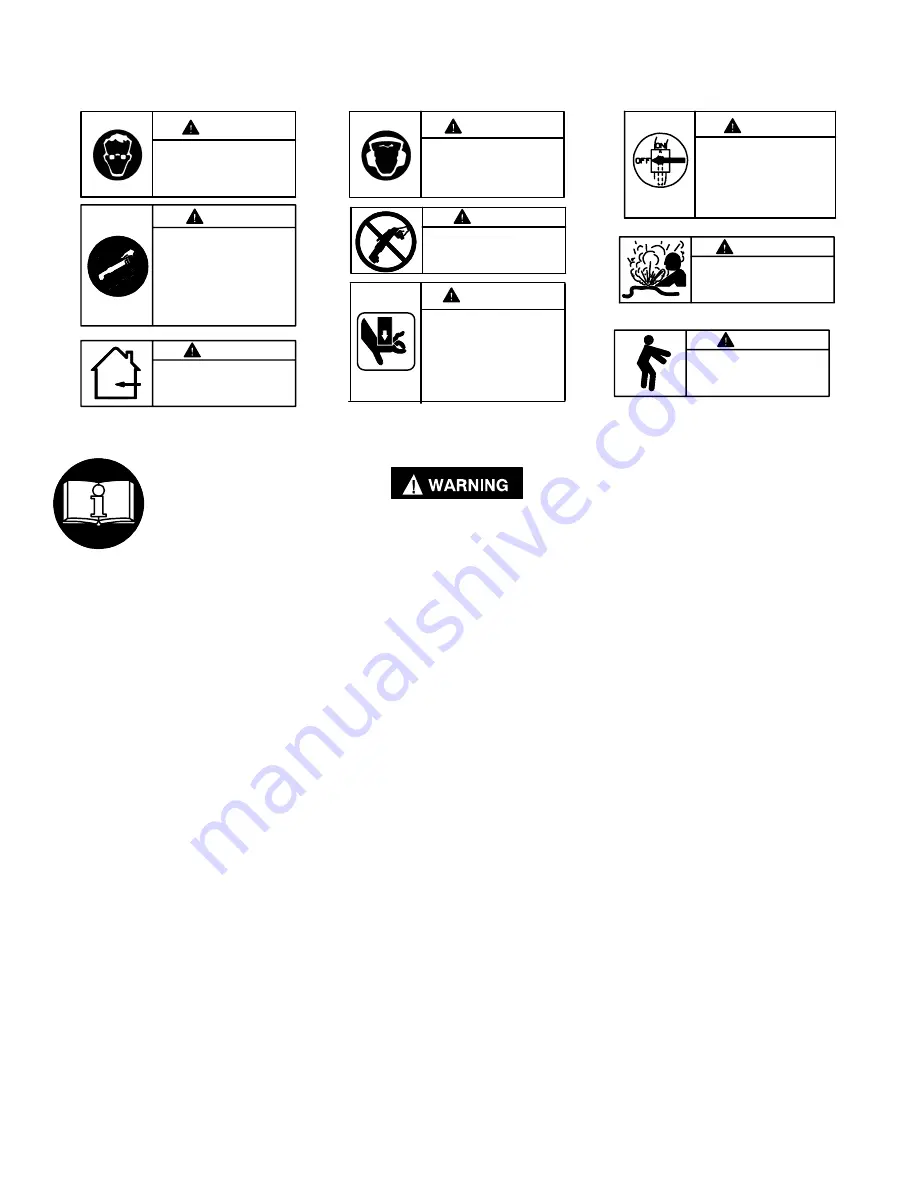
4–3
WARNING LABEL IDENTIFICATION
Always wear eye protection
when operating or perform-
ing maintenance on this tool.
WARNING
WARNING
Always wear hearing
protection when operating
this tool.
Always turn off the electrical
supply and disconnect the
power cord before installing,
removing or adjusting any
accessory on this tool, or
before performing any
maintenance on this tool.
WARNING
WARNING
Do not use damaged, frayed
or deteriorated power cords.
WARNING
Keep body stance balanced
and firm. Do not overreach
when operating this tool.
WARNING
INDOOR USE ONLY.
WARNING
The Torque Reaction Bar must
be positioned against a
positive stop. Do not use the
Bar as a dead handle and take
all precautions to make certain
the operator’s hand cannot be
pinched between the Bar and
a solid object.
Powered tools can vibrate in
use. Vibration, repetitive mo-
tions or uncomfortable posi-
tions may be harmful to your
hands and arms. Stop using
any tool if discomfort, tingling
feeling or pain occurs. Seek
medical advice before resum-
ing use.
WARNING
Do not carry the tool by the
cord.
WARNING
WHEN THIS MODULE IS USED WITH AN AIR POWERED TOOL
IMPORTANT SAFETY INFORMATION ENCLOSED.
READ THIS MANUAL BEFORE OPERATING TOOL.
IT IS THE RESPONSIBILITY OF THE EMPLOYER TO PLACE THE INFORMATION
IN THIS MANUAL INTO THE HANDS OF THE OPERATOR.
FAILURE TO OBSERVE THE FOLLOWING WARNINGS COULD RESULT IN INJURY.
PLACING TOOL IN SERVICE
•
Always operate, inspect and maintain this tool in
accordance with all regulations (local, state,
federal and country), that may apply to hand
held/hand operated pneumatic tools.
•
For safety, top performance, and maximum
durability of parts, operate this tool at 90 psig (6.2
bar/620 kPa) maximum air pressure at the inlet
with 3/8” (10 mm) inside diameter air supply hose.
•
Always turn off the air supply and disconnect the
air supply hose before installing, removing or
adjusting any accessory on this tool, or before
performing any maintenance on this tool.
•
Do not use damaged, frayed or deteriorated air
hoses and fittings.
•
Be sure all hoses and fittings are the correct size
and are tightly secured.
•
Always use clean, dry air at 90 psig maximum air
pressure. Dust, corrosive fumes and/or excessive
moisture can ruin the motor of an air tool.
•
Do not lubricate tools with flammable or volatile
liquids such as kerosene, diesel or jet fuel.
•
Do not remove any labels. Replace any damaged
label.
USING THE TOOL
•
Always wear eye protection when operating or
performing maintenance on this tool.
•
Always wear hearing protection when operating
this tool.
•
Keep hands, loose clothing and long hair away
from rotating end of tool.
•
Note the position of the reversing lever before
operating the tool so as to be aware of the direction
of rotation when operating the throttle.
•
Anticipate and be alert for sudden changes in
motion during start up and operation of any power
tool.
•
Keep body stance balanced and firm. Do not
overreach when operating this tool. High reaction
torques can occur at or below the recommended
air pressure.
•
Tool shaft may continue to rotate briefly after
throttle is released.
•
Air powered tools can vibrate in use. Vibration,
repetitive motions or uncomfortable positions may
be harmful to your hands and arms. Stop using
any tool if discomfort, tingling feeling or pain
occurs. Seek medical advice before resuming use.
•
Use accessories recommended by Ingersoll–Rand.
•
Use only impact sockets and accessories. Do not
use hand (chrome) sockets or accessories.
•
This tool is not designed for working in explosive
atmospheres.
•
This tool is not insulated against electric shock.
(Continued on page 4–4)
Содержание 150 D Series
Страница 6: ...4 6 Dwg TPA1724 ...