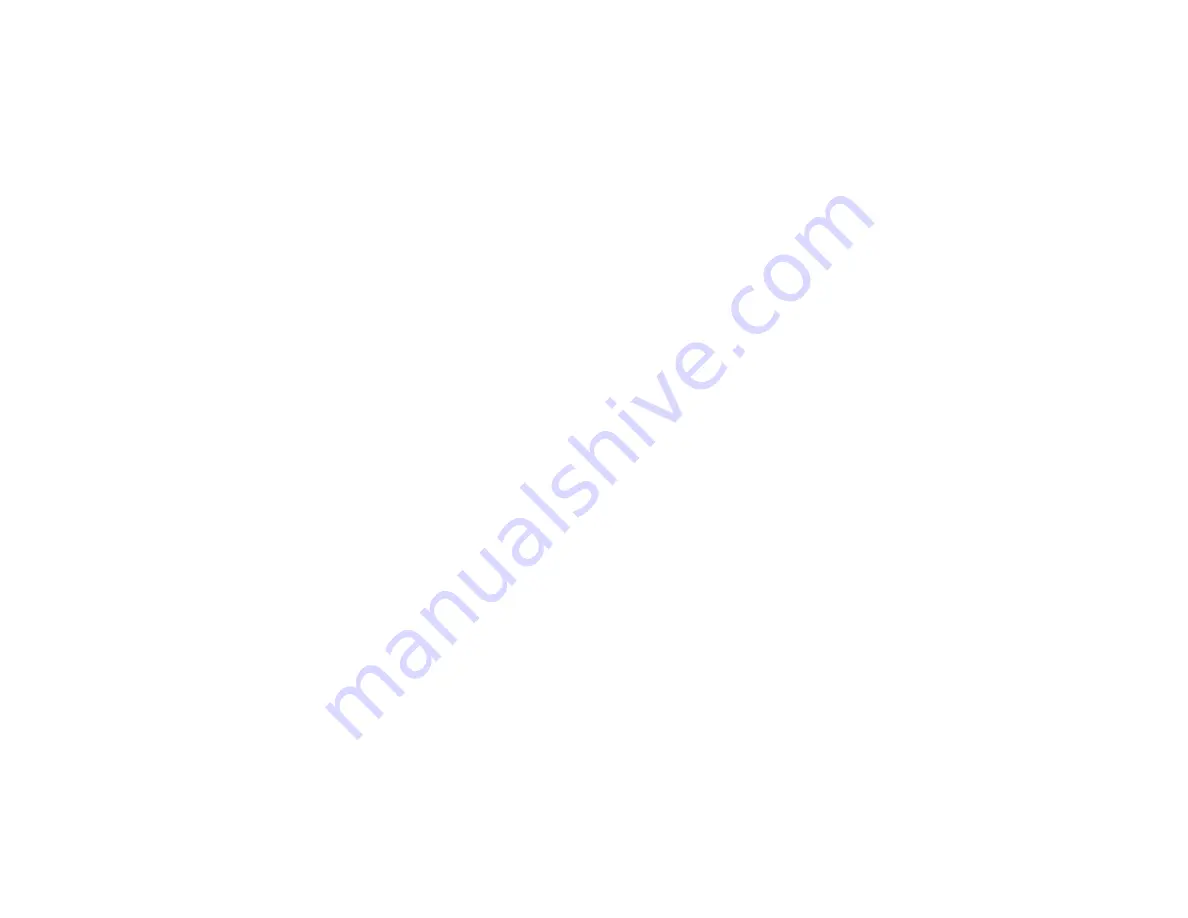
ResMark 5000 High-Resolution
Appendix B: Theory of Operation
400386 Operations Manual Rev A
Page 39
Print Head Daisy Chain
Print heads attach to the system (production line) in a daisy chain configuration via Ethernet or wireless. The Primary print head is the beginning
of the daisy chain and has the photosensor plugged into it. All data is fed downstream from the primary print head to the daisy-chained heads.
If connecting the system via hard cables, an Ethernet cable can be connected from the HMI / Controller to the Primary print head CPU (J6). The
next downstream head will connect to the Primary head via an Ethernet cable between the output port (J7), and the input CPU port (J6) on the
next print head. This I/O repeats for all downstream heads. The maximum number of daisy chain print heads is eight.
One power supply can power up to two print heads and an HMI, independent of printer size (Mark 2 or Mark 4). An additional power supply is
required for every two print heads in the daisy chain.
When print messages are sent to the Primary print head, all downstream daisy chain print heads receive the same information. When a
production line is running, photocell and encoder data are dynamically communicated to all the print heads to maintain timing and stay in sync.
Print Trigger Photosensor
The photosensor detects when a product is about to pass by the PM nozzle plate and signals the CPU to start a print cycle. The photosensor
signal is active low, and it must remain low for at least one encoder pulse. Once a print cycle starts, it continues to completion regardless of what
the photosensor signal does.
The system is compatible with through-beam, retro-reflective, and diffused photosensors that work at 24VDC and have a current sinking (or open
collector) output. The photosensor plugs into the print head CPU (J5).
E
ncoder
The encoder determines the time period between the printing of individual columns, or the print speed. As a product's speed increases, the time
period between columns must decrease, that is, the print speed must increase, to maintain consistent column-to-column spacing. The system
has two encoder options, external and internal. Use the external encoder when the conveyor speed fluctuates. Use the internal encoder when
the conveyor speed is constant.
The
external encoder
is a 24VDC optical encoder. The encoder's wheel is sized such that the encoder outputs 300 pulses per inch of product
travel. The external encoder plugs into the print head CPU (J4), and its signal is used to time the sending of column data to the print head.
The
internal encoder
signal is a constant frequency pulse stream generated on the print head CPU. This pulse stream is divided down in the
CPU to generate the desired speed / timing.