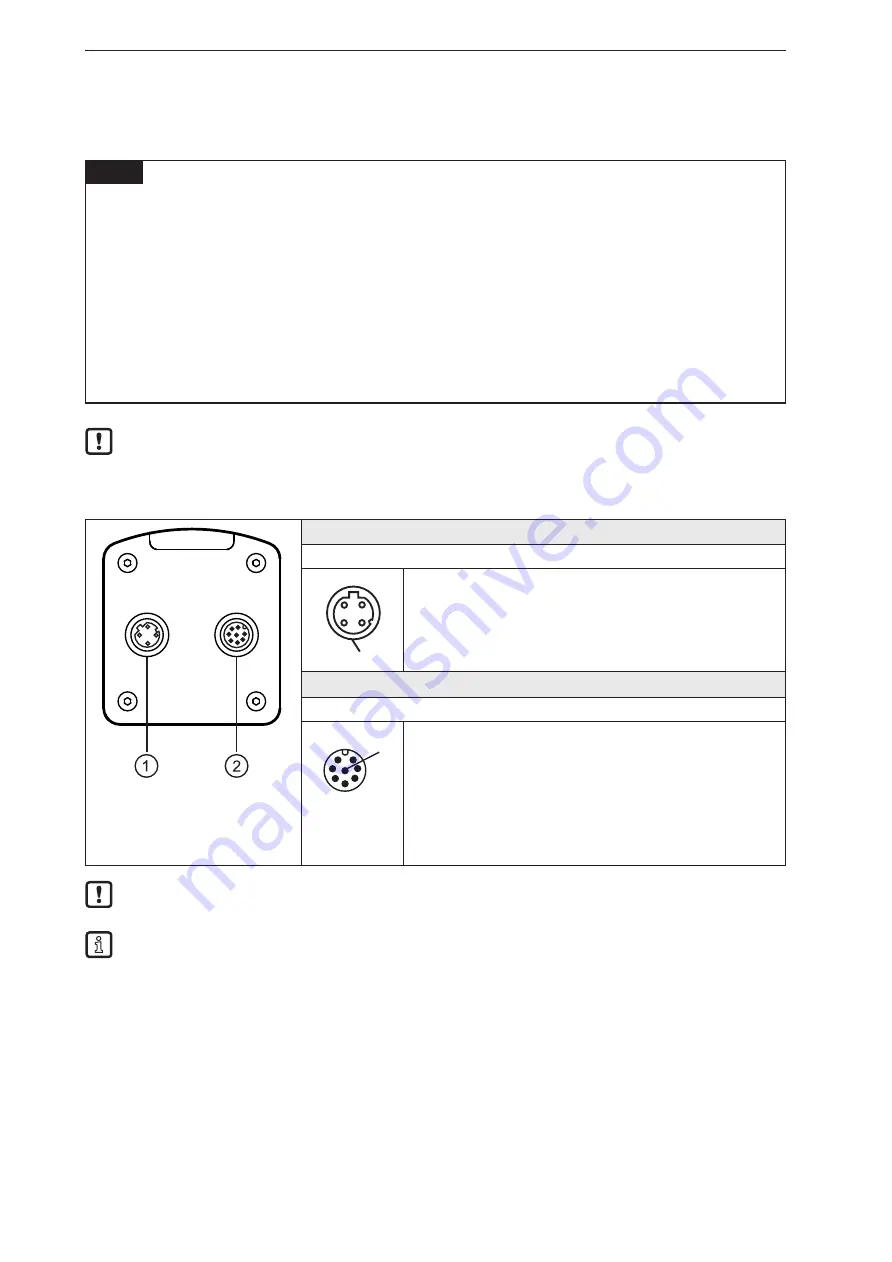
3D sensor
10
7. Electrical connection
Observe the following instructions before electrical installation.
NOTE
The device must be connected by a qualified electrician. Observe the electrical data in the data sheet.
Device of protection class III (PC III).
The electrical supply must only be made via PELV circuits.
Electric supply must correspond to UL61010-1, chapter 9.4 - Limited Energy:
The overcurrent protection device must switch off a current of 6.6 A in 120 s. For the correct rating of
the overcurrent protection device take the technical data of the sensor and wiring into account.
The separation of external circuits must comply with UL61010-2-201, fig. 102.
For cable lengths > 30 m use an additional protection against surge voltages to IEC 6100-4-5.
Disconnect power before connecting the device.
For the scope of validity cULus:
Minimum temperature rating of the cable to be connected to the field wiring terminals: 70 °C.
7.1 Wiring
①
Ethernet
M12 socket, D-coded, 4 poles
1 TD +
2 RD +
3 TD -
4 RD -
S Shield
②
Power supply
M12 connector, A-coded, 8 poles
6
2
1
4
5
7
3
8
1 U+
2 Trigger input
3 GND
4 Switching output 1 - (digital or analogue)
5 Switching output 3 - ready
6 Switching output 2 - (digital)
7 Switching input 1
8 Switching input 2
Cover unused Ethernet connection with the protective cap (E73004).
Tightening torque 0.6...0.8 Nm.
The behaviour of the switching inputs and outputs can be set with the software ifm Vision Assistant.
The setting PNP or NPN always applies to all switching inputs and outputs.
When installing actuators and sensors make sure that the setting is correct
(e.g. photoelectric sensors for triggering).
The switching outputs can also be operated as pulse outputs which reset their switching signal
after an adjustable time.
The analogue output provides current / voltage against GND.