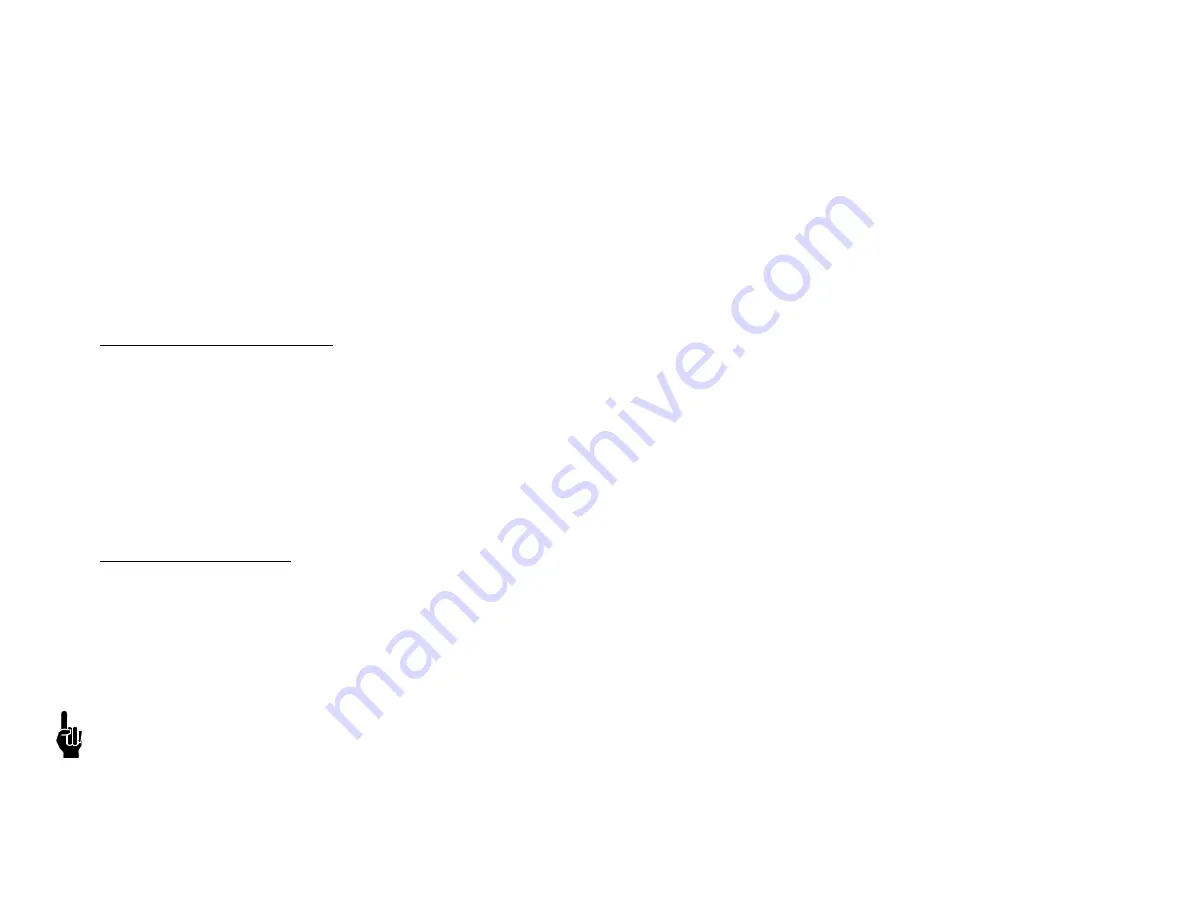
ResMark 5000 High-Resolution
Appendix B: Theory of Operation
400386 Operations Manual Rev A
Page 36
Appendix B: Theory of Operation
Functional Description
The ResMark 5000 high-resolution ink jet system prints text, autocodes (such as product counts or time and date stamps), barcodes, and/or graphics onto
products as they travel by conveyor past stationary print heads. Print can be placed on any one of, or a combination of, the product's sides. The conveyor
speed is monitored using a variable speed encoder or a built-in fixed speed encoder. Products are detected using a photosensor. The information to be printed
is defined as a message whose elements are created and controlled in software and maintained on the ResMark Ink Supply Module.
ResMark 5000 Mark 2 and Mark 4 Print System
The ResMark 5000 print system consists of an Ink Supply Module (ISM) and Printer Module (PM). The ISM is comprised of a Smart CPU printed circuit board,
ink cartridge, ink manifold, ink pump, vacuum waste system, and male coupling. The PM contains a female receiver coupling, ink management fluidics, and
piezoelectric print engine.
Ink Supply Module (ISM)
Ink flow and pressure is managed by the ISM along with ink waste recovery. When the ink cartridge is inserted into the septum receiver, two needles puncture
the septum on the cartridge and allow for ink to flow into the manifold up to a control point level. Atmospheric pressure is allowed through a vent on the rear of
the ISM. When the system is printing, capillary action pulls the ink from the ISM into the PM, and to the piezoelectric print engine. The action of ink flow from
printing or priming lowers the ink level in the manifold reservoir to the control point where atmospheric pressure allows the flow of ink from the cartridge. In
addition to ink flow, the ISM manages ink recirculation and priming via an ink pump. When either the
Recirculation
or
Clean / Prime
feature buttons are
activated, the ink and vacuum pumps turn ON, and the print is disabled. During
Recirculation
, the ship cap should be installed. When using the recirculation
feature, downstream pressure builds allowing optimal conditions for removing unwanted air from the ink supply system and wetting of the print engine ink
pathways. Finally, the ISM provides a means of ink / waste collection from the use of the
Clean / Prime
feature.
The ISM CPU electronics control all functionality of the printer system. These functions include all fluidic management, LED’s, button presses, wireless and
wired connectivity, photosensor and encoder communication, message storage, and all print imaging features. Once a message has been sent to the printer
and requested to print, external HMI / controller connectivity is not necessary (i.e. Smart Print Head).
Printer Module (PM)
The fluidics in the PM appropriately manage ink as it enters and exits the ink ports of the print engine. When the system is placed in
Recirculation
mode, with
the ship cap installed, ink pressure and flow from the ISM through the PM moves air bubbles back to the ISM and is ventilated from the system.
The piezoelectric inkjet print engine has a nozzle plate with an array of orifices and a corresponding array of piezoelectric crystals. These crystals expand and
contract rapidly based on voltage being supplied to them. Very small ink pulse waves are created as a result of piezoelectric crystals expanding rapidly, creating
a pressure pulse to force ink droplets out the orifices. The print engine also incorporates a heater to control the head temperature, allowing ink viscosity to be
maintained over a wide spread of ambient temperatures. The print engine must be at the correct operating temperature before printing and can be monitored
via the LEDs located on the rear of the ISM. They show when the heater is ON (irregular modulation) and when the print engine is at the appropriate
temperature (steady ON light).
NOTE
: Since ink is fed to the print engine via gravity, it is important to maintain the print head at a level position during operation.