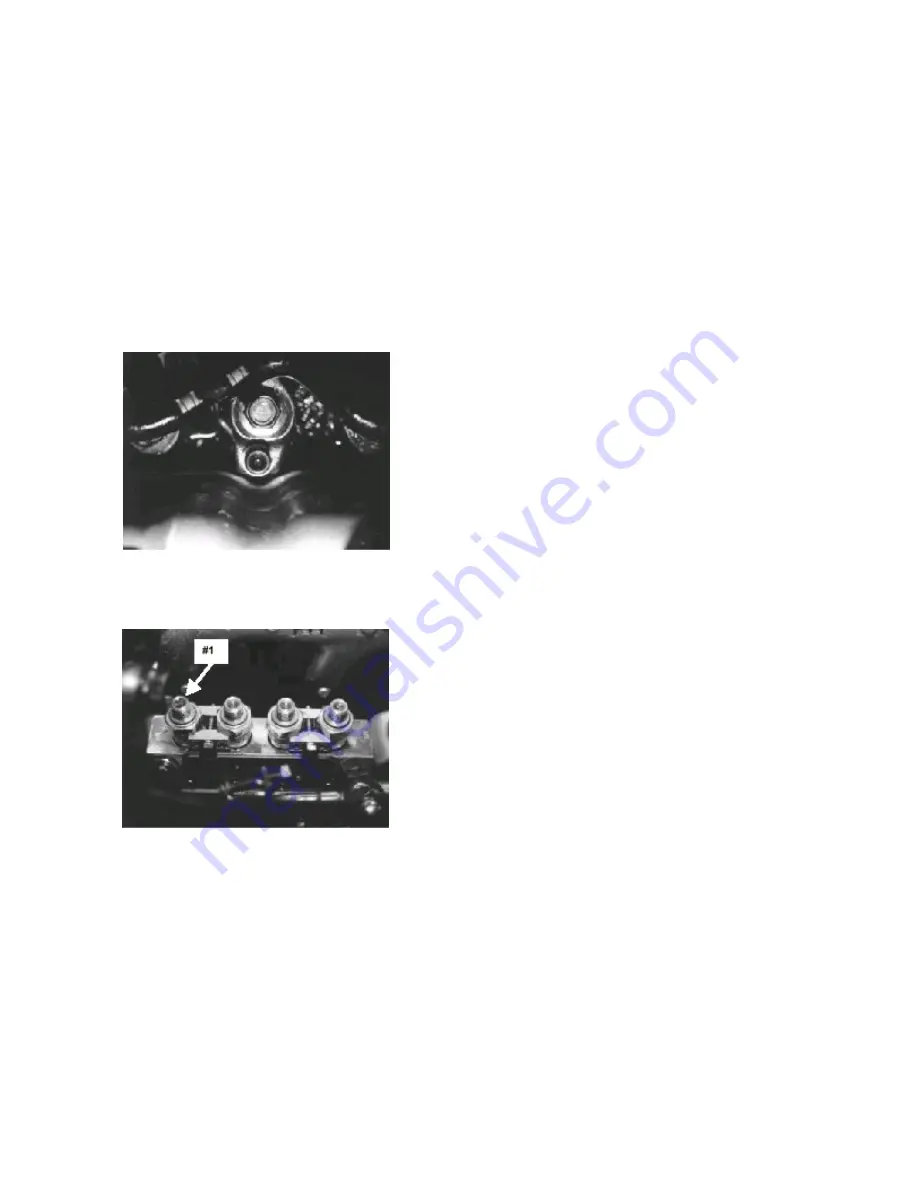
25
III. Engine Servicing Procedures
Spill Port Timing
Spill-port timing is a precise method of measuring the initial injection of fuel by the pump and the
duration of injection. It is a standard procedure used by IR when timing Zexel pumps. This
procedure is a very precise method of timing fuel because it shuts off fuel to the high-pressure
chambers relative to the position of the piston.
Disconnect and remove the #1 injection pipes
from the nozzle and fuel pump.
First clean the fuel pump to prevent any foreign
materials to enter the pump. Then remove the
delivery valve holder from the injection pump.
Then disassemble the delivery valve holder to
remove the valve and valve spring. Replace the
delivery valve holder. Tighten to 29-33 Ft. lbs.
Place the stop solenoid in the on or up position
to allow full fuel flow. Bring the TDC mark to
90° BTDC. Cover the valve assembly with a rag
and prime the pump. Uncap the fuel return to
bleed any air in the system. Then rotate the
engine clockwise until fuel quits flowing out of
the holder. This is the beginning of the injection.