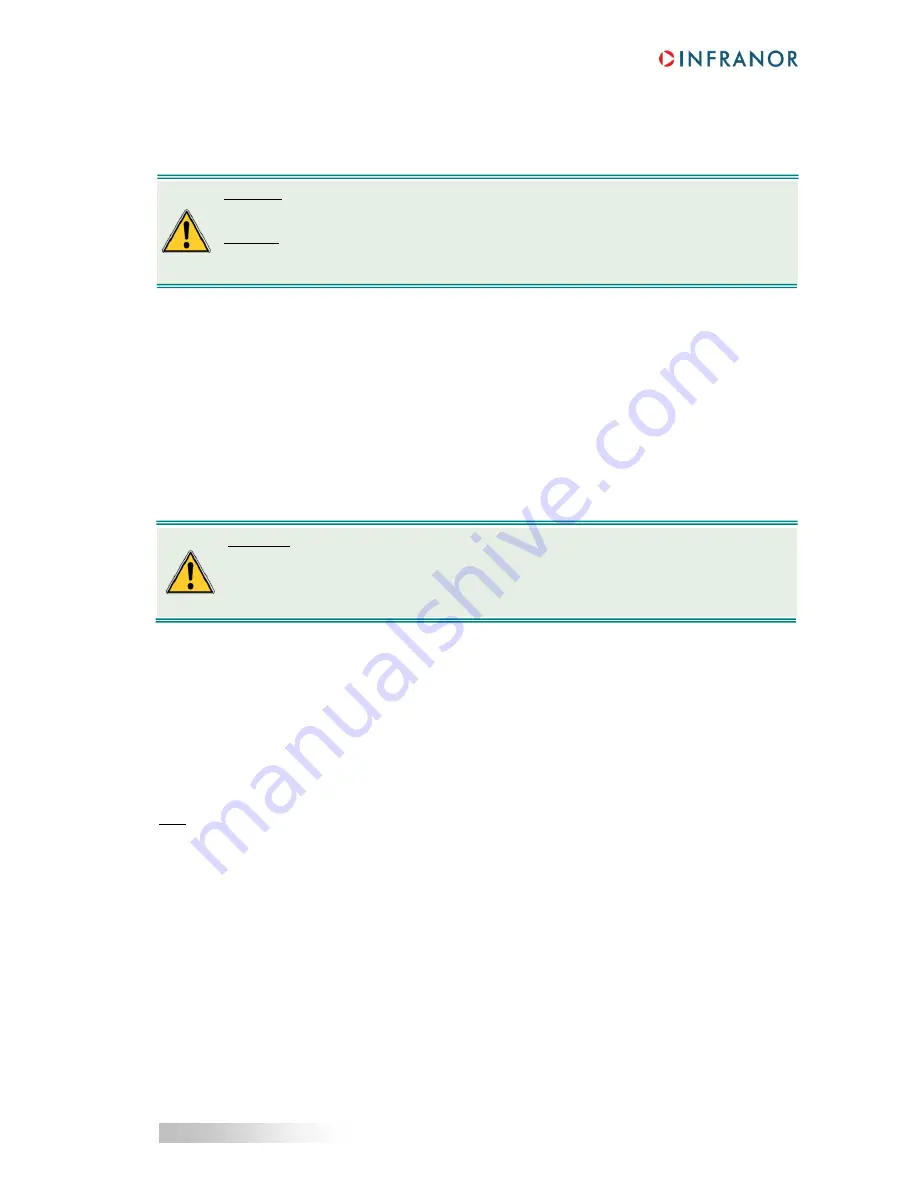
65
Chapter 4 - Connections
XtrapulsPac Installation Guide
4.6.5 - Serial link and CAN communication cables
Serial link and CAN communication cables must also be shielded according to the shield connection
recommendations above.
4.7 - FIRST POWERING OF THE DRIVE
4.7.1 - Very important
Check the connections, especially of the 24 V
DC
and power supplies. Check that the housing serigraphy actually
corresponds to the power connections.
The 400 V
AC
connection of a 230 V drive will destroy it!
If a logic input is software configured with the Enable function, it must be disabled.
Check for the braking resistor specifications if connected in place of the internal braking resistor.
Check for the correct groundings as well as the 360° shield connections.
4.7.2 - Connection of the 24 V
DC
supply
The red
Err
LED on the front panel must be flashing ("Undervolt." error).
The
AOK
signal (pins 4 and 14 of X2) is closed. The power voltage relay (Rpu) can then be controlled according
to the recommendations of Chapter 4, section 1 (connection diagram). The connection must be made in
compliance with the X8 connector serigraphy.
4.7.3 - Connection of the mains power supply
The red
Err
front panel LED must be unlit.
Note: If a fault occurs, the red
Err
LED remains continuously lit.
4.7.4 - Starting procedure
See
XtrapulsPac
– User Guide
.
CAUTION!
Control cables (resolver, serial link, CAN) and power cables must be connected and disconnected
with the drive
turned OFF
.
Reminder:
The power voltage may remain several minutes at the power capacitor terminals.
A contact with high voltage may involve severe physical damage.
WARNING !
During the machine adjustments, drive connection or parameterization errors may involve
dangerous axis movements. It is the user's responsibility to take all necessary steps in order to
reduce the risk of uncontrolled axis movements during the operator's presence in the pertaining
area.