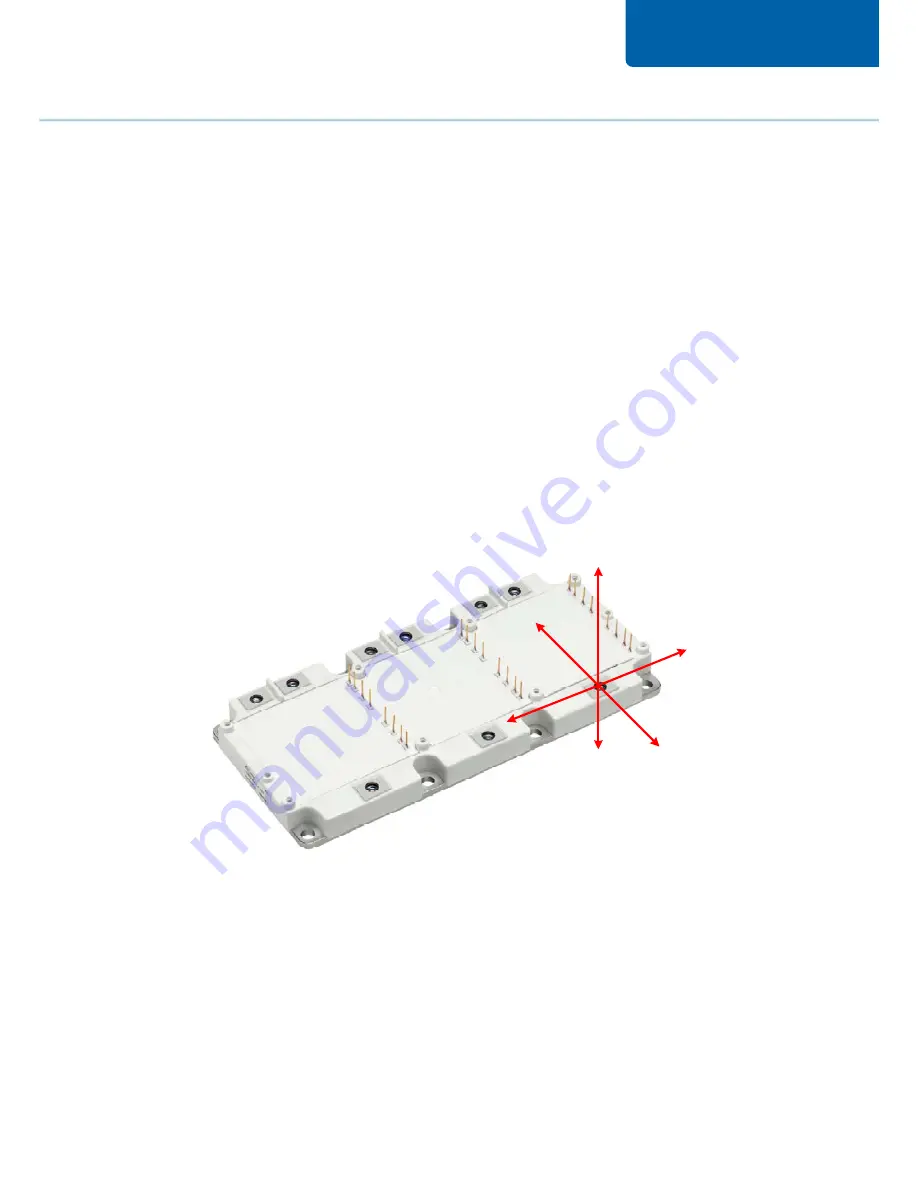
N 2010-03
r 2009
Application Note AN 2010-08
V2.0, August 2010
7
Connecting the Bus Bars to the Power Terminals
The DC power side should be connected with a laminated DC bus bar in order to keep the
switching overvoltage as low as possible by minimising the stray inductance. Adherence to
the maximum permissible voltage at the power terminals and at the IGBT chip is to be
assured according to the RBSOA data in the datasheet.
For the connection of the power terminals DIN M6 screws are required which comply at least
with class 6.8, in combination with a suitable washer and spring washer or complete
combination screws. These should be tightened with the recommended torque of M
min
=2.5
Nm to M
max
=5.0 Nm.
When selecting the screws length the layer thickness of the connected parts has to be
subtracted from the total length of the screws. The effective length of engagement into the
module thread may not exceed the maximum specified depth of 10mm.
The connected parts have to be mounted to the power terminals in such a way that the
specified static forces are not exceeded during assembly or later in operation, as shown in
Figure 10.
PLEASE NOTE: The values of the specified forces refer only to static forces. No oscillation
(swinging) forces are allowed here.
<100 N
<100 N
<100 N
<100 N
<100 N
200 N
Figure 10
Maximum permissible static pull and push forces at the power terminal
of the HybridPACK™ 2.