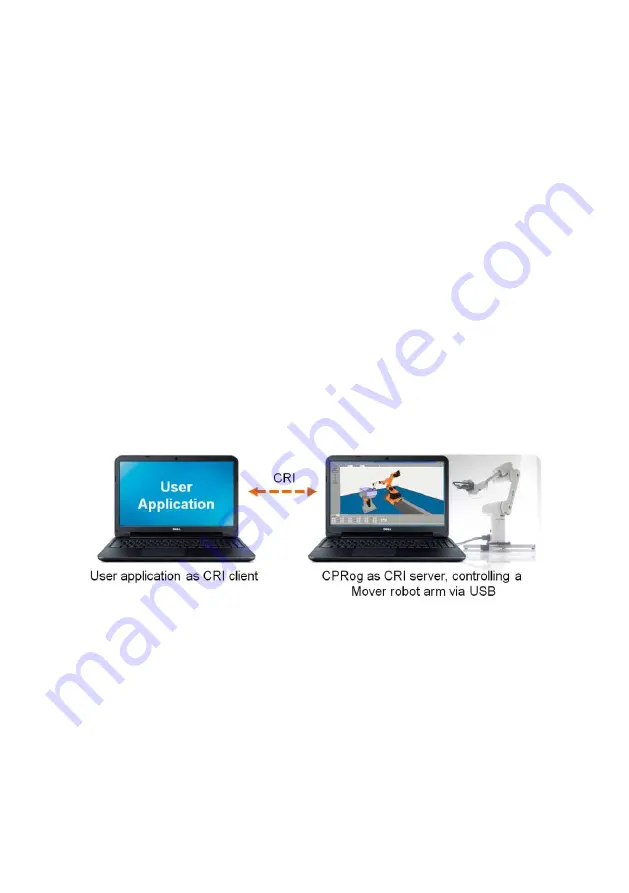
72
12.2.
PLC Interface
The PLC interface (PLC = Programmable Logic Controller) allows the integration of the Robot
into a production system controlled by a PLC. In this way, the Robot can work without manual
interaction. Also, it is possible to connect third party control panel with push buttons to
simplify and restrict operation of the robot in a production environment.
Specifically, this interface assigns certain digital IO channels to special functions, such as:
inputs: "reset/enable motors", "start/stop program”, "reference";
outputs: "noFault", "enabled" and "program running".
Further details are available on the Wiki (section "PLC interface", http://wiki.cpr-
robots.com/).
12.3.
CRI Ethernet Interface
The Commonplace Robotics Interface (CRI) allows the Robot to be controlled via Ethernet.
The Robot can be moved, programs can be uploaded and executed. It allows the development
of a custom robot control software. The control software (TinyCtrl) on the Embedded
Computer and igus
®
Robot Control on the Windows PC communicate via the CRI interface.
This interface makes it possible to combine the igus
®
Robot Control functions with
application-specific algorithms, such as a teleoperation system or a database. The CRI
documentation and a C# sample project for a client can be downloaded on request.
Содержание Drylin Delta
Страница 1: ......
Страница 2: ...1...
Страница 14: ...13 4 Electrical Connections 4 1 Overview Figure 4 1 Overview of electrical connections...
Страница 26: ...25 Figure 5 1 Schematic wiring of the safety components with the Support Module...
Страница 79: ...78...
Страница 80: ...79...
Страница 81: ...80...