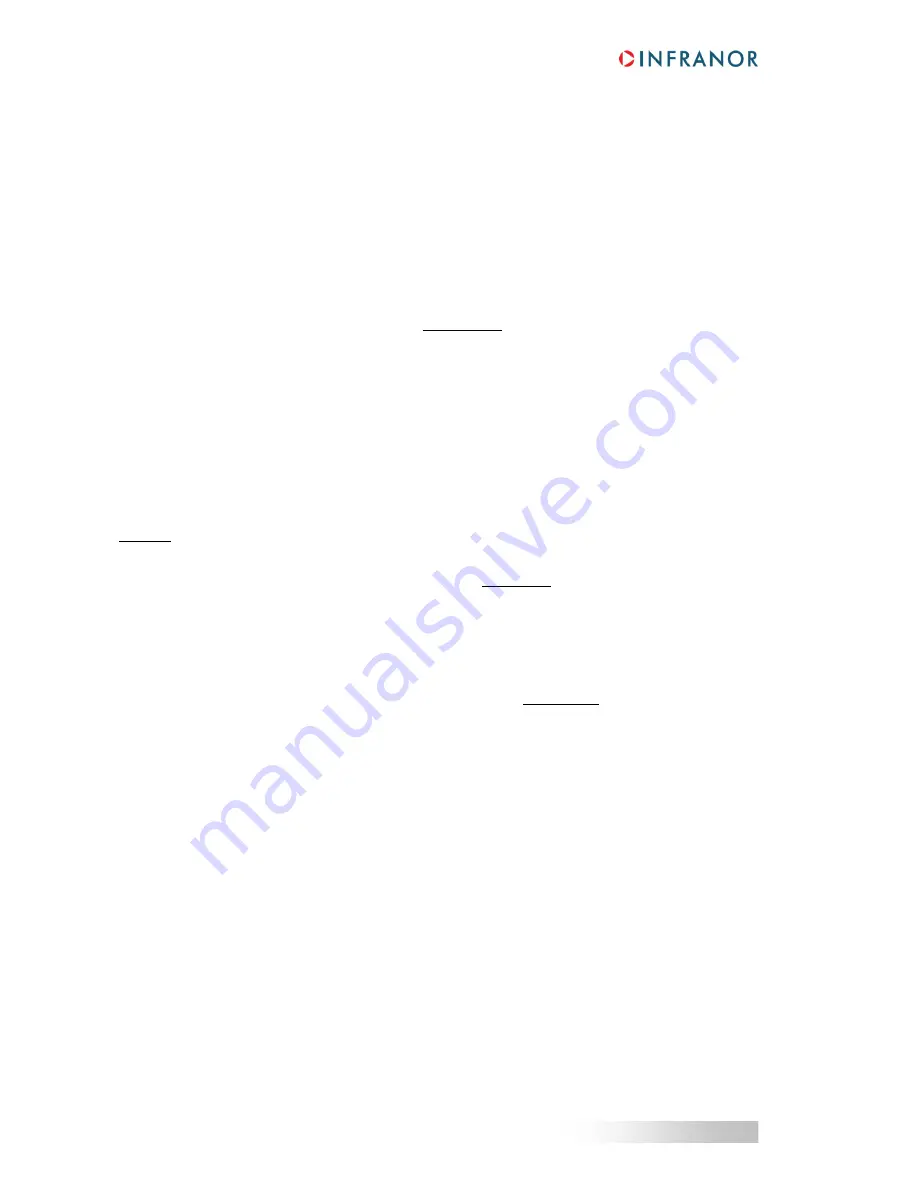
64
Chapter 4 - Connections
XtrapulsPac Installation Guide
4.6.4 - Motor, resolver and encoder cables
Motors, resolvers and encoders are grounded via their housing.
Cable inputs must be made by means of metal connectors with collars allowing the 360° shield connection.
The resolver cable must be pair twisted and shielded (sin, cos, ref.). Motor cables MUST also be shielded and
connected over 360° at both ends, as shown on the shield connection picture of section 4.6.3.
The encoder inputs A, B, C, D, Z and R require pair twisted and shielded cables. The shield must have a 360°
connection via metallic collars at both ends.
Check that the voltage drop in the power supply lines of the encoder cable is complying with the technical
specifications of the encoder. The voltage drop value for a given cable is calculated as follows:
²]
[
]
[
].
[
.
10
.
40
]
[
6
mm
S
mA
I
m
L
V
U
C
with
U:
voltage drop in volts
Lc:
cable length in meters
I:
encoder current in milliamps (see technical specifications)
S:
section in square millimetres
Due to this voltage drop:
an encoder with a wide power supply voltage range should be selected,
if the encoder has power supply SENSE feedback lines, they can be connected to the power supply lines in
order to reduce the voltage drop by the half (the SENSE feedback signal is not used in this drive).
Example
The application requires a linear Heidenhain encoder, supplied with 5 V ±5 % / 300 mA and 25 m cable length.
Supply voltage: 5 V ±5 %
U
max
= 0.25 V
Minimum section: S = 1.2 mm².
Such a cross section is difficult to obtain, so the user can:
either connect the SENSE feedback signal lines to the power supply lines, so the required wire section will be
the half (0.6 mm²),
or use the same encoder type but in a version which allows a power supply voltage from 3.6 to 5.25 V / 300
mA. Minimum power voltage 3.6 V
U
max
= 1.4 V
Min. section: S = 0.21 mm².
Brake equipped motors must also have their brake cables shielded in order to be EMC compliant.
Maximum cable length:
100 m.
For cable length >25 m, we advise:
- the use of the maximum cable section allowed by the connectors,
- the mounting of a reactance with an inductive value between 1 % and 3 % of the motor inductive value for the
motor cable. The reactance inductive value must be taken into account in the calculation of the current loops.
The current rating of the reactance must be higher than or equal to the drive rating.
The reactance must be mounted at the drive output.
Due to the use of a reactance, a shielded cable is not mandatory anymore.
A more complex sinus filter type B84143V x R127 by company Epcos may also be mounted instead of the
reactance.
UNDESIRABLE EFFECTS OF MOTOR CABLES LONGER THAN 25 M:
- Heating of the power module, the motor and the cable.
- High overvoltage on the motor windings, involving a shortening of their life time.
The reactance reduces the undesirable effects on motor and drive but it may be quite heated. This requires an
appropriate fan.